¿Cómo desarrollamos nuestra capacidad para identificar el desperdicio, determinar sus causas y aplicar una corrección duradera?
Esta tercera entrega de una serie de tres posts ofrece varios ejemplos pictóricos de los "Muda, Mura y Muri", como se explicó en el post nº 2. Nuestro primer post se centró en los conceptos de "desperdicio", "valor" y "búsqueda de la perfección". En este post se sugiere una plantilla sencilla para utilizarla cuando se dé un "waste walk” (paseo para detectar los desperdicios) en el lugar de trabajo y se analiza el proceso de "Análisis de la causa raíz", es decir, la identificación de lo que debe cambiarse para eliminar el desperdicio o despilfarros a nivel causal.
Primero, hagamos una recapitulación de algunos puntos vistos en el 1r y 2º artículo publicado.
Para identificar los desperdicios en nuestras operaciones, necesitamos ver lo que estamos mirando de forma diferente utilizando un nuevo conjunto de lentes Lean. Esta nueva perspectiva es el resultado de la aplicación de los cinco fundamentos Lean que ya debería haber memorizado: Identificar el Valor añadido definido por el cliente, creado por Flujo Continuo de trabajo que debe ser Fluido y proveniente de una demanda “Pull” (tirar de la demanda en vez de empujar) y sujeto a la Mejora Continua.
En el 2º artículo, explicamos las clásicas definiciones japonesas sobre el desperdicio que le llaman “Muda” (los 8 desperdicios), “Mura” (desequilibrios), “Muri” (sobrecarga), cada uno con el análisis de qué debería ver en relación el diseño y la ingeniería durante la fase de proyecto o durante la fase de construcción.
La identificación y el análisis sistemáticos de las prácticas de los desperdicios han sido esenciales para el desarrollo de los principios de Lean y de la Ciencia de las Operaciones. A medida que descubrimos las causas de la imperfección, empezamos a ver patrones en el diseño de nuestros sistemas de trabajo que conducen al fracaso o al éxito. Podemos convertir esos patrones observados en principios rectores y leyes científicas de causa y efecto. Si estos principios rectores son buenos, necesariamente pondrán en tela de juicio los supuestos y las formas de pensar que condujeron a los fracasos anteriores.
Un gurú del management, Peter Drucker, dijo:
“No hay nada más inútil que hacer eficientemente aquello que no debe ser hecho”
Si no extrae nada más de este tercer artículo, por favor, absorba esta verdad fundamental:
El fracaso o el éxito de cada proyecto se debe a las decisiones que tomamos, en cada momento, día a día. Las personas toman las mejores decisiones que saben, a menudo de forma inconsciente y habitualmente, basándose en sus modelos mentales subyacentes de la "realidad". Por lo tanto, el análisis de la causa raíz, si se realiza de manera meticulosa, siempre nos llevará a examinar nuestros modelos mentales subyacentes, es decir, las razones de las elecciones que hacemos. La mejora duradera requiere que aprendamos y mejoremos nuestra forma de entender el mundo y los sistemas que nos rodean y su funcionamiento.
Los Fundamentos Lean proporcionan un nuevo conjunto de lentes a través del cual ver y analizar nuestros sistemas de trabajo. Puede ejercitar sus “gagas” Lean dando un “waste walk” o "paseo para la identificación de residuos" por su lugar de trabajo. Los japoneses llaman a esto ir al "gemba" del lugar de trabajo. Aquí tiene una plantilla sencilla que puede hacer y modificar para su uso:
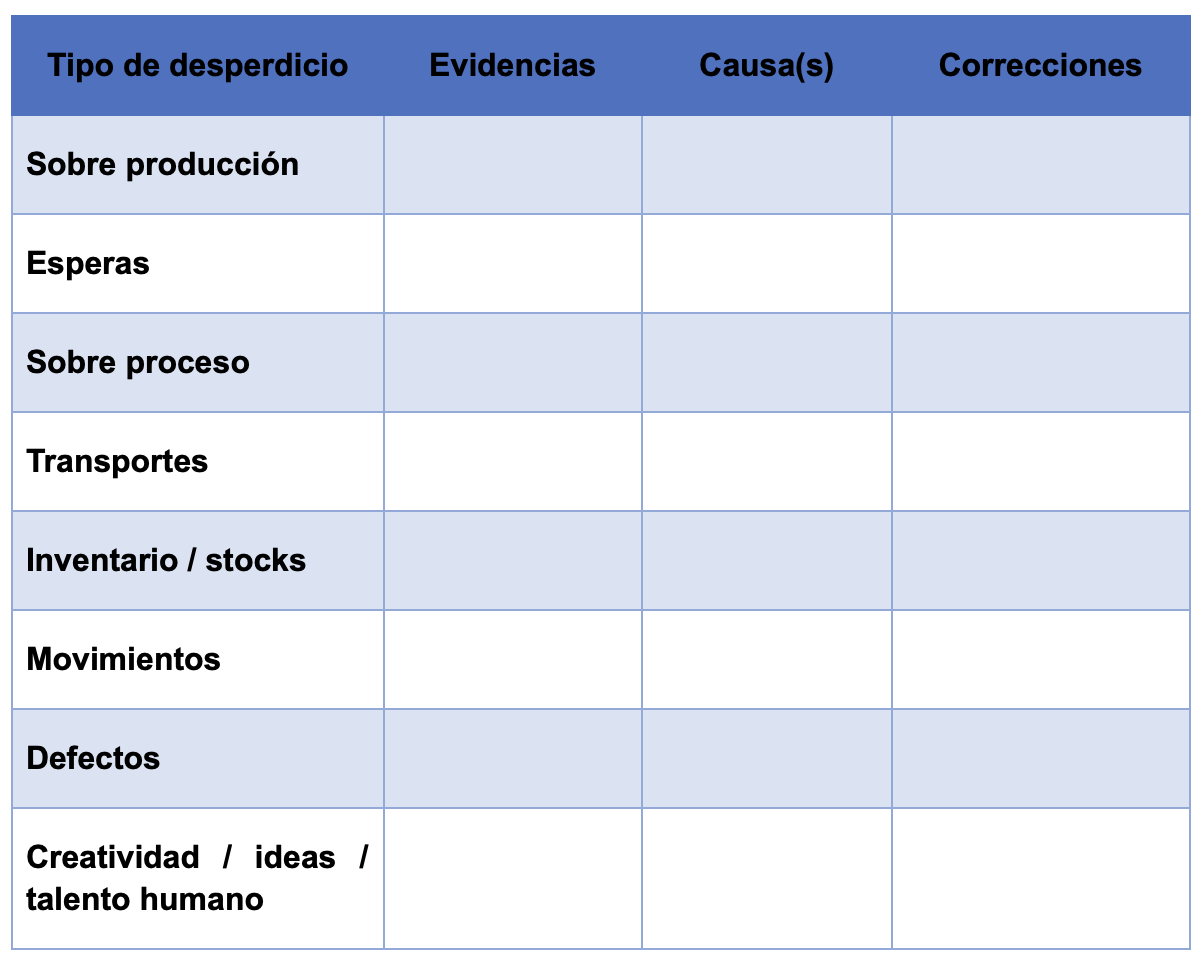
Utiliza una de estas plantillas para cada situación que encuentres: haz una foto y adjunta la plantilla. Las "pruebas" de la foto suelen sugerir una o varias categorías de residuos. Hay que investigar las causas. No basta con preguntarse "¿Quién ha metido la pata o error?". Casi siempre, la situación fue el resultado de múltiples individuos que hicieron todo lo posible por hacer lo correcto, teniendo en cuenta cómo entienden lo que es "lo correcto". W. Edwards Deming, uno de los padres de la gestión de la calidad total, nos recuerda: "Todo sistema o proceso de trabajo tiene límites inherentes en cuanto a la capacidad de producir un producto de calidad. Nadie puede superar los límites del sistema o proceso en el que trabaja". Por lo tanto, debemos aplicar el Fundamento Lean nº 2 para comprender el flujo de actividad que ha conducido a la situación.
A veces, los fallos de nuestros sistemas de trabajo son evidentes, independientemente de nuestros modelos metálicos subyacentes. Por ejemplo...
Aquí tenemos un tanque, una bomba anclada a un pedestal formado, y un carrete de tubería prefabricado que se supone que conecta los dos. Hmm... ¿Qué hay de malo en esta imagen?
El desperdicio, que es un defecto de calidad, es obvio por la brida desalineada. Menos obvios en una imagen son otros desperdicios, como la espera. Cuando tomé esta foto, esta situación había permanecido así durante muchas semanas, sin corregir. También tenemos un WIP (Del inglés, Work in progress, trabajo en ejecución), un inventario de trabajo en proceso que no añade ningún valor en su estado actual. Habrá un retrabajo que requerirá transporte y un ("sobre") procesamiento adicional. ¿Cuál es la causa de esto?
