Planifier-Faire-Vérifier-Adapter (PDCA) est un cycle d'amélioration basé sur une méthode scientifique qui consiste à proposer un changement, à mettre en place le changement, à mesurer les résultats et à ajuster si nécessaire. Il est également connu sous le nom de cycle de Deming, d'après W. Edwards Deming qui a introduit le concept au Japon dans les années 1950.
Taiichi Ohno, à qui l'on doit une grande partie de la réflexion sur le système de production Toyota, était connu pour se rendre dans l'atelier et dessiner un cercle sur le sol. Il se tenait dans le cercle et observait, réfléchissait, analysait et apprenait ce qui se passait réellement. Cette étude lui permettait d'acquérir suffisamment de connaissances pour améliorer le processus. Les fondateurs du Lean Construction Institute, Glenn Ballard et Greg Howell, ont adopté une approche similaire lorsqu'ils ont abordé les "First Run Studies" dans la publication de 1997 intitulée "Implementing Lean Construction : Improving Downstream Performance". Les études préliminaires sont utilisées pour concevoir et améliorer les méthodes de travail par le biais d'observations sur le terrain. Les améliorations mises en place deviennent la nouvelle méthode de travail standard et nous répétons le processus pour permettre une amélioration continue.
Dans ce post, j'aimerais expliquer comment, chez DPR, nous utilisons le cycle PDCA et l'enregistrement vidéo pour les études de première exécution.
1. Plan
La planification consiste à choisir une activité à étudier dans le but de normaliser le travail et d'éliminer les déchets. Les étapes de ce processus sont les suivantes
Décider de l'activité à étudier (idéalement, l'activité est répétitive ou présente un risque élevé pour le projet).
Réunir les bonnes personnes (c'est-à-dire les personnes qui effectuent le travail) qui peuvent apporter une contribution ou avoir un impact.
Faire un brainstorming sur la méthode de travail la plus efficace pour l'activité sélectionnée
Planifier la sécurité, la qualité et la productivité
Affecter la main-d'œuvre, les outils, l'équipement et les ressources
Pour réaliser une première étude, nous utilisons un équipement d'enregistrement vidéo standard (figure 1).
Figure 1 : Equipement pour l'enregistrement vidéo
2. Do
Cette étape consiste à mettre le plan en œuvre. Pendant que l'activité est en cours, nous installons une caméra pour filmer l'activité. Il n'est pas nécessaire de filmer les 8 heures d'une journée de travail. Assurez-vous simplement que la vidéo capture plusieurs cycles complets de l'activité. Par exemple, pour l'étude d'une installation de cloisons sèches, nous enregistrons les activités suivantes : Planification, mesure, découpe, manutention et installation d'une ou plusieurs plaques de placoplâtre. La plupart des activités peuvent être filmées en 10 à 20 minutes.
Figure 2 : Enregistrement d'une partie des travaux
3. Check
Inclure les artisans qui ont effectué le travail dans le processus d'amélioration. Les personnes qui effectuent le travail sont beaucoup plus proches du gaspillage dans les processus et connaîtront probablement la meilleure façon de l'améliorer. Vous trouverez ci-dessous une feuille de calcul que nous utilisons pour décomposer une vidéo en valeur, en non-valeur nécessaire et en gaspillage. À chaque instant, nous regardons la vidéo et déterminons dans quelle catégorie se situe l'activité.
Figure 3 : Classification des activités en catégories
4. Adjust
Rassemblez toutes les idées et réflexions des artisans qui ont effectué le travail et concevez une méthode de travail qui deviendra la nouvelle norme. C'est l'une des meilleures façons d'introduire des innovations dans votre projet en faisant participer les artisans au processus d'amélioration. Lorsqu'ils se rendront compte qu'ils jouent un rôle important dans la conception des méthodes de travail, la résolution des problèmes et l'amélioration du projet, ils développeront et partageront leurs idées plus ouvertement.
