The Lean Construction in Europe is a series that features Lean practitioners working in Europe. In this series, William Power interviews lean leaders and shares lessons learned. This series highlights how people are currently applying Lean in their projects and how they are progressing on their lean journey. The goal of this series is to connect people with the lean practices that they are currently using. We want to share stories about what they are learning and how they are improving their practice.
1. Hello John. Can you tell us about yourself and the work you do at Cygnum?
I am the Managing Director of Cygnum, a Cork, Ireland based timber frame manufacturing company. I studied forestry at UCD and began my working life in the sawmilling industry. In 1997 I set up Cygnum with the owners of Palfab, the sawmill I worked with. We made our first house with basic tools in the corner of a shed and from there, Cygnum has gone on to become one of the most advanced timber frame manufacturers in Europe. Today, I work closely with our senior team to steer strategy, innovation, and operations.
2. Could you provide a brief introduction to Cygnum and describe the organisation’s development in the Irish construction sector?
Cygnum designs, manufactures, and installs precision-engineered timber frame structures for the Irish residential and commercial sectors. We support some of Ireland’s largest homebuilders and are currently producing approximately 30 fully insulated timber frame homes every week from our Macroom based factory.
We have grown from a workshop-style business to what is now considered one of the most automated timber frame plants in Europe. In 2017 we invested over €7 million to double the size of our factory. This added to our output capacity, allowed us to take more site elements into the factory (insulating, airtightness installation, fitting plasterboard to party walls) and ultimately create an additional 50 jobs.
2025 is another major expansion year. We are halfway through a building project that will see us almost double the size of our factory again and double our output capacity. This development will be complete before the end of the year.
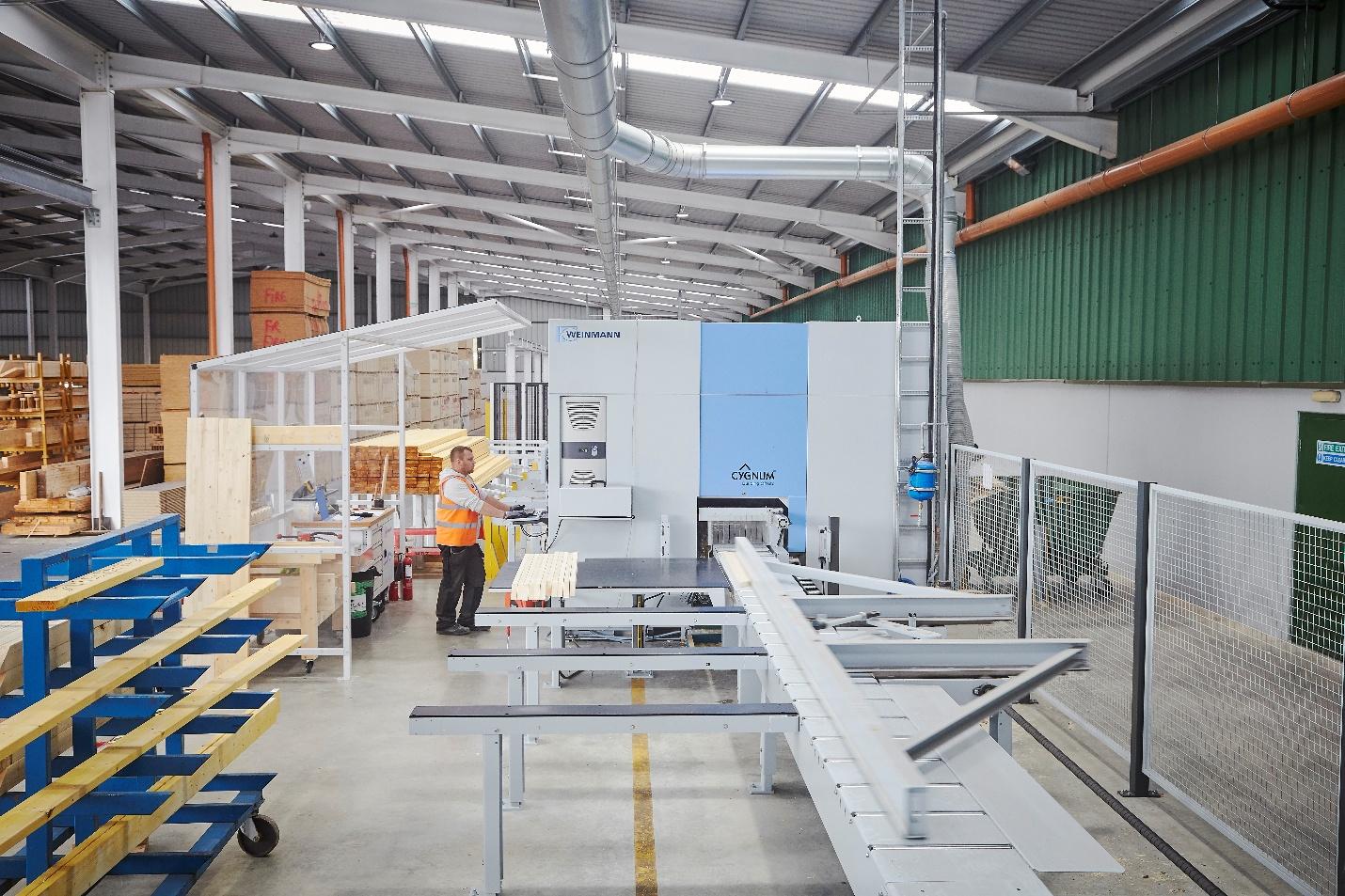
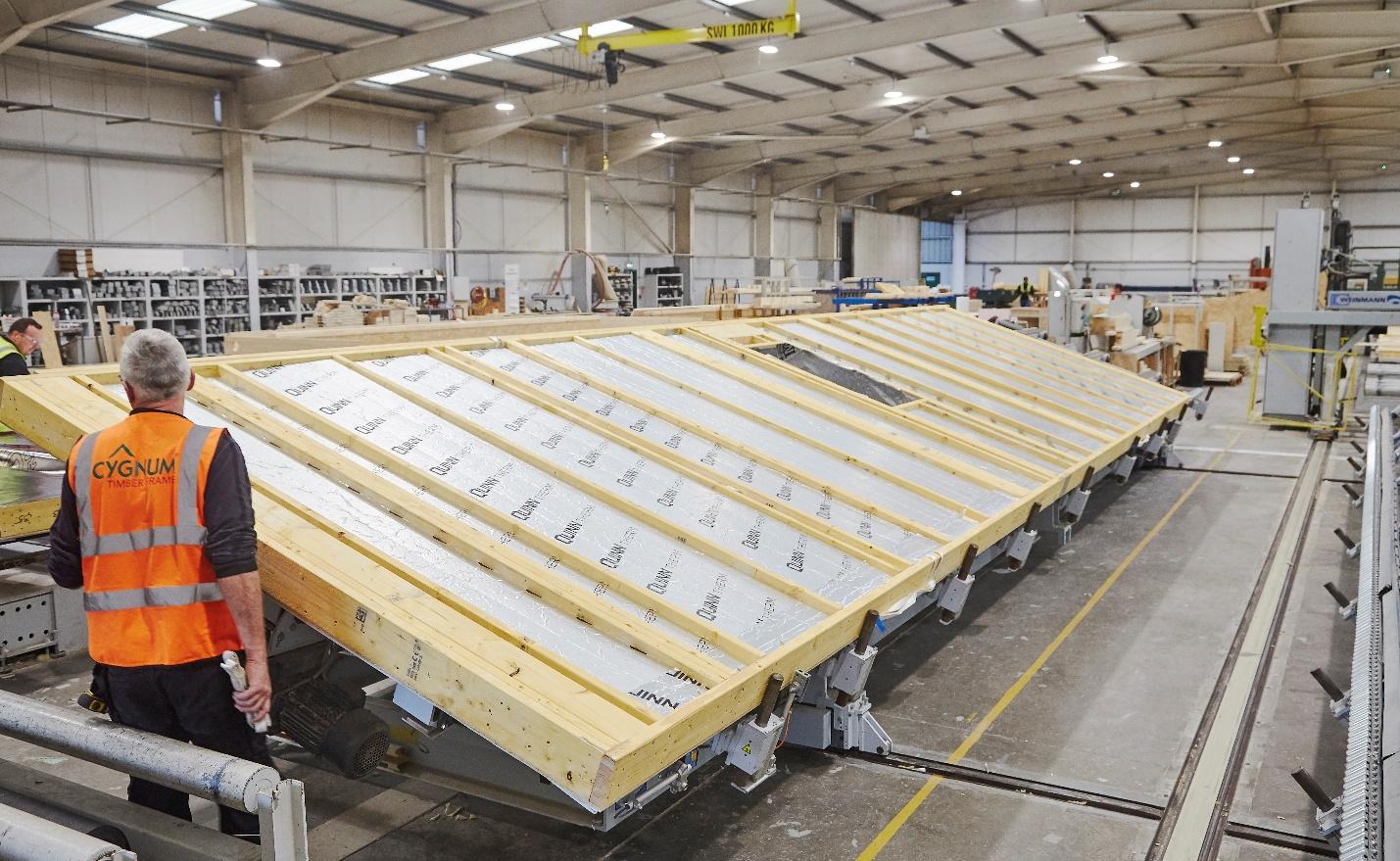
3. Cygnum’s production system follows Lean practices. How did you first learn about Lean and Lean Construction, and how has it influenced your work methodology?
We were first introduced to Lean principles through Enterprise Ireland’s Lean Business Offer. That was a turning point. It helped us see real performance improvement that comes from systems thinking, streamlining flows, eliminating waste, and empowering people to problem-solve in real time. It is also something that aligns well with our values. Off-site timber frame construction lends itself naturally to Lean principles as the manufacturing model is carried out in a controlled environment, is often repetitive and highly efficient when engineered and optimised well. We have taken that a step further by digitising almost every part of the production process. Today, every workstation on the production floor receives live task-specific instructions, design updates in real time, and our scheduling is fully dynamic enabling us to meet our customer’s changing needs as they arise.
4. Can you describe some of the Lean practices utilised in your production system?
Lean modelling is embedded across our digital manufacturing environment:
- Digitally-Driven Operations: Our entire workflow, from design through to production and delivery, is integrated through a centralised digital platform.
- Design for Manufacture and Assembly (DfMA): We model each home we build with offsite assembly in mind, simplifying junctions and creating structural components and elements that can be lifted into place with minimal on-site work.
- CNC Precision: Recent investments in CNC equipment have transformed the accuracy, repeatability, and speed of our plant. On average there is approximately 16,000 individual components required in each of our timber frame homes, and every timber piece is pre-labelled and optimised for rapid line assembly.
- Smart Scheduling: Our digital system recalibrates production flow in real time, based on project updates. That level of flexibility has been a huge asset in recent years and has made our model very dynamic enabling the maximum product output capacity to be achieved.
- Zero Paper Floor: In early 2024 we transitioned to a fully paperless production floor. Digital visuals and work instructions at each station reduce error, eliminate rework, and keep production flowing with minimal machine downtime.
5. How does your on-site installation contribute to the speed and scale that is now demanded in Irish house building?
Our offsite manufacturing approach allows houses to be built much faster than building with traditional methods of construction. Our panels arrive on-site fully insulated and pre-fitted with air-tightness membranes and plasterboard which reduces the need for multiple trades onsite. We deliver to a well-planned delivery schedule, and we can erect a typical pair of semi-detached houses in 2 days.
We have seen a big cultural change in how sites are managed in the last few years. Well run sites that adopt Lean methodologies, such as the Last Planner System, are almost like an extension to our factory processes. A great example of this is a site operated by Cfield Construction site in Ballyvolane in Cork. The space is ready, sequencing is followed, and our on-site teams are involved in short daily stand-up planning meetings (referred to as huddles). That collaborative environment helps to ensure the builder gets maximum benefit from the system. In the case of Cfield, they take between 3 and 4 houses per week and have reduced construction time from 26 weeks on a recent traditional site to 11 weeks on the Ballyvolane project. Because they are using timber frames and adopting the lean systematic approach on site, they are also finding it a much easier site to manage despite the high level of output.
6. Modern Methods of Construction is seen as a potential solution to Ireland’s house building crisis. What are your thoughts on enabling full volumetric construction in the timber frame industry?
Timber frames in Ireland have advanced significantly in the last 10 years or so. As well as supplying completed structural walls, floors and roofs, the standard supply package now includes factory fitted insulation, airtightness membrane, service battens and plasterboard to party walls. Though it is likely that more will be completed in the factory in time, it is imperative that anything we do brings advantages like cost and waste reduction and improved quality to the overall process.
Full volumetric construction where almost all trades are completed in the factory and units are delivered fully assembled will have a role to play in addressing our house building crisis. There are challenges in this industry like pipeline certainty, design alignment with the manufacturing process, cost alignment and building system certification. It is however playing a major role in other sectors like education and even in the supply of emergency housing for Ukrainian refugees, so it is likely to play a significant role in time.
7. How do your improved and innovative processes contribute to carbon reduction and energy efficiencies in comparison to 10-15 years ago?
Timber itself is the most sustainable mainstream raw material in the building industry. It sequesters carbon from the atmosphere while growing and stores this while in use. On average a 3-bed semi-detached timber frame home for example, will store approximately 15 tonnes of carbon over the structure’s lifecycle.
Our own production and operation systems have evolved dramatically. Every aspect of our operation has been digitised, optimised, and refined. We repurpose 90% of timber offcuts and have introduced solar energy, which provides over 20% of our energy needs.
I strongly believe public procurement policy should reflect these achievable benefits of building with sustainable materials. Stipulating timber frame for public housing and infrastructure would be a straightforward way to help Ireland meet its carbon reduction targets.
8. Finally, what do you define as your company’s mission?
To make better homes for people and the planet. This is central to all aspects of how we run our business.
Watch our factory and installation process featured on TG4’s Na Builders:
We’re also very proud to have contributed to several life-changing builds on RTÉ’s DIY SOS: The Big Build Ireland, including the current series. It’s a privilege to use our systems to make a direct difference in people’s lives: https://cygnum.ie/diy-sos-the-big-build-ireland/
4 people, 4 Houses, 4 Days
Built to Innovate