Contact Information
info@leanconstructionblog.com
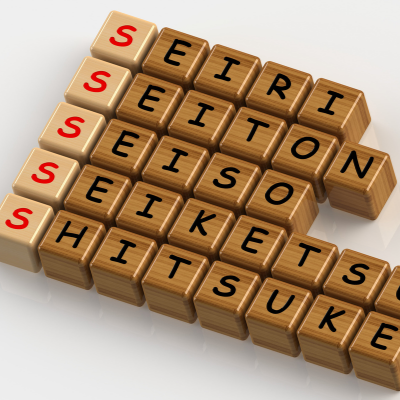
Keys and Tips to Implement the 5S Methodology
The 5S methodology was born at Toyota in the 60s under an industrial environment to achieve better organized, tidier, and cleaner workplaces to increase productivity and to obtain a better working environment.
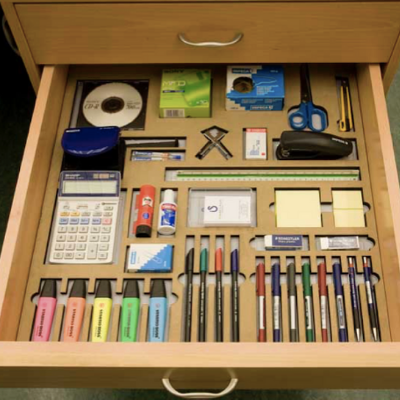
6 Tips On How To Implement A Lean Office in the AEC Industry
A highly revered ex-Toyota consultant stated that most manufacturers seem focused on achieving a 35 to 40 percent productivity gain over three to five years as a measure of success in their current Lean efforts.
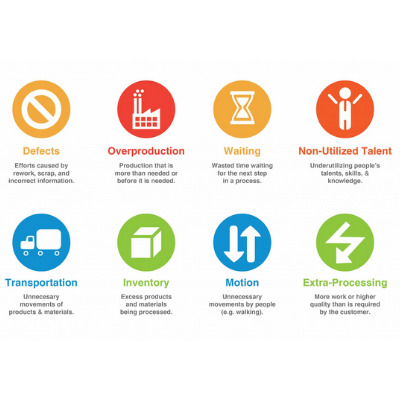
The Concept of Waste as Understood in Lean Construction
The construction industry is seen, by researchers, as a slowly progressing industry that is suffering from low productivity and poor performance compared to other industries.
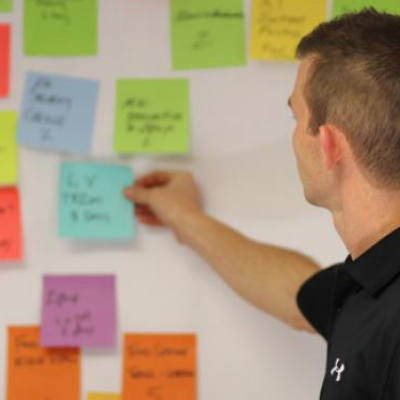
What is the Last Planner System?
It’s full name is the Last Planner® System of Production Control. Production control is necessary on projects to support working toward planned accomplishments, doing what can be done to move along a planned path, and when that becomes impossible, determine alternative paths that accomplish desired goals.
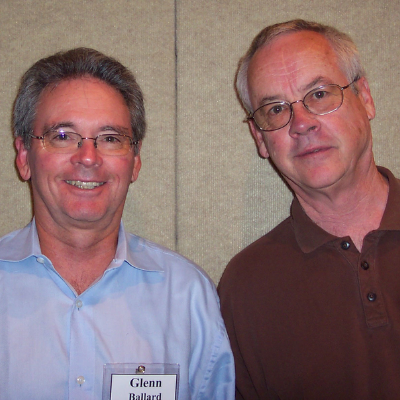
The History of the Development of the Last Planner® System
According to Glenn Ballard, one of the inventors of the Last Planner System (LPS), an earlier study on Crew Planning in the 1980s was a precursor to its development. At that time, Glenn was the Productivity Improvement Manager for Brown & Root’s Construction in the US.
