By nature, the design process is complex; it often involves thousands of decisions, sometimes over a period of many years, with numerous interdependencies, and under a highly uncertain environment. Design can involve a large number of participants and decisions makers, trade-offs between multiple competing design criteria with inadequate information, and intense budget and schedule constraints1.
The influence of the design phase on the outcome of any projects both technically and economically is immense. It is in the design phase that the customer’s ideas and speculations are conceptualized into a physical model, and the customer’s needs and requirements are defined into procedures, drawings and technical specifications. Many authors have however stated that planning and control in design are substituted by chaos and improvising, causing poor communication, lack of adequate documentation, deficient or missing input information, unbalanced resource allocation, lack of coordination between disciplines, and erratic decision-making1. According to Tzortzopoulos and Formoso2, the traditional design process fails to minimize the effects of complexity and uncertainty, to ensure that the information available to complete design tasks is sufficient, and to reduce inconsistencies within construction documents. Lean Design is introduced as a way for reducing waste, unnecessary uncertainty, and improving value generation in the design phase.
What is Lean Design?
Lean Design is an extension of Lean Thinking, which has been applied to the production phases in several industries including manufacturing, construction, and healthcare. According to Emmitt et al.3, moving Lean Thinking upstream should create significant potential to deliver value throughout the whole process. That is because most of the costs and much of the quality in a construction project are locked in long before production launch, and therefore the design process will be crucial not only to ‘do things right’ but also, more importantly, to ‘do the right things’. The Lean philosophy, with its focus on minimizing waste and maximizing value, is therefore recommended to be applied as early as possible in a building process.
While Lean has already shown significant results in the manufacturing and construction industries, there is a clear difference between designing and building. According to Ballard & Zabelle4, Designing produces the recipe and Building prepares the meal. This is the ancient distinction between planning and doing. The principles of Lean are therefore modified in Lean Design to accommodate the nature of the design process. Ballard & Zabelle4 compare designing to a good conversation, from which everyone leaves with a different and better understanding than anyone brought with them. How to promote this conversation (iteration) and differentiate between positive (value generating) and negative (wasteful) iteration are some of the central principles of Lean Design. Hansen and Olsson5 states that Lean thinking in design has at least two main objectives: to find the best design to meet the client's needs in order to support effectiveness, efficiency and user satisfaction; and to define systems, structures and materials to ensure effective, streamlined construction.
Lean Design considers three perspectives to describe the design process (1) Transformation (transformation of inputs into outputs); (2) Flow (flow of material and information through time and space); and (3) Value (the generation of value for customers), rather than the more traditional view of the design process as only a transformation process4. The ‘transformation view’ has been the dominant view of production and is best described as ‘getting the task done’. Several practices such as work breakdown structure support this view. The ‘flow view’ emphasizes on the interconnectivities of tasks with the aim of shortening lead times and elimination of waste, including reduction of rework, use of team-based approaches to avoid time-consuming iterations, and release of information in small batches to allow for rapid feedback from team members. The ‘value view’ stresses the use of analysis of requirements and constraints to deliver what matters to the customer6. The Lean Design process involves all three perspectives, even though each perception is orthogonal to one another (e.g., having just the transformation view does not guarantee that the flow and value view are taken into account and vice versa). Table 1 below compares the different views.
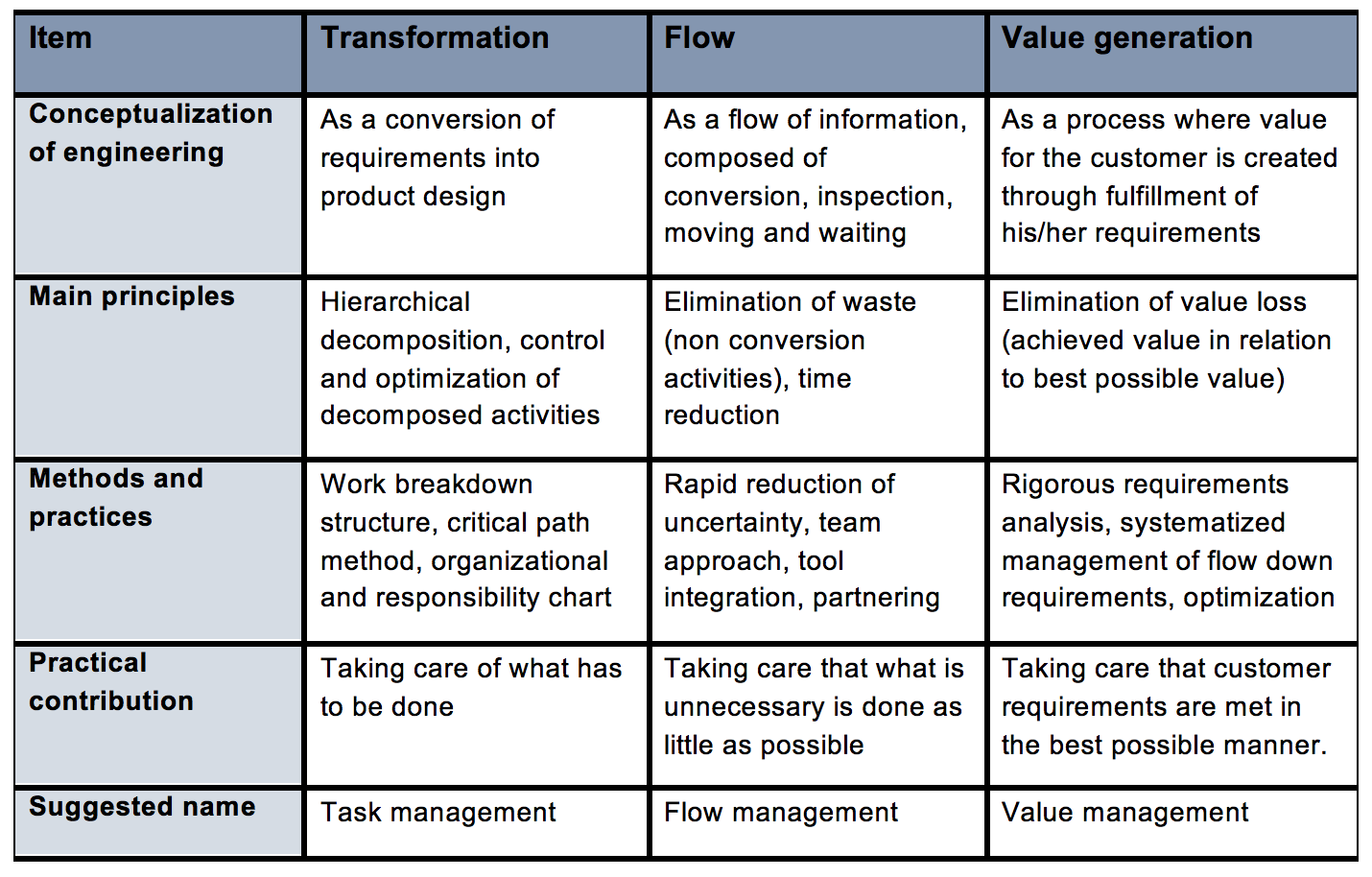
Design is understood as encompassing not only product design, but also process design. Product design determines what is to be produced and used, while process design determines how to produce it or use it. In traditional design approach, the product is first designed, then ‘thrown over the wall’ to someone else to decide how or if it can be built, operated, altered, etc. Lean Design aims to integrate design of product and process, meaning that considering and deciding how to build and use something can be done at the same time as considering what to build7.
References
1. Freire, J., & Alarcon, L. F. (2002). Achieving Lean Design Process: Improvement Methodology. Journal of Construction Engineering and Management, 128(3), 248-256.
2. Tzortzopoulos, P., & Formoso, C. T. (1999). Considerations on application of lean construction principles to design management. Proceedings 7th Annual Conference of the International Group for Lean Construction (IGLC), (ss. 335–344). Berkeley,California.
3. Emmitt, S., Sander, D., & Christoffersen, A. K. (2004). Implementing value through lean design management. Proceedings 14th Annual Conference of the International Group for Lean Construction (IGLC), (ss. Copenhagen, Denmark).
4. Ballard, G., & Zabelle, T. (2000). Lean Design: Process, Tools, & Techniques. Lean Construction Institute.
5. Hansen, G. K., & Olsson, N. O. (2011). Layered Project–Layered Process: Lean Thinking and Flexible Solutions . Architectural Engineering and Design Management, 7(2), 70-84.
6. Ballard, G., & Koskela, L. (1998). On the agenda of design management research. Proceedings 6th Annual Conference of the International Group for Lean Construction (IGLC). Guarujá, Brazil.
7. Ballard, G., Tommelein, I., Koskela, L., & Howell, G. (2002). Lean construction tools and techniques . I R. Best, & G. de Valence, Design and Construction: Building in Value (ss. 227-255). Oxford: Butterworth-Heinemann.