Despite the importance of construction in our lives and the global economy, the traditional construction system still has several shortcomings. In short, there are 7 main challenges facing the construction industry (CI) nowadays as shown in the figure below:
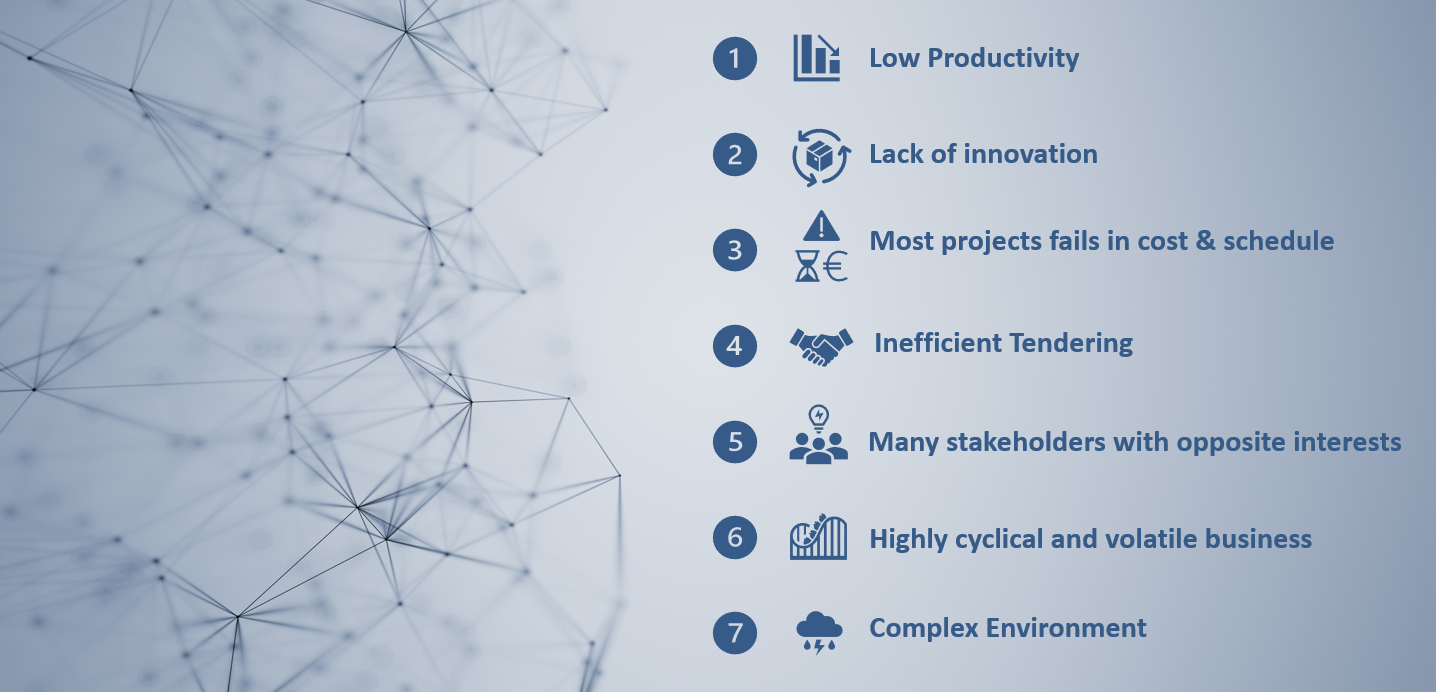
Figure 1. The 7 main challenges of the construction industry (CI) nowadays.
1. Steady low productivity
The use of body-worn sensors such as accelerometer, gyroscope, and magnetometer that enable the measurement of workers’ posture and motions has gained greater attention for construction activity monitoring. Accelerometers are resilient and robust in difficult conditions compared with image sensors, besides having a small size, good accuracy, and reasonable power consumption. Another advantage is that they can be embedded in wristbands to classify activities performed with hands, such as masonry, ironwork, and carpentry.
2. Lack of innovation and delayed adoption
In 2014, the European Commission published an R&D ranking of investment in the industrial sectors and share of main world regions for the world’s top 2.500 companies. In this report, the construction sector appears in the last position amongst a total of 15 main industries. Also, most of these investments in construction are in software solutions and rarely in project management methodologies.
3. A huge amount of projects fails in cost and schedule
According to the report of the McKinsey Global Institute in 2017 (1), 70% of construction projects in the world were not completed on budget and 61% of them with delays in the schedule.
From an economic perspective, the construction sector has historically been a very significant part of every country's economic engine, both for its contribution to GDP and for its ability to create direct and indirect jobs.
4. The traditional tender is not efficient
The traditional tