A previous blog article discussed Lean Construction Management (LCM®) as an alternative process model to the Last Planner System, as well as Takt planning and Takt control. This article looks at the implementation of Kanban card systems and Andon signals in greater detail.
Today’s construction projects are highly complex. And visualization can help. This is because the human brain processes visual information faster than the written or spoken. Despite this, visualization and the associated high level of transparency of processes is seldom found on today’s construction sites. This has given rise to LCM®. LCM® makes use of visual planning. It adapts the Kanban systems used in Lean Management from automotive production to the execution phase of construction projects. This allows the construction execution process to be timed right down to the smallest detail and to the day, and then to be flexibly controlled on the construction site. LCM® promotes project visualization and collaboration between all stakeholders with regard to the construction process and the sequence of individual work packages. While downtime is not uncommon on many construction sites, it would be unthinkable in the manufacturing industry, where processes are already so finely tuned that every second is meticulously filled and every move is perfect.
On construction sites, however, there is often sheer chaos! This could be avoided with simple means such as better planning depth before the start of construction and the use of a Kanban card system as an on-site planning and control tool. Like in any production facility, detail or board planning with the help of Kanban cards serves as an important visual control tool both for the trade contractors and construction management. The construction sequence for the next four weeks is displayed on the board in advance and planned down to the day. As a simple physical tool, it allows all project participants to discuss detailed planning on site and plan construction work three to four weeks in advance. The individual activities, key figures and action items can be read off the four-week board.
Each trade has its own card color or hatching. The daily activity of each trade is noted on the cards. Everyone can see exactly what the trade is currently doing where. Each card represents a goal for the day for the trade concerned. Any disruptions to the construction process are identified at an early stage. In this respect, the LCM® system always acts as an early warning system. This is illustrated in Figure 1.
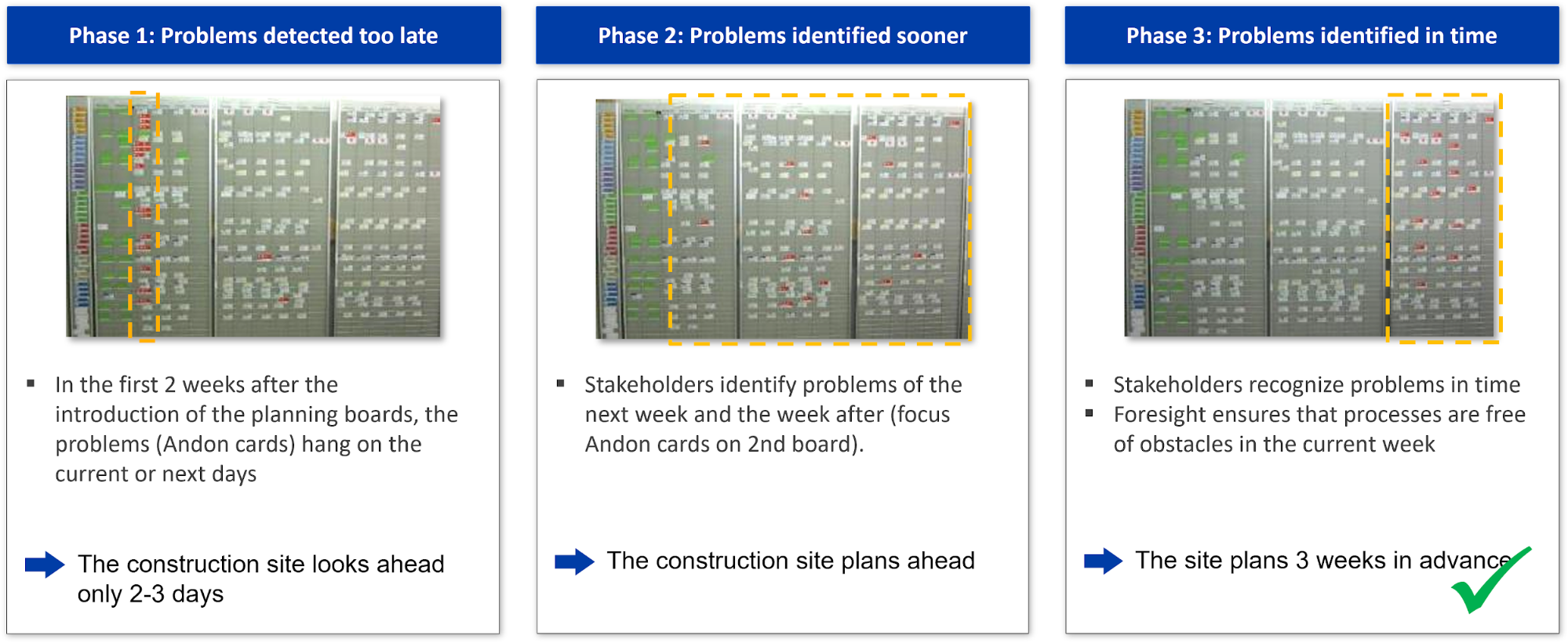
Figure 1 is an example of a three-week preview. Initially, when the board has been completely filled, the team identifies a number of problems, all of which occur on the same day or within a week. The time is too short for a systematic solution or workaround, resulting in greater process instability and a lot of ‘firefighting’. About one to two weeks after the board has been installed, the site team is able to spread problems out across the board so that they are not all being addressed at once. After four to six weeks, most problems are listed on the board in the final week, and three to four weeks is usually enough time at this detailed level to resolve the problems.
Once a week, a meeting is held at the detailed planning board to discuss the work for the next three weeks and to plan for the fourth week (see Figure 2). Each contractor fills out their cards for the fourth week before the meeting. Each card represents one unit of work per day per team. Together, the fourth week is then planned on the board (cards are put in their respective work areas on the drawing, tasks are defined, and any problems identified). Kanban cards show all the information for a daily work package per team/trade, and as mentioned, each team or trade has its own color or hatching.
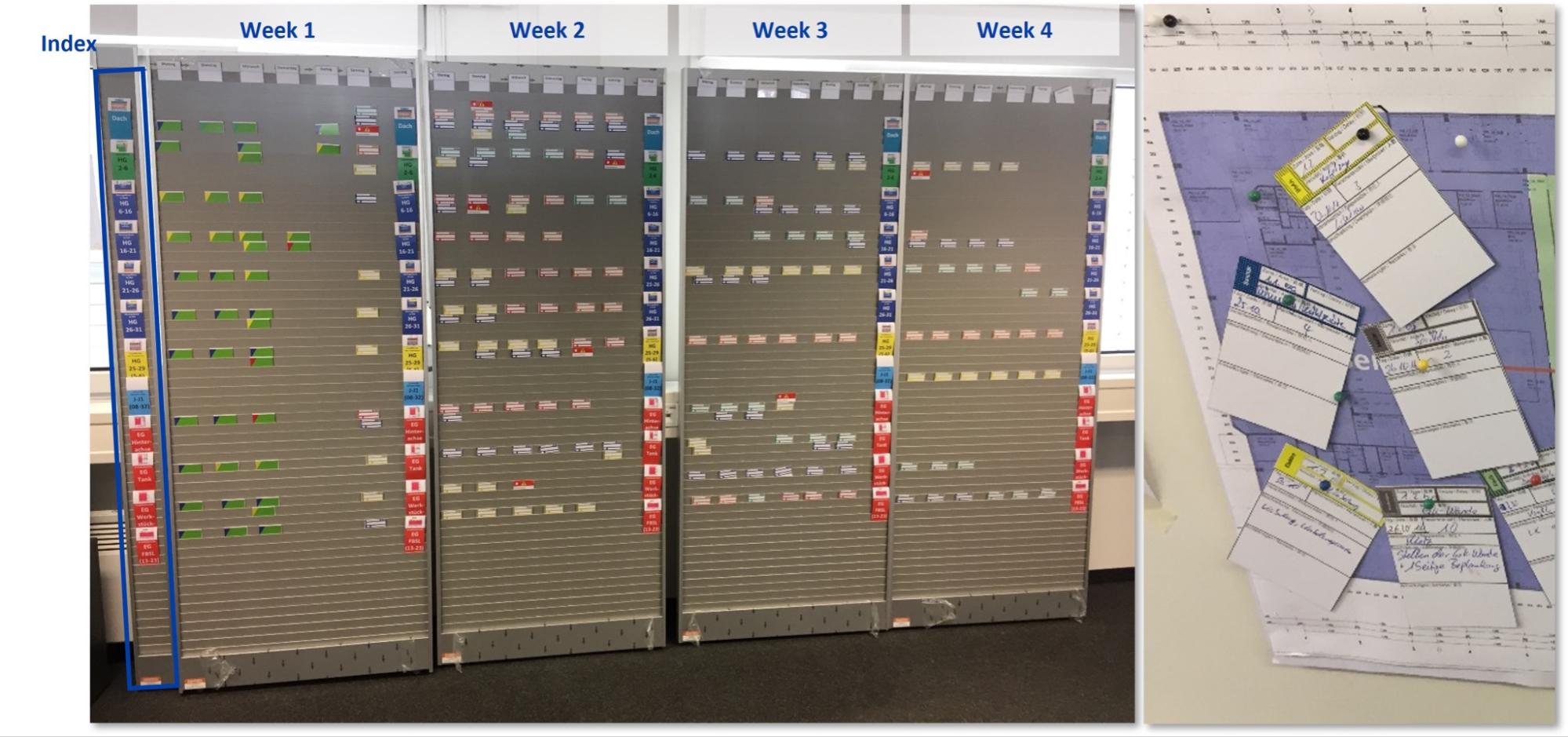
In addition to the construction cards for each trade, there are other types of cards (see Figure 3):
- Work Area Cards: These are placed in the left column of the Kanban board and show the work areas of the project. The left column is also called the Index Board.
- Problem Cards: These are red and visualize a time constraint in the process. It is placed in front of the card that the problem concerns. The problem card adapts the Andon ‘lamp’ principle from Lean production to the construction site.
- Stop Card: A Stop card is inserted to indicate that there will be no activity in a specific area for a certain time (for example, allowing screed to cure until it is ready to be driven on). It means that the work area must not be entered or that work must be stopped in that work area.
- End Card: The End card is placed after the last current task performed in this work area.
- Planned End Card: The Planned end card shows the first planning goal of a planning area. The End Card can be placed before or after the Planned End Card.
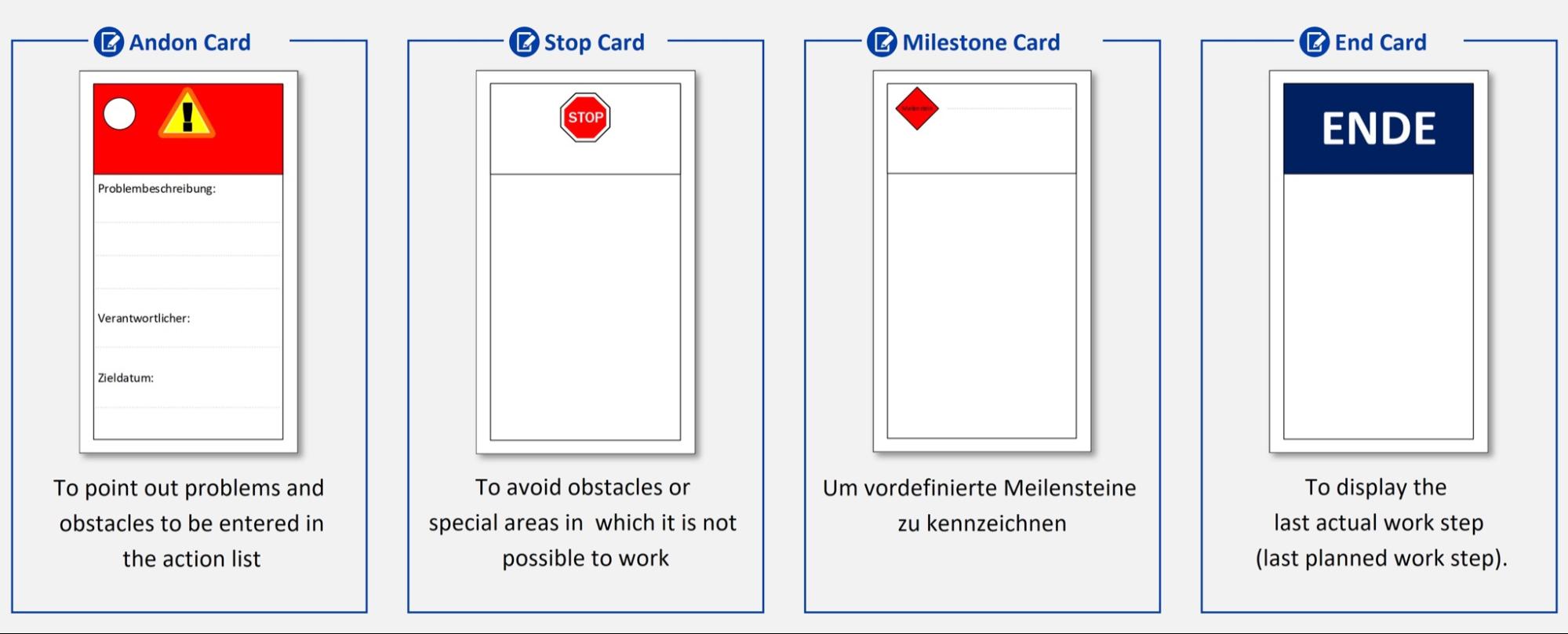
The Percent Plan Complete (PPC) is calculated by dividing the number of completed cards (turned to show the green back) by the total number of plan cards per trade/team per day. PPC is one of the key performance indicators of the LCM® system. It does not show the conventional contractor schedule variances, but instead documents daily process stability. At defined cyclical intervals, all participants meet in the designated Lean Room. The LCM® makes processes on the construction site stable and reliable – 80% to 95% of the time. Stability is a guarantee that construction projects will be completed on time and within budget, and will ultimately deliver the quality demanded by the client.