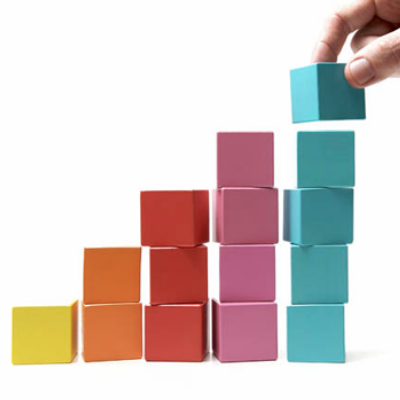
5 Levels of the Last Planner® System “Should, Can, Will, Did and Learn”
The Last Planner System (LPS) is a production planning and control system designed to produce predictable workflow and rapid learning in programming, design, construction and commissioning of projects. LPS has five main elements.
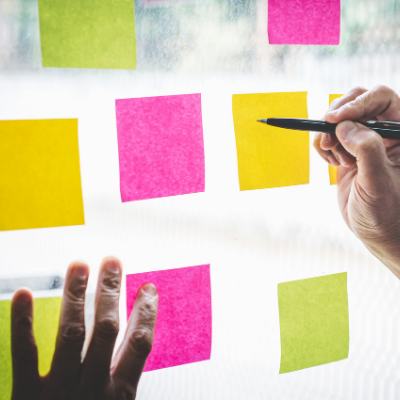
How to Lead a Pull Plan Session
Around 15% of builders are using Pull Planning (although only 9% are using the full Last Planner® System) on at least some of their projects, according to the AGC and McGraw Hill [1] . The challenge is how to get the most value in the shortest time during a pull planning session.
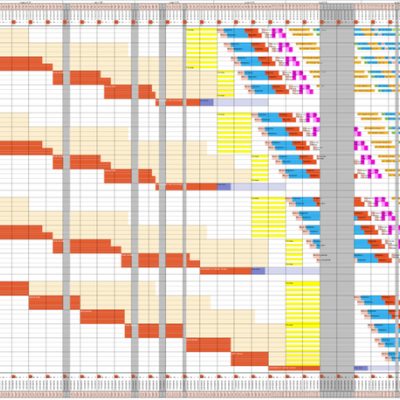
Location Based Management System & Takt Time Development for Construction Sites in France
Lean Construction has been developing in France since the 2010s, mainly under the impetus of specialized consultants for the largest general contractors.
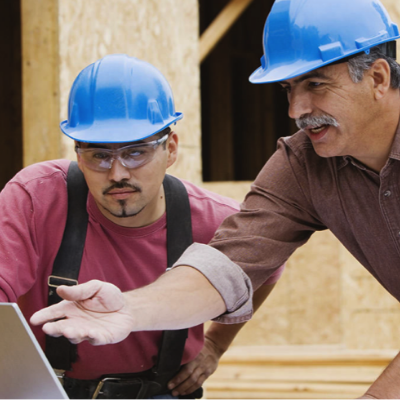
An Introduction to Takt Time Planning
‘Takt time’ is a term used in manufacturing to describe pacing work to match the customer’s demand rate. ‘Work structuring’ is the practice of scheduling out work and is a part of designing a production system. Takt time planning then, is one method for work structuring around a set pace of work.
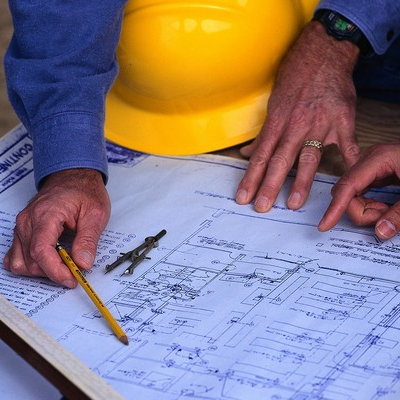
5 Steps To Takt Time Planning
As a foreword to the post, I think there are many ways one can execute Takt time planning (TTP). The fact that there isn’t much research on the topic in construction means that it is definitely an open question. Through some iteration and research, the five step method below is the best practice to Takt time planning so far.
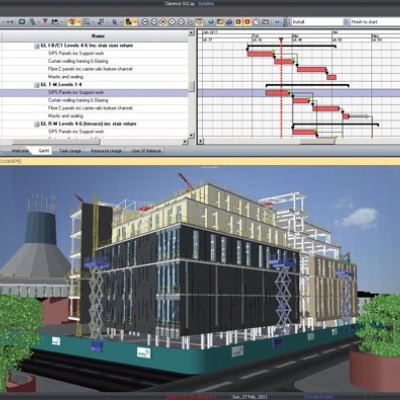
How 4D scheduling creates synergies between BIM and Lean
With new tools come new methods. There are numerous examples of this when it comes to Lean Construction and BIM, where new BIM tools require new processes that very often encompass several lean principles.
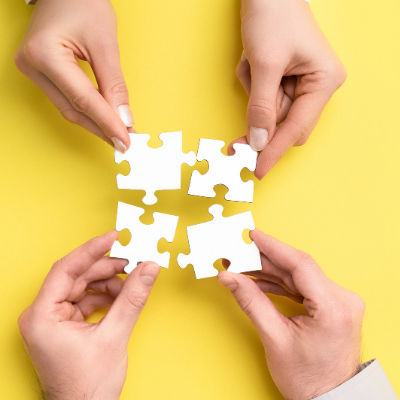
Top Ten Synergies between Lean Construction and BIM
Lean Construction and Building Information Modelling (BIM) are important transformation drivers for the construction industry. Recent research shows that there are considerable synergies between the two.
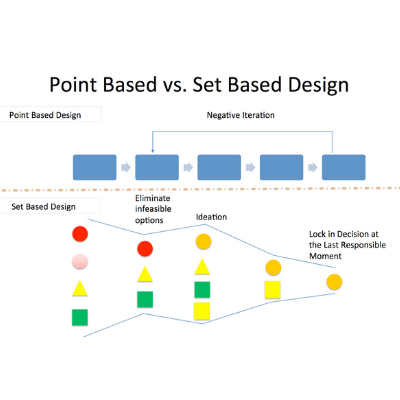
An Introduction to Set Based Design
Set-based Design (SBD) is a design methodology that has many applications in the architecture, engineering, and construction (AEC) industry. It was discovered when researcher studied the engineering and design process at Toyota [1]. Known as the “second Toyota paradox”.
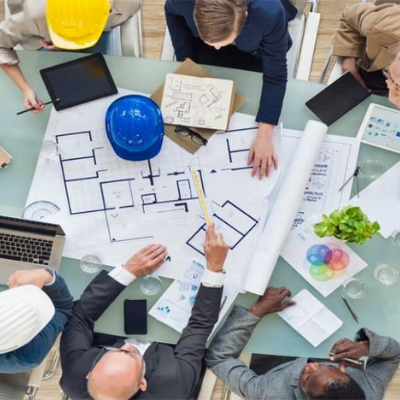
Lean Tools During Design & Preconstruction – IPD or Not
I wanted to start this blog post with the most important message I have for all those who read this – you don’t need to have an IPD project in order to successfully use lean tools during design and preconstruction!
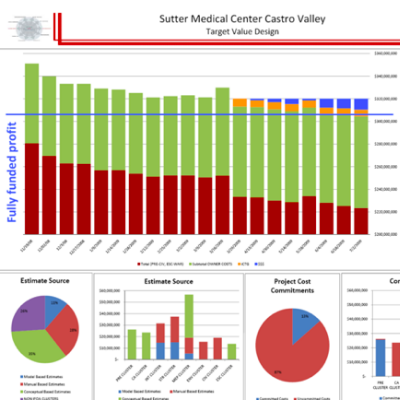
An Introduction to Target Value Delivery
Target Value Delivery (TVD) is “a management practice that drives the design [and construction] to deliver customer values within project constraints” (Ballard, 2009). It is an application of Taiichi Ohno’s practice of self-imposing necessity as a means for continuous improvement (Ballard, 2009).
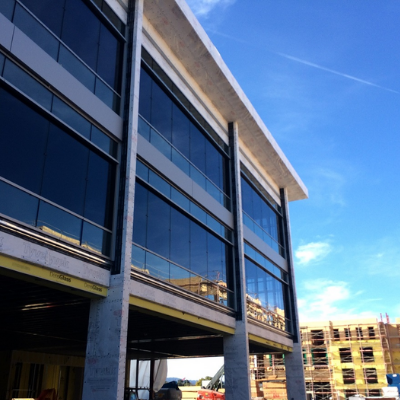
5 Things to Consider When Setting Targets For Target Value Delivery
A common concept in the construction industry is that there are three legs to a project: Schedule, Cost, and Quality. An owner is advised to pick any two, and thereby sacrifice the third (i.e., you can have cost and schedule, but not the quality you want.
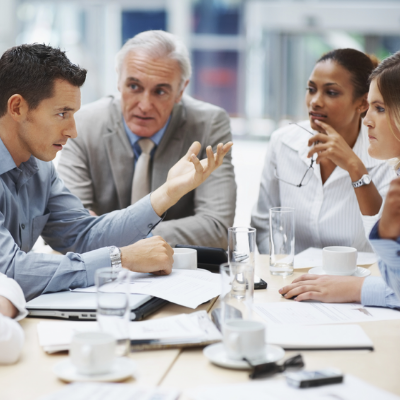
Step By Step Guide to Applying Choosing By Advantages
Choosing by Advantages (CBA) is a collaborative and transparent decision making system developed by Jim Suhr, which comprises of multiple methods. CBA includes methods for virtually all types of decisions, from very simple to very complex (Suhr 1999).
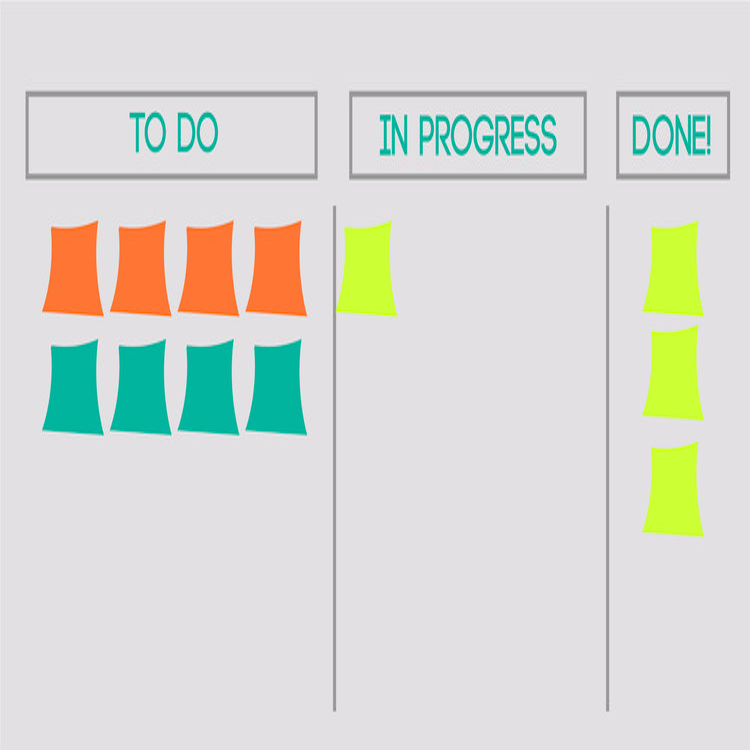
11 Scrum Steps to Get Twice the Work Done in Half the Time
Before I began my Lean journey in 2009, I honestly never thought about my capacity. I paused and reflected on what I had learned about applying Lean. My entry point was “Lean Thinking” by Womack and Jones.
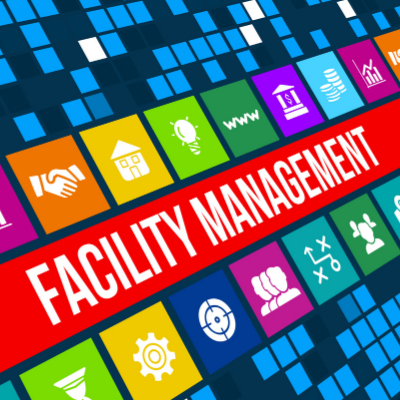
Lean Facility Management – Introducing the Kanban System
Maintenance is defined as a combination of technical, administrative, and management activities throughout the product lifecycle [1]. This is done to ensure that the product keeps functioning smoothly and achieves its full lifecycle.