DÉFIS
Le défi le plus difficile à relever lors de la mise en place de la première étude d'exécution est d'obtenir l'adhésion des travailleurs artisanaux. Il est important de souligner que les études vidéo sont conçues pour aider les travailleurs à s'améliorer et rendre l'entreprise plus compétitive. Les vidéos ne sont pas utilisées à des fins de surveillance et de contrôle ou pour des licenciements. Le tableau 1 présente certaines des réactions négatives que nous recevons de la part des corps de métier et nos réponses.
RÉSULTATS
Grâce à l'utilisation d'études vidéo, nous avons considérablement amélioré la productivité de notre main-d'œuvre. Parmi les autres avantages de cette pratique, citons :
- Amélioration de l'identification des risques de sécurité
- Amélioration des quantités stockées et des lieux de stockage
- Identification des besoins en outils et équipements plus performants ou plus appropriés
- Optimisation de la taille de l'équipe et réduction du gaspillage dans l'attente
- Améliorer le moral des artisans et la satisfaction au travail
- Améliorer la qualité en éliminant les retouches et les erreurs
- Diminution du temps de travail
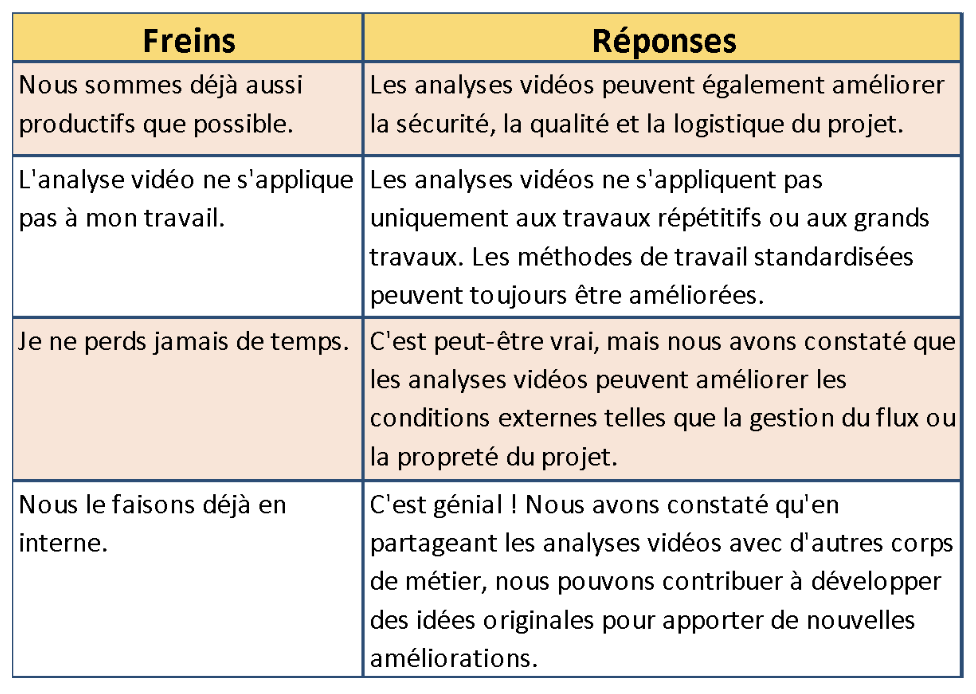
Tableau 1 : Freins à l'implémentation et réponses apportées
ENSEIGNEMENTS TIRÉS
Les principaux enseignements que nous avons tirés sont les suivants :
- Aller sur le terrain Observer (Gemba)
- Demander pourquoi ?
- Respecter les personnes qui effectuent le travail
- Impliquer les artisans dans la résolution des problèmes
- Apprendre à détecter les gaspillages dans nos méthodes de travail
- Apporter des améliorations (Kaizen)
- Créer des normes
- Répéter
Dans le secteur de la construction, les salaires des artisans représentent la seule dépense importante d'un projet et pourtant, ils constituent souvent une ressource sous-utilisée. Leurs commentaires, leur expertise et leur potentiel ne sont souvent pas pleinement exploités. L'étude de la première exécution nous donne un moyen de nous engager avec les artisans et d'obtenir leur aide pour améliorer les processus de travail.