Contact Information
info@leanconstructionblog.com
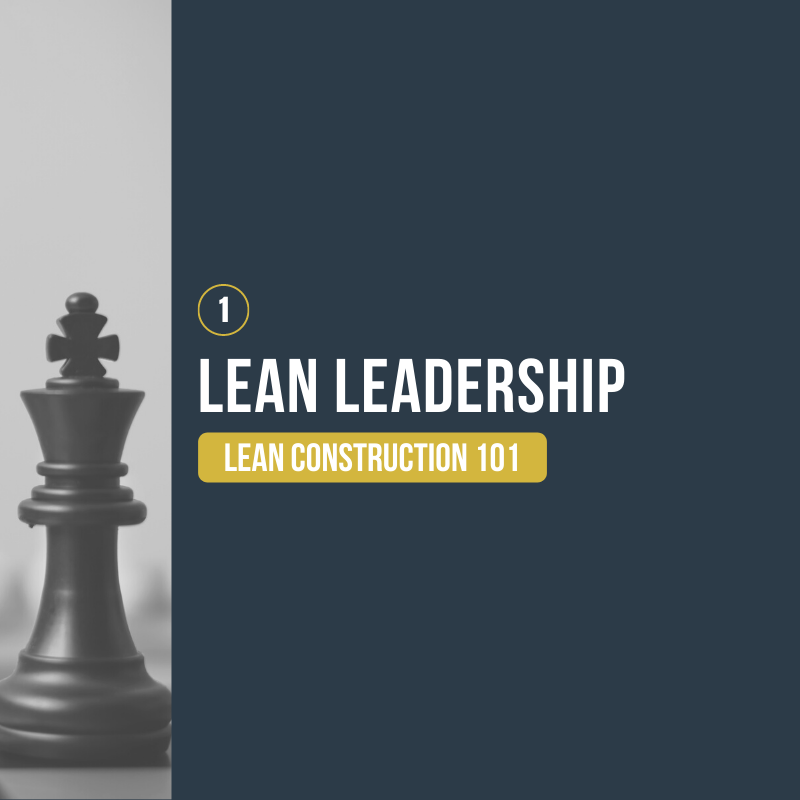
The Lean Leadership Pattern Puts People at the Center of a Challenge
Leading is about WE rather than ME. It comes from a recognition that I can take care of myself while we take care of each other, the customers, and the company.
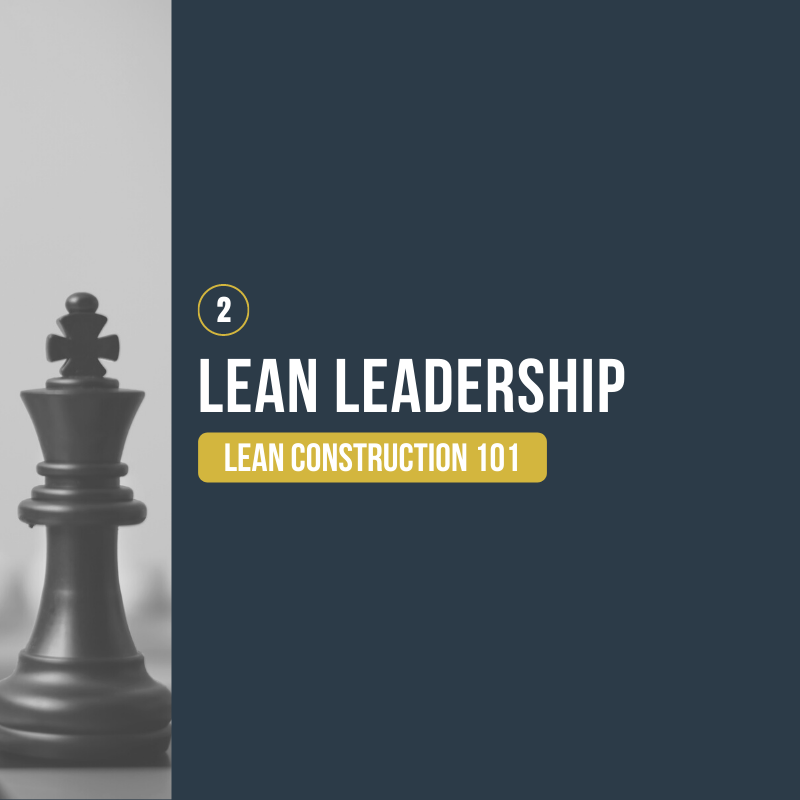
Leaders Start by Aligning and Committing to a Challenge
Lean leaders keep attention to what is good for customers, stakeholders (supply chain, partners, the community, etc.), team members, and the company. Aligning the interests of all is ideal.
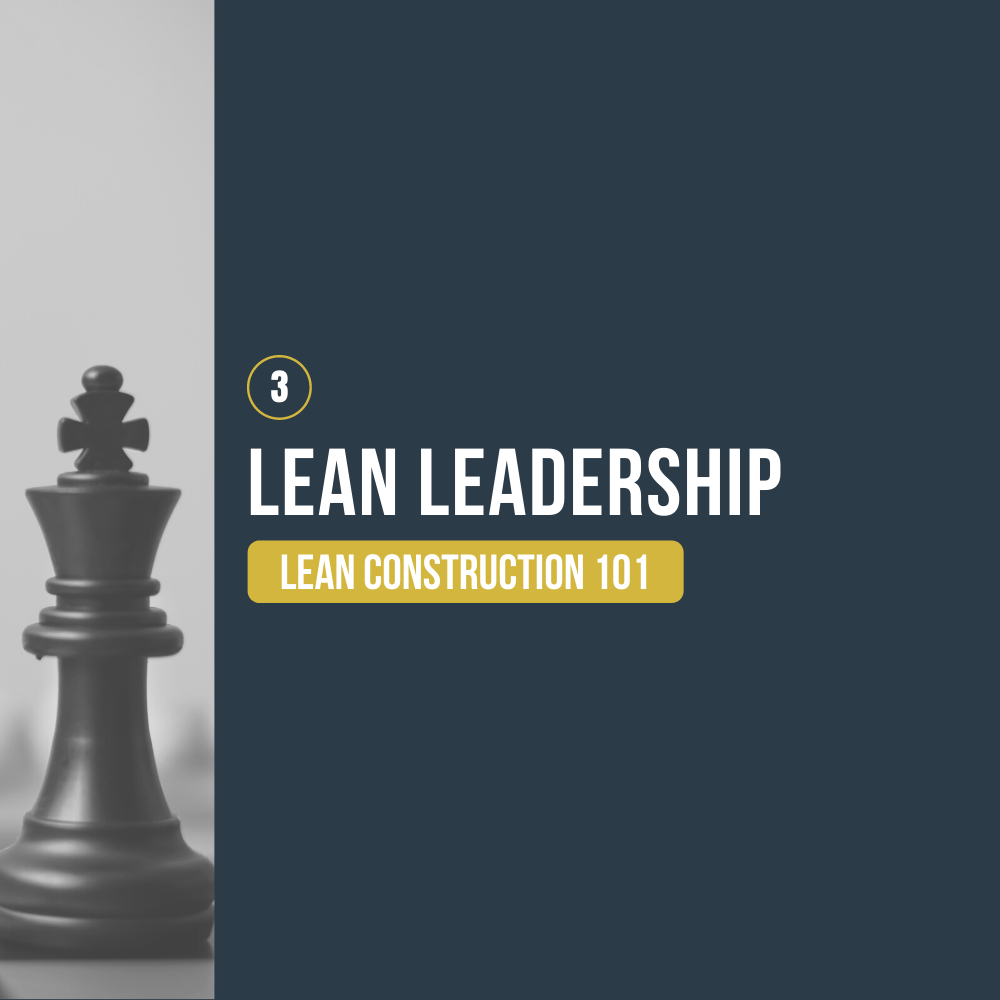
Using Study-Adjust-Plan-Do for Experimental Learning
Experimental learning follows Dr. W. Edwards Deming’s cycle of improvement which turns everyone who uses it into a scientific thinker. People typically call it PDCA for Plan > Do > Check > Act.
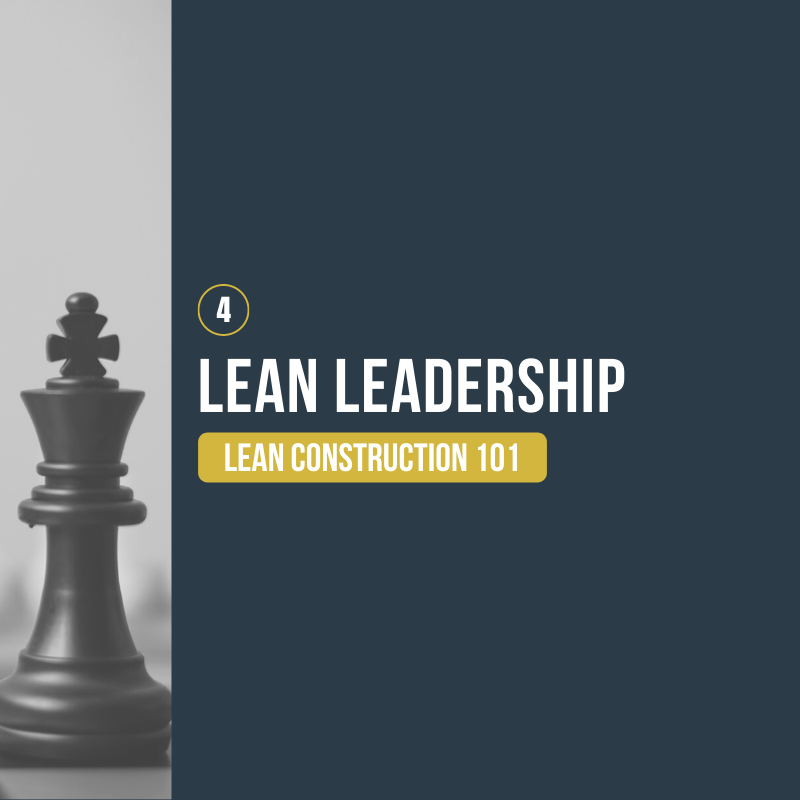
Leaders Take a Systems Thinking Perspective for Making Change
Thinking in systems has been part of the Toyota Way since the 1950s. We just didn’t know it, or did we? Like many other Japanese manufacturers, they learned about quality and production at the feet of Dr. W. Edwards Deming, one of the people after WWII who helped them get back on their feet.
Leaders Make Learning the Ongoing Payoff for the Team and Themselves
The Toyota Way principles #9 Grow Leaders and #10 Develop People and Teams are key responsibilities of people who are leaders. It starts by developing oneself as a leader. This is accomplished with ongoing study and more importantly by leading for learning.