A partir de la imagen no podemos decir si el problema de fondo es un error de diseño, de prefabricación o un error de instalación en la obra de algún tipo. Durante el análisis del problema descubrimos que el pedestal del tanque y el tanque se instalaron primero correctamente y que las dimensiones originales del diseño de cada elemento en general estaban bien. Por casualidad, a medida que se avanzaba en esta zona de trabajo, la actividad de inspección adicional del emplazamiento descubrió que se había colocado un marcador de inspección crítico en un lugar muy transitado y desprotegido. La maquinaria pesada había pasado por encima y se había desplazado unos 25 cm. El pedestal de la bomba y los demás elementos se colocaron utilizando el marcador desplazado. El carrete de acero inoxidable se prefabricó fuera de la obra sin medir la ubicación real, probablemente porque era un elemento más largo y costoso.
Si seguimos la lógica de Deming, debemos examinar cómo se ha configurado todo el sistema y las suposiciones subyacentes sobre cómo debe hacerse el trabajo. En este proyecto había una serie de empresas subcontratadas, cada una de las cuales trabajaba con sus respectivos contratos de baja cuantía con márgenes muy estrechos. Cada uno era responsable de su propia pieza del rompecabezas, sin ningún incentivo para colaborar, lo que presumiblemente consumiría tiempo no incluido en sus ofertas. Se les pagaba mediante el EVA (del inglés, Earned Value Analysis, Análisis del Valor Ganado o acordado), lo que creaba un incentivo para construir y facturar el mayor "porcentaje de finalización" reclamable lo antes posible. Los subcontratistas podían afirmar que cada uno de ellos había funcionado perfectamente, que habían consumido su capacidad disponible y que necesitarían una orden de cambio aprobada para hacer correcciones. El sistema de producción funcionaba perfectamente como se había diseñado. Se diseñó partiendo de la base de que, si cada gremio hace su trabajo a la perfección y al menor coste posible, todo irá bien. Esta organización tradicional de los proyectos conduce a lo que Lean llama "Optimización del subsistema, mientras se sub-optimiza todo el sistema".
La acción correctiva más sencilla, modificar la bobina de la tubería para que encaje, sigue requiriendo un retrabajo despilfarrador y probablemente más despilfarro de sobreprocesamiento y espera, ya que las partes interesadas se pelean por quién pagará las correcciones. La solución del problema inmediato podría haber sido realizada en un día por un instalador de tuberías cualificado. Muchas acciones correctivas se detendrán ahí, habiendo apenas arañado la superficie de las condiciones que condujeron a la situación. La única manera de llegar a la causa raíz es sustituir un sistema que desalienta la colaboración y la responsabilidad compartida, premia la actuación en interés propio, aunque sea con las mejores intenciones, y está limitado por la desalineación contractual. Repensar el sistema de producción de proyectos no es una tarea sencilla, una comprensión que probablemente impulsa gran parte de la resistencia a las prácticas Lean a la que tan a menudo nos enfrentamos.
Una herramienta eficaz, pero a menudo incomprendida para el análisis de la causa raíz es "Los cinco porqués". Este enfoque se desarrolló en la línea de montaje de una fábrica. Cuando se detectaba un error en cualquier estación de montaje de la línea, como una pieza que no encajaba correctamente, la práctica consistía en detener la línea y trabajar hacia atrás en la línea, preguntando cada vez "¿Por qué?" ocurrió el error. No había magia en "Cinco" porqués. Se trataba de seguir indagando en el proceso hasta encontrar una causa corregible y aplicar una solución para evitar esos errores en el futuro. Retroceder en la línea, en el flujo de trabajo o en el tiempo también se llama a veces "análisis de regresión". En la situación anterior, tuvimos que hacer un análisis de cada uno de los elementos y oficios. Algunos elementos sólo requerían un único "¿por qué?" para validar su correcta instalación. Otros elementos requerían comprender la secuencia del flujo de trabajo en la obra, creando mental y visualmente el equivalente de la cadena de montaje de una fábrica, para identificar dónde se producían las averías. Los "5 porqués" podían aplicarse a cualquier avería.
Algunos casos son más fáciles de analizar con una simple serie de "porqués". Es difícil encontrar un ejemplo más lineal que el de una tubería -¿O dos, o tres? He aquí otro ejemplo con un par de fotos.
Esta situación tiene lugar en una explotación petrolífera bien desarrollada y saturado. El petróleo y el gas están contenidos en formaciones rocosas porosas a cientos de metros de profundidad. Se bombean productos químicos de fracturación (fracking) y vapor a alta presión en la roca para provocar la fracturación por expansión y desprendimiento del petróleo mediante calor y productos químicos para facilitar la extracción. Los líquidos extraídos se depositan en grandes tanques y el agua y otros materiales se desvían para su limpieza y reutilización. Este proyecto consiste en instalar un nuevo conjunto de tuberías de acero inoxidable, que se configurarán como las tuberías oxidadas del primer plano. Obsérvese la diferencia de diámetro en el primer plano. Está claro que tiene sentido instalar los carretes de mayor diámetro primero y más atrás para facilitar el acceso a cada tubería de diámetro sucesivamente pequeño y evitar tener que levantar carretes pesados sobre carretes más pequeños y más fáciles de dañar. Las tuberías de este tipo sólo pueden extenderse hasta cierto punto antes de que sea necesario un bucle de expansión en forma de U, visible en la tubería de acero inoxidable en línea con los depósitos distantes. Obsérvese que las bobinas de acero inoxidable se colocan a lo lejos sobre los soportes amarillos de las tuberías, antes del equipo de soldadura. Sencillo. ¿Qué podría salir mal?
Esta es la escena detallada a continuación. ¿Qué señales de qué tipo de despilfarro ve en el sistema de producción? ¿Cómo resolverías el problema para encontrar y solucionar la causa raíz?
De nuevo, la situación que se presenta es obvia, aparentemente. Hay cuatro diámetros de tubería en el sistema, incluyendo la más grande de color óxido y las tres sucesivamente más pequeñas de acero inoxidable. Al menos dos carretes, prefabricados con codos de 90 grados soldados se dejaron fuera de la construcción de este bucle de expansión y, al parecer, hace tanto tiempo que las dos líneas más pequeñas ya se hayan instalado, bloqueando el acceso a la tercera línea más grande. El equipo de soldadores está trabajando en otras bobinas más delante de la línea más externa y pequeña. Esto no parece ser un caso único. Nuestro bonito y lógico plan de instalación se ha venido abajo de alguna manera. Necesitamos un análisis.
Entre los indicios identificables de despilfarro están
- Defectos/errores – Esta vez no en los materiales, sino en el proceso de suministro de materiales
- Desplazamiento – las cuadrillas, los materiales, los equipos de soldadura, las grúas, etc., se mueven de un lado a otro a lo largo de muchos kilómetros de tuberías. Las cuadrillas y los equipos de soldadura deben ser levantados en espacios ahora confinados, arriesgando la seguridad y la calidad. El hecho de que las cuadrillas se desplacen por todas partes, arrastrándose por encima y por debajo de las tuberías, es también un ejemplo de “Muri” (de su término en japonés, sobrecarga).
- Procesamiento excesivo o insuficiente – las bobinas que se dejan en el desierto se llenan de polvo y otros residuos y las reparaciones sobre el terreno, especialmente de bobinas revestidas de cemento, que se pueden secar y agrietar si no se mantienen húmedas, son habituales.
- Inventario – en forma de WIP (del inglés, “Work In Progres” o trabajo en ejecución), lo tenemos aquí, ¿Y en cuántos otros lugares?
- Espera y creatividad de los empleados – aquí vemos una solución creativa al problema de la capacidad de los tiempos de espera en el trabajo. Las bobinas se instalan fuera de secuencia para optimizar la capacidad disponible, pero sin optimizar el sistema global de producción. Finalmente, los carretes se entregan fuera de secuencia y ahora tenemos trabajo esperando la disponibilidad de las cuadrillas. Un gran ejemplo de “Mura” (de su término en japonés, desigualdad de flujo).
En esta situación, el análisis de la causa raíz de los "5 porqués" es más lineal:
- ¿Por qué se instalaron carretes de tuberías fuera de secuencia? Porque faltaban algunas bobinas y había bobinas de otros diámetros a disposición de la cuadrilla que necesitaba hacer el trabajo.
- ¿Por qué faltaban algunas bobinas y había otras disponibles? La disponibilidad del material dependía de los lotes de entrega y de la coordinación con la fabricación de carretes de tuberías.
- ¿Por qué los lotes de entrega mezclaban y combinaban estos diferentes tamaños de carretes? Porque la oficina de logística de fabricación se encargó de utilizar la máxima capacidad de los remolques de transporte para reducir los costes. Se trata de una práctica habitual para el éxito del subsistema de logística.
- ¿Por qué se fabricaban y entregaban las bobinas fuera de secuencia? Porque se licitó todo este trabajo de manera global para permitir al taller de fabricación optimizar la capacidad entre las numerosas demandas de los clientes que competían entre sí.
- ¿Por qué el campo y el taller de fabricación, ambas divisiones de la misma empresa, no coordinaron mejor la demanda (“pull” o flujo tirado) y el suministro? Porque el trabajo de instalación sobre el terreno y el trabajo de fabricación estaban organizados como divisiones corporativas separadas, cada una de las cuales se encargaba de mantener su capacidad plenamente utilizada y era evaluada por ello, sin tener en cuenta el efecto sobre el rendimiento del proyecto en su conjunto.
