The Lean Construction in Europe is a series that features Lean practitioners working in Europe. In this series, William Power interviews lean leaders and shares lessons learned. This series highlights how people are currently applying Lean in their projects and how they are progressing on their lean journey. The goal of this series is to connect people with the lean practices that they are currently using. We want to share stories about what they are learning and how they are improving their practice.
1. Hello John. Introduce yourself and tell us about your work.
I am a Project Controls and Management specialist working in the Life Sciences industry, specifically Pharma. I have been in Switzerland since early 2017 and I have previously worked on Semiconductor and Energy projects in Ireland and the UK. I have worked in Planning, Quantity Surveying and Project Management roles, allowing me to bring a more integrated approach to project execution. I have been lucky in my career to date as I have worked on great projects and made good friends along the way.
2. How did you first come across Lean Construction (LC) and what were your first thoughts?
I first came across Lean when I was working with Suir Engineering on the Intel site at Leixlip, Ireland. Intel put a huge emphasis on Lean methodologies to ensure maximum value through efficient, safe, and quality delivery. There was an enthusiastic sense of competition between contractors on the Tool Install at the Intel Site - to be competitive you needed to be able to respond quickly to changing environments and demands. With Suir, I learned the importance of ensuring customer value. Suir were at the time (and I am sure still are) leaders in Quality. They had an off-site fabrication hub that supplied the site with Electrical and Mechanical containment modeled by the site-based BIM team. This made site assembly fast and efficient and reduced any waste. DPS Engineering were site coordinators, and it was at a DPS led seminar that I was first introduced to the Last Planner® System.
3. What Lean methodologies are you using in your work?
During the C&Q phase of a recent project I worked with the execution teams to develop three-week lookaheads and daily planning and tracking tools to set weekly targets, facilitate daily tracking, and to progress the overall schedule. I had eight different validation area teams to work with. For the daily planning I developed a simple template for listing tests for completion and a simple Gantt chart to show when the test is planned. In seven out of the eight areas the plans were working, and the only further action required was to coach and sometimes monitor and control the proper and timely use of the plans. In the one area where it did not work I met with the team lead, and I was surprised to discover how frustrated he was with the system; he could not build or adhere to an accurate plan. I explored this situation in more detail and began to ask questions - why was it so difficult to forecast a week’s work and what was happening that was causing the plan to fail?
I discovered that there was an unusually elevated level of bugs in the automation system, and this was causing many failures, meaning tests needed to be repeated. The knock-on effect was that the successor activities that he had planned were no longer successors and the traditional waterfall method was not going to work anymore.
I implemented a Scrum framework:
- The team and it’s lead selected and prioritized the weekly scope of work.
- On a Monday morning at the daily stand up, each team member had a starting point.
- The team would review their scope for any blockers for starting the tests, any constraints were highlighted, and actions assigned to remove or resolve any issues. We used post-its to track the progression across each test.
- The test execution would begin, each team member would report back on their progress each morning - if completed they would move to the next priority.
At the end of the week progress was appraised, and a Sprint review (lesson learned and observation session) was conducted by the team to look for ways to improve delivery by streamlining the execution process, and removing any resistance encountered in handover or review. This approach worked wonders in this area - all because I listened carefully to the team’s needs, built a prototype, and tried something new. It quickly became clear that this system would also be more beneficial in the other validation areas also; areas where I had not considered any further improvement because the first attempt was working fine. I have learned that it is important to understand that one size does not fit all, even with Lean, you must listen to the team’s needs and understand the problems. Do not be afraid to try something new.