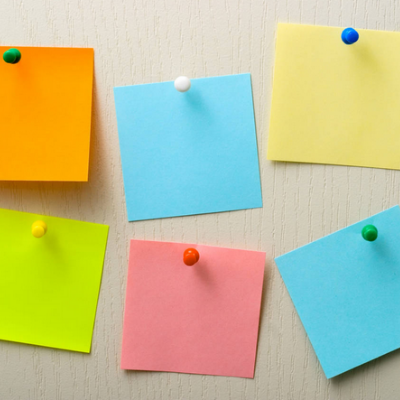
An Introduction to Conventional Visual Management
Visual Management is a visual (sensory) communication strategy that is frequently used to realize Lean Construction goals at the operational level (i.e construction field, design office, facilities etc.). Visual Management emphasizes consciously employing simple yet effective cognitive concepts and artefacts.
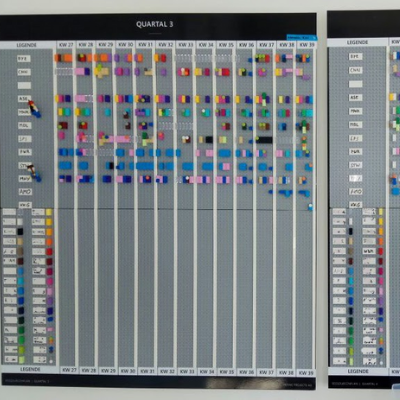
How Visualizing Your Resources Can Lead to Better Flow and More Reliable Commitments
In an office, organizing the available resources and securing reliable commitments in the daily business is important.
+Into+Action.png)
A Simple Framework for Putting Integrated Project Delivery (IPD) Into Action
Design and construction projects are long and complex and require collaboration between many parties. While there are benchmarks in place to help owners achieve efficiencies, the traditional delivery model leaves much to be desired.What if we could do better?
_+-+Part+1+of+3.png)
What is Integrated Project Delivery (IPD)? - Part 1 of 3
Integrated Project Delivery (IPD) is gaining popularity among owners, contractors, and design teams as a means to unlock creativity, drive reliability, and successfully deliver complex capital projects.
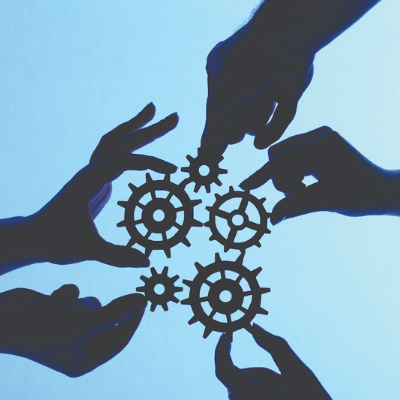
What is Integrated Project Delivery Part 2: Lean Operating System
This post is the 2nd of a 3 part series looking at Integrated Project Delivery. The first post focuses on IPD agreements (contracts), this post focuses on IPD as a Lean Operating System, and the final post focuses on culture.
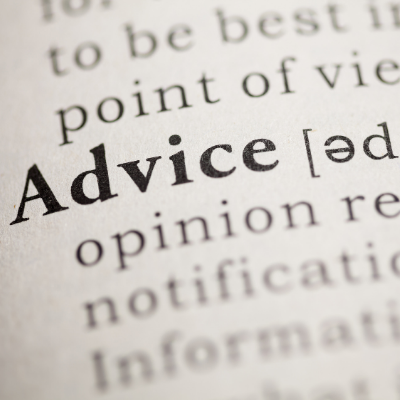
IPD Advice from Owners
During the Summer of 2013, we interviewed a group of owners who had completed IPD projects. Some owners had many IPD projects under their belts and others only one or two. But all were willing to share their experience and advice to help other owners.
