The Lean Construction in Europe is a series that features Lean practitioners working in Europe. In this series, William Power interviews lean leaders and shares lessons learned. This series highlights how people are currently applying Lean in their projects and how they are progressing on their lean journey. The goal of this series is to connect people with the lean practices that they are currently using. We want to share stories about what they are learning and how they are improving their practice.
1. Hello Aleksi. It is a pleasure to chat with you. Can you introduce yourself and give us a brief introduction to your construction career and experience?
I am the first Finnish takt construction evangelist, coach, and assistant, enthusiastic about
transforming the global construction industry. My goal is to improve the lives of tradesmen, the
built environment, and the way we think about efficiency.
My Lean journey began after six years at Nokia, which was a leader in operational excellence
and Lean, after I started working on cruise ship cabin refurbishment. In 2016, I transitioned to
the construction sector as a consultant and Partner at Vison Oy. In Finland, the takt construction
transformation has progressed in two-year phases, focusing on:
- Repetitive construction 2016–2018
- Non-repetitive construction 2018–2020
- Mega project general scheduling 2020–2022
The key question, which I explore in my upcoming book, is how to shift the value chain towards
industrial flow production. Currently, I am transforming €2 billion/year shipyard operations
towards takt, which presents a new level of challenge. I am eager to connect with a peer group
from companies undergoing similar large-scale transformations.
2. What results have been achieved with takt construction?
Takt construction has led to zero-defect deliveries, 30 to 50% reductions in lead times and labor
hours, and better sleep for management.
3. I am impressed with Finnish construction’s Lean maturity. Can you tell us how, as a
sector, Finland’s construction partners have advanced their Lean application and
maturity?
A. Public Alliance projects are excellent for developing innovative methods due to their
large scale, demanding owners, and risk-sharing. Over €10 billion worth of alliance
projects have been initiated since Vison Alliance Partners was founded in 2012.
B. In a small market, word spreads quickly when people collaborate and share ideas.
Group development programs like RAIN and IPT, both under LCI Finland, and Building
2030 under Aalto University, have fostered collaboration. Aalto University is a world
leader in the number of annual takt papers.
C. Location-Based Scheduling has become the de facto standard in Finland, thanks to Olli
Seppänen’s work on developing the framework, his consulting, and the development of
the Vico scheduling software. LPS has also been widely used for a long time.
D. Finns have always taken architecture and construction seriously, resulting in some of the
world’s most functional buildings. The perfect 21°C indoor climate is taken for granted,
even with temperatures of -21°C or -31°C outside. Buying a Finnish house should be as
obvious as buying Italian fashion.
4. I have read the case study on the cruise ship cabin refurbishment [1] and the scale of
production throughput achieved from Takt is very impressive. How applicable are these
concepts and approaches in wider construction?
These concepts can be applied to any human endeavor with the right adjustments. Throughout
my consulting career, I have focused on demonstrating the applicability and value of Lean
principles to construction projects. Nowadays, it only takes a week of workshopping with a client
to get most people on board. That is my promise. The rest of the implementation can be led by
experienced LC, LPS, AWP, or PPI consultants.
5. What do you perceive as the biggest obstacles and challenges to Lean application in
construction?
On a personal level, making exact forecasts can be intimidating after decades of blame culture.
The term "schedule" has a negative connotation, as it implies a rigid plan that must be followed
without deviation. In contrast, a takt plan is meant to help improve daily operations by making
deviations visible. For example, a hunter at a shooting range does not aim at the center
expecting to hit it but to know how to adjust the sight for the next round. A significant part of takt
planning workshops is fostering this adaptive mindset.
On a macro level, strategic marketing is a challenge. General contractors have power, owners
face cash flow problems, subcontractors deal with cost issues, and some people have ideas for
solutions but lack the capacity to restructure the value chain or transactions.
There are also concerning examples of lost billions in industrial construction due to excessive
capital tied up and a lack of understanding of the Efficiency Paradox, as presented by my hero
Niklas Modig. This paradox is the hardest concept to grasp in Lean, and anyone who says Lean
is only common sense has not genuinely thought about it.
6. What is the key to starting Lean turnarounds?
The Efficiency Paradox in Lean refers to the possibility of improving quality and labor
productivity by improved speed of production, i.e., reduced throughput time. This is hard to
believe unless you have experienced the change yourself. To avoid requiring an impossible
amount of belief, the direct value of speed must be integrated into day-to-day decisions,
balancing resource, and material costs with the benefits of speed. This allows the organization
to reduce batch sizes and Work in Process holistically towards 'thin‘ production, quality, and
efficiency, with belief to Efficiency Paradox growing along the way.
When the figure is large, say €100 million for shortening a billion-euro hospital project by a year,
considering rental income, project overheads, and more efficient hospital use, attitudes change.
Tackling difficult issues becomes more meaningful as the size and benefits of the challenge are
better appreciated. It is also easier to abandon outdated ideas and practices when it is clear
they are not helping to achieving new results. This makes it possible to try something new and
initially challenging, like takt construction.
7. How do you help people start takt construction?
I work directly on real projects in three steps. First, I lead the creation of a takt concept for a
project or its single phase over a week-long workshop, culminating in a go/no-go decision by the
team on Friday. It is crucial to reserve this decision for the workshop participants so they can
fully commit during the week without fear of committing to something that does not work for
them or having a conversation about takt feasibility before sharing the same facts.
The second phase scope depends on the targeted maturity level of takt production. We have
updated our IGLC paper on this [2], based on three International Takt Forums with Berkeley
P2SL for more information. The third phase involves learning, adjusting, and maintaining
discipline through daily and weekly management.
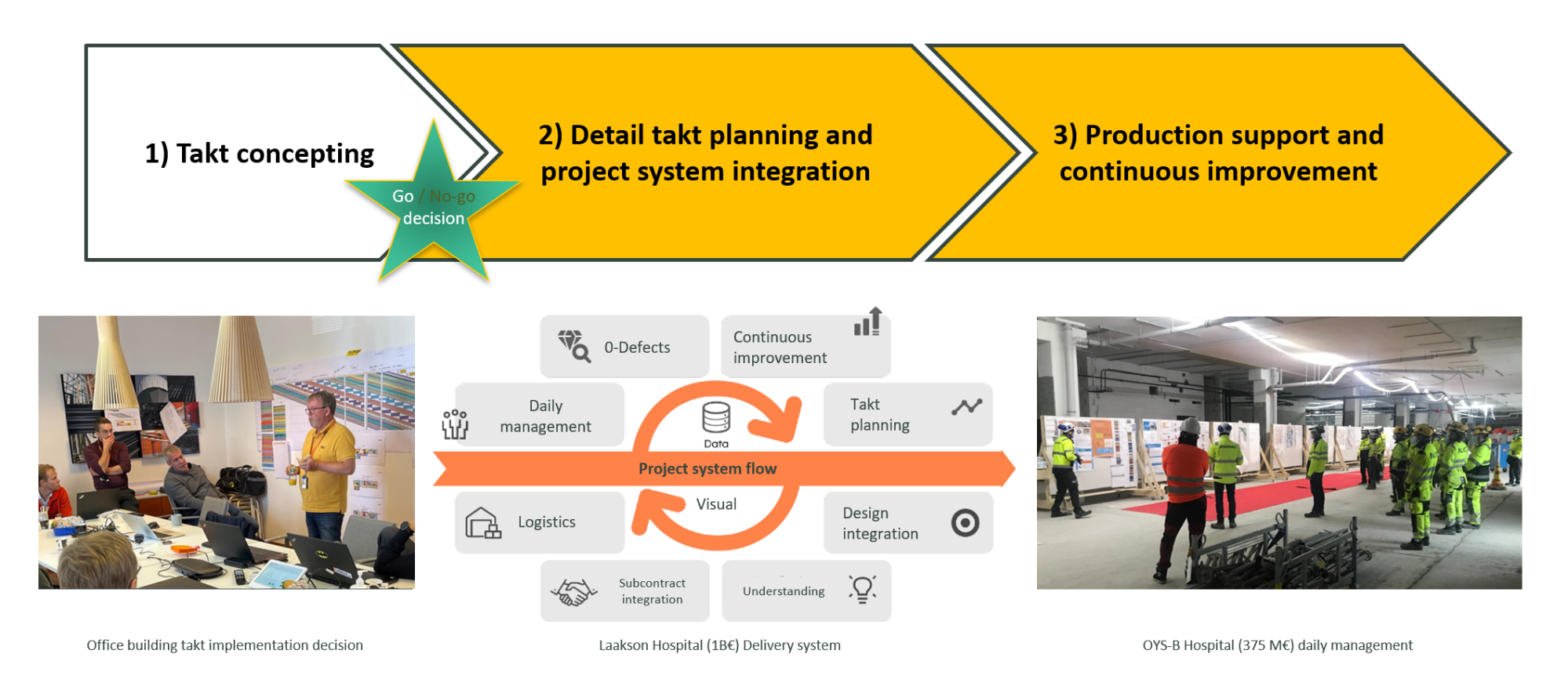
IGLC articles
1. Cabin refurbishment https://iglc.net/Papers/Details/1338
2. Takt maturity model https://www.iglc.net/Papers/Details/2284
3. Takt Production as Operations Strategy https://iglc.net/papers/Details/1902