No había un sistema fiable para equilibrar y predecir la oferta y la demanda. El superintendente de campo dijo que la dirección de su empresa desaprobaba cualquier demanda de campo que pudiera "interferir" con las decisiones de utilización de la capacidad en las instalaciones de fabricación. Fin de la discusión. El cliente acaba pagando, ya fuera en órdenes de cambio, en retrasos y falta de fiabilidad en la finalización del proyecto, ya que cada día de retraso le impide generar ingresos con las nuevas líneas y la nueva planta de limpieza de agua a la que alimentan las líneas.
El efecto sobre el inventario de materiales puede verse aquí:
El modelo mental operativo subyacente para la gestión de proyectos es esencialmente "divide y vencerás" en lugar de "colabora y coordina". Las bobinas entregadas fuera de secuencia en un lote común de materiales se mueven y reubican varias veces, con el riesgo de entregar la bobina equivocada en el lugar equivocado y de tener que repetir el trabajo. La fabricación puede presumir de haber fabricado el 80% de las bobinas, pero ¿equivale eso al 80% de la instalación que puede completarse?
Como no estamos acostumbrados a diseñar los proyectos de construcción como sistemas de producción, con un flujo de principio a fin y con tasas de rendimiento medibles, no vemos las consecuencias de nuestras decisiones a nivel de subsistema en el éxito general del proyecto. Para suavizar el flujo de producción, nuestro sector debe desplegar más herramientas automatizadas de gestión de la producción que conecten la fabricación, la entrega y la instalación en tiempo real para establecer un flujo fiable de recursos basado en la preparación del terreno tirando de toda la cadena de suministro.
Por último, he aquí un par de ejemplos de situaciones no lineales:
¿Qué ves en estas fotos? El desorden es evidente. Hay un exceso de inventario, trabajo en curso y todo tipo de riesgos de seguridad que invitan al peor tipo de "errores": las lesiones. Una vez más, el modelo subyacente es mantener los recursos trabajando en la instalación, no en la limpieza, pero el proceso de instalación está claramente tan desorganizado que uno debe dudar de que se esté logrando alguna "eficiencia". Estos ejemplos exigen a gritos una solución de "5 S".
Como se ha comentado en el post 2, cuando se ejecuta correctamente una solución Last Planner®, el sistema de producción crea un Look-Ahead de varias semanas con planes de finalización de trabajos inmediatos cada vez más detallados. El Análisis de restricciones permite la identificación temprana de materiales faltantes o incorrectos y otros errores. El objetivo es completar el 100% del trabajo que debe realizarse cada día según lo comprometido. Sólo un 85-90% de la capacidad debe comprometerse con las tareas planificadas, dejando un pequeño colchón que limpie y organice, elimine las próximas limitaciones y resuelva los problemas. Los ejemplos anteriores evidencian un fallo en el diseño y la gestión del sistema de producción.
El exceso de capacidad aplicado a las "5 S" (clasificar, simplificar, limpiar, estandarizar y mantener) puede crear resultados en el lugar de trabajo como estos:
Si las herramientas, los materiales e incluso los espacios de oficina están organizados así y a disposición de las áreas de trabajo, ¿Cuánto más eficiente será el trabajo, en comparación con los ejemplos de obras más desordenadas?
Como dije en el primer post de esta serie, cuando aprendemos a reconocer los residuos en el sistema actual podemos encontrar oportunidades casi ilimitadas de mejora, algo que añade sentido y emoción a cualquier trabajo. Ese entusiasmo proporciona la energía que necesitamos para superar la inercia de la costumbre y la enormidad de la necesidad de repensar la forma de hacer negocios. La clave para añadir valor y reducir el despilfarro es examinar las decisiones que tomamos, tanto las grandes como las pequeñas, y tomar decisiones mejor informadas basadas en una comprensión más ilustrada e informada de los sistemas de trabajo.
Ahora el reto es suyo. ¿Cómo podemos diseñar y poner en práctica sistemas de producción cada vez mejores y más fluidos que produzcan valor sin desperdicio exactamente cuando y donde se necesita?
Reúna a sus equipos. Realice paseos por los residuos con regularidad. Fotografíe y documente lo que encuentre. Analicen las causas y solucionen los problemas en colaboración, y luego... presenten sus conclusiones y mejoras en el chat de abajo.
Mantengamos el debate y el aprendizaje en beneficio de todos.