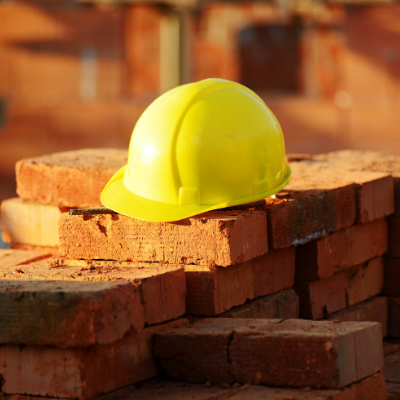
Lean Construction Won’t Happen and Here’s Why
The concepts of lean have been applied to the design and construction of capital facilities for twenty years or more. I think it’s high time that we in the construction industry face the hard truth – lean is not going to happen in our lifetime – not really.
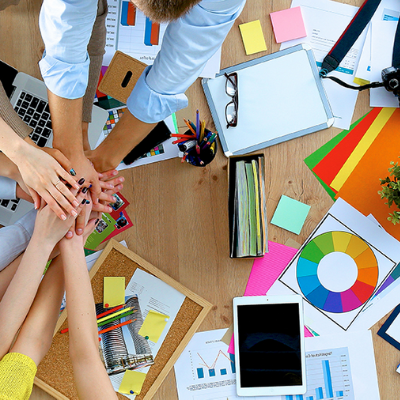
Culture Matters in Design and Construction
In the choosing, developing and managing of design and construction teams, the collaborative project delivery approach consciously seeks out teams of individuals that embrace certain core beliefs. The first core belief is that the current system is dysfunctional and doesn’t work well.
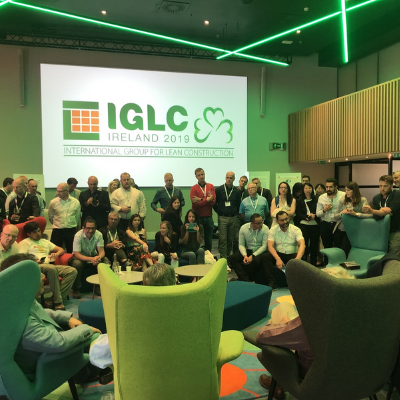
Highlighting 12 Papers from the IGLC 2019 Conference
The International Group For Lean Construction (IGLC) is an international conference started in 1993. The IGLC brings together an international community of researchers and industry practitioners each summer to advance the research and practical applications of Lean Design and Construction.
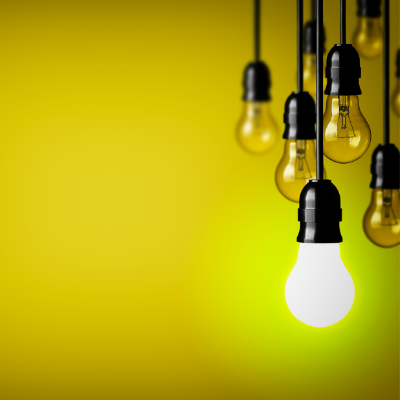
5 Key Ideas to Make Your Lean Implementation More Successful
As a trainer and consultant of Lean Construction, I have always been passionate about the human side of Lean. I have been observing the behaviour of people in a lot of companies regarding the cultural changes that comes with implementing Lean.
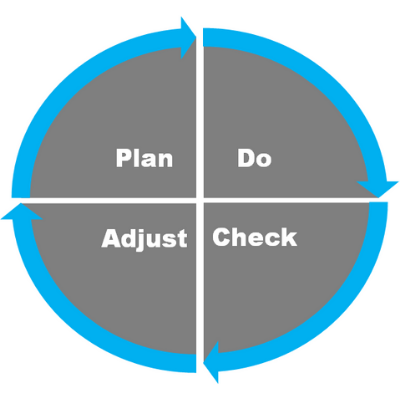
First Run Video Studies: Plan-Do-Check-Adjust
Plan-Do-Check-Adjust (PDCA) is an improvement cycle based on a scientific method of proposing a change, implementing the change, measuring the results, and adjusting as needed. It is also known as the Deming Cycle after W. Edwards Deming who introduced the concept in Japan in the 1950s1.