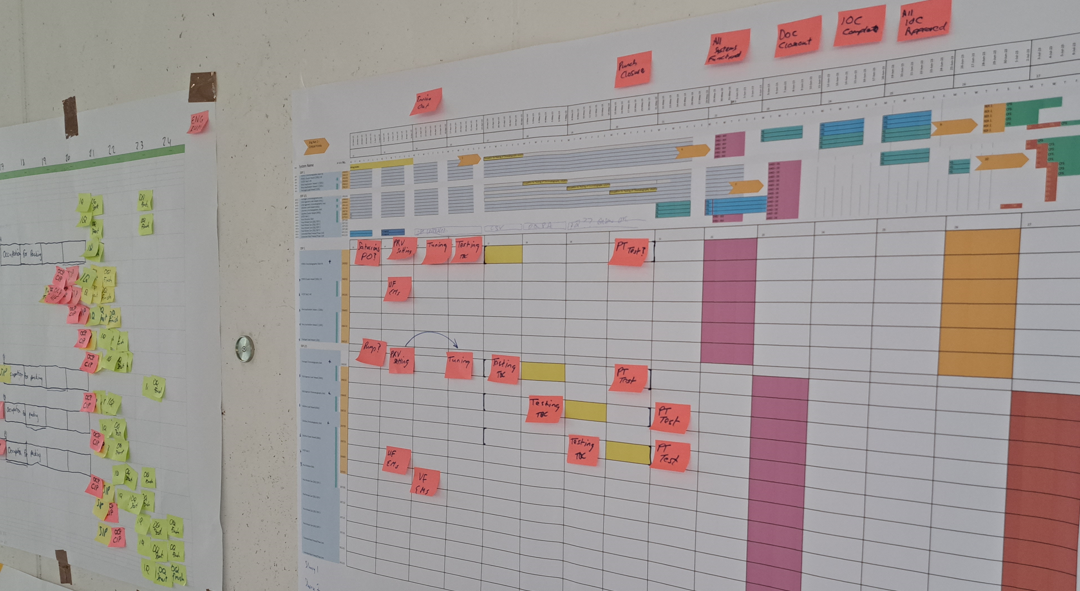
4. What issues with existing methods does the Lean approach address?
For this situation using a Lean approach allowed the team to be more agile in their execution. One of the main goals during commissioning is to check the system for any flaws and failures as it can be difficult to build a robust weekly plan to account for these in advance. In trying to do so we were causing frustration amongst the team as they did not have a plan that they could follow; we were losing time replanning activities and updating work plans. Introducing a Scrum approach brought great energy and interest back into the team. The daily stand ups, or Tier meetings as we called them, became much more interactive and engaging. As the team members were now all responsible for moving their post-its and representing their own progress there was an enthusiastic sense of healthy competitiveness.
5. Have you found resistance to introducing new methods?
It all depends on the situation. If you have a new scope of work and the team has just formed it can be quite easy to coach the team and introduce Lean concepts. However, we all have some level of cognitive bias for getting attached to ideas that are our own. If you have a team that is mature, and they have a system that works for them then it can take time to win them over. I have found the key is understanding their challenges and applying relevant Lean methodologies to solve their issues. It is much easier if you introduce a framework that will save time and make the team’s lives easier.
6. What other challenges do you encounter and how do you overcome these?
Projects by their nature are ever changing, each day will be different to the next, and the needs of the team change as the project moves forward. As new interfaces emerge it is important to be able to react quickly to this. An example is managing cross-functional communication and collaboration between teams. As you move through construction, commissioning, and qualification there will be a requirement for teams to coordinate with other validation areas and departments to support transfer testing, to schedule calibrations or to handover to Quality for review. This is a change and needs to be managed carefully, identifying the key stakeholders, and setting clear expectations for what is required to support efficient collaboration. I have found using Lean methods such as creating visual tools to map out the interface or the frequency of a task to be helpful. Gemba walks can also help identify any gaps in the process and bring instant insight and feedback through observing the team at work.
7. Can you tell us more on the hybrids of Scrum and Last Planner System you have used to manage and track C&Q into Operational Readiness?
I used the Last Planner System to map out the testing for each validation area. This brought instant visibility to the deliverables and allowed us to challenge the execution strategy and timelines. We used Last Planner to track overall progress and forecast completions for IC / OC / IQ / OQ for each system. At the next level of detail, I implemented more detailed three-week lookaheads and weekly Scrum sprints. The three-week lookaheads allowed us to plan for system handover or to schedule downtime for testing. As an overall execution strategy, it was critical to ensure there was a strong link between each method - Last Planner System depicted our strategy and overall direction, the three-week lookaheads gave us visibility on the mid-term outlook, and the Scrum hybrids ensured we were agile and efficient in our daily and weekly execution.
8. Did you find that visualization of the plans and processes helped the team?
I am a huge fan of creating visual tools and timelines to bring the plans and processes to life. For a plan to be successful it is crucial that the teams can understand the short-, mid- and long-term path of the project, especially as traditional planning tools can be restrictive and even confusing at times. I have always found that breaking the scope of work up into smaller and easily understood work packages can bring instant clarity and trust in the system. It is important to listen to the teams and understand the challenges that they are facing and then try to build and implement a framework that supports them.
9. What are the main challenges facing the construction industry over the next decade and what role do you think Lean can play in addressing these issues?
As an industry we have an exciting future ahead of us. There are huge challenges facing us in the Life Sciences and the Energy sector and the solutions will be delivered by project teams. In Life Sciences, the focus is to be able to respond quicker to the market, getting new therapies out to patients faster, while ensuring the highest possible standards of quality and safety are adhered to. We must innovate today to be competitive for tomorrow and this means looking for improvement in everything we do, looking for diverse ways of doing things, and looking outside of our industry for innovative ideas.
Traditionally in the construction industry we have always been strong in our delivery skills; we are experts in analyzing, planning, and getting things done. However, we tend to rely on methods that have worked for us in the past. We need to have the courage to innovate, to challenge the status quo and to build up creative confidence through questioning, observing, associating, and experimenting. This will be especially important in tackling the energy transition and ensuring the path to net zero is successful. As the technologies we need to support this do not exist yet, we must be agile enough to be able to change our strategic capabilities to ensure we are best placed to support and embrace technological advances as they occur; Lean thinking and methods that drive innovation will play a vital role in ensuring this.