What is Takt time planning?
Takt time planning is a work structuring method. Let’s decouple that a little bit.
‘Takt time’ is a term used in manufacturing to describe pacing work to match the customer’s demand rate. ‘Work structuring’ is the practice of scheduling out work and is a part of designing a production system. Takt time planning then, is one method for work structuring around a set pace of work. The goal of Takt time planning is to create a reliable plan, with the input of the entire team, which balances workflows for specific phases of work.
Setting the paces of work is an iterative design problem with several related questions. What work should be paced? What should the pace be? How big are the spaces to work through? How should different sets of work be paced? It is important to start this process early in a project, because whether design professionals realize it or not, they are critical to defining the means and methods when they create design documents and specifications1.
Why Do We Use Takt Time?
Simply put, we need a systematic way of improving production if we are to improve over the long term. When activities are all moving at different paces, then projects naturally become more chaotic. Stable flows help reveal bottlenecks, which are the areas to improve upon. This is not a new idea. Liker and Meier2 describe this as part of the continuous improvement spiral (Figure 1). The spiral shows the relationship for how improvement can occur in an iterative fashion through creating stability, pacing work, and standardizing.
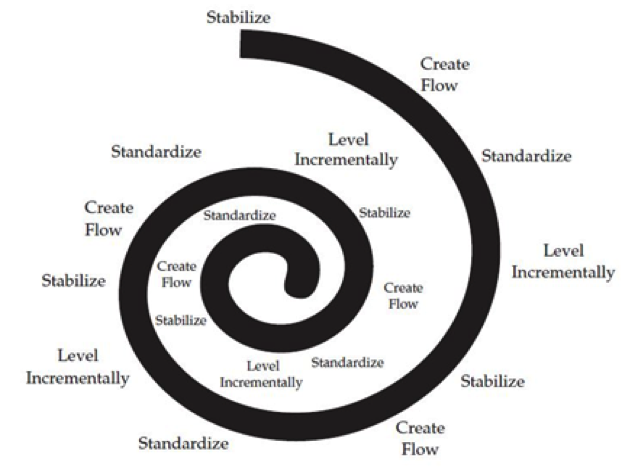
It is important to think about both the size of the batches we release and the pace work is released at on site, for each affects the overall project duration. In most cases, an overall schedule duration improves through handing off smaller batches of work. The caveat is that this makes the paces that activities move through areas much more dependent upon each other.
In general, there is always a better way to plan the work when you start to understand how much work is on the floor for different trades, where it is located, and how people want to work through the space. Achieving flow for a work phase is a difficult task, even when using the Last Planner system, pull planning work phases, and identifying work sequences. That’s because identifying the trade sequences and the required work handoffs is only one component. Designing flow into the schedule requires additional work, and Takt Time Planning is a method to do just that.
Example: Overhead Takt Time Plan
Figure 2 is a simple example schedule resulting from Takt time Planning. The phase of work covers overhead MEP installation for plumbing, duct-work, and electrical conduit. In this example, the work is planned with plumbing (blue) going first, followed by duct (red), and electrical conduit (green). The work is all paced at a 5 day takt time, moving through quadrants on two floors. The work starts in 1A and ends in 2D.
In this example, the work begins on July 15 and completes on September 24. Had the work been scheduled using the same quantities, but with activities requiring full floors instead of quadrants, then the work would’ve finished on November 9. In conclusion, small batches of work are important!
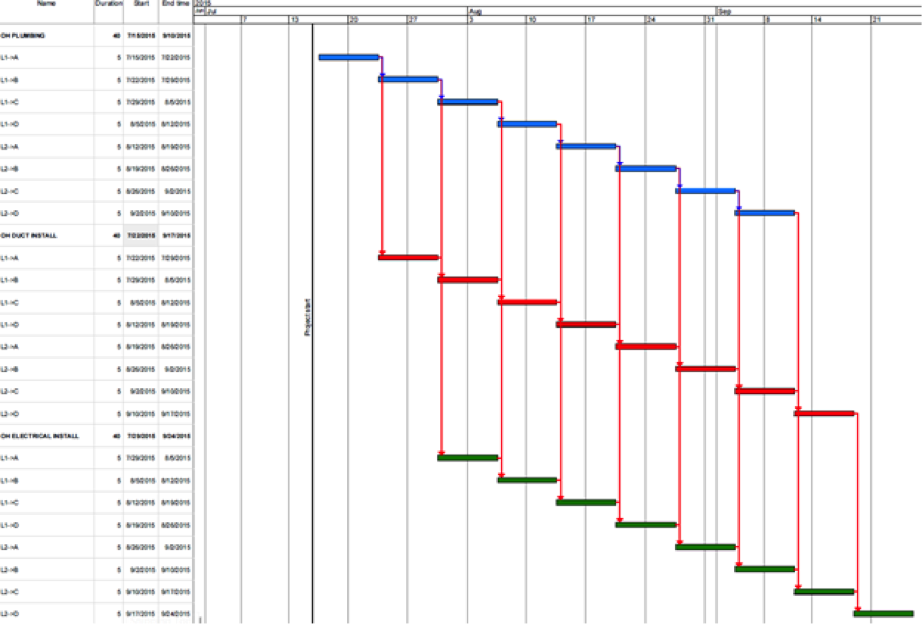
Future Posts
Takt time planning is a very dense topic, and this post was just a brief overview of what it is and how it works. Future posts will go more into detail on the history of Takt Time Planning and location based scheduling, how to use the method, examples of how it has been implemented, and how it ties in with other Lean Construction concepts.
References
1. Tsao, C.C.Y. (2005). “Use of work structuring to increase performance of project-based production systems.” Ph.D. Dissertation, University of California, Berkeley.
2. Liker, J.K. and Meier, D. (2006). The Toyota Way Fieldbook: A Practical Guide for Implementing Toyota’s 4Ps. New York: McGraw-Hill.