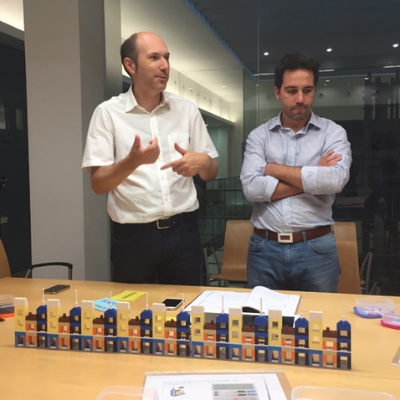
Teaching Lean Construction I: Pull & Flow
According to Tommelein et al.1, workflow can be characterized in several different ways. In manufacturing, it is defined by stationary machines with partially completed products being transported from one to the next. In construction, the products being built tend to be stationary, whereas crews of various trades move from location to location.
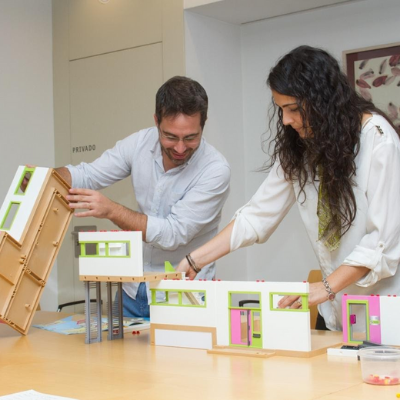
Teaching Lean Construction II: Last Planner
Glenn Ballard and Greg Howell developed the Last Planner System of Production Control throughout the 90s1. At the same time, Lauri Koskela was working on developing a theory of production which provided the theoretical framework for the LPS2.
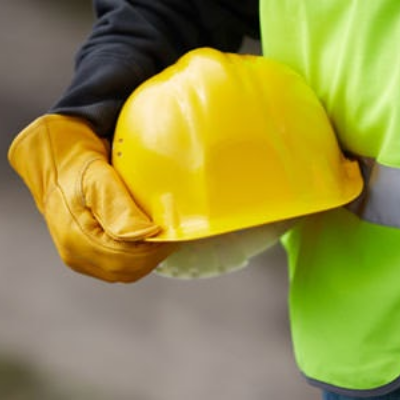
Applying Lean Thinking to Improve Safety Performance in Construction
The construction industry remains one of the most hazardous industries in the United States in terms of the number of occupational fatal and non-fatal injuries. In 2014, 874 fatal work-related injuries were reported in the U.S. construction industry.
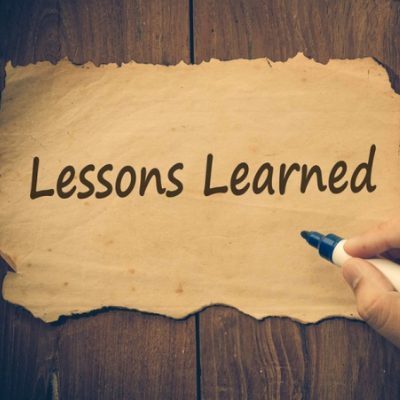
Lean Lessons Learned: 10 Steps to Success
My Lean thinking has gradually evolved since beginning my journey in 2000. You'd think I’d have figured it all out by now, right?... Not a chance. I was recently asked a very good question: What would you do differently if you had all the Lean knowledge and experience you have today?1 Below are 10 thoughts to this question.
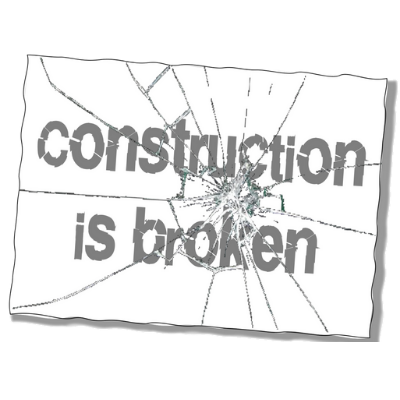
Construction is Broken
The idea that construction is broken has been long recognised by governments. Since the 1930s the UK government alone has commissioned over 15 reports aimed at trying to improve the way work works in the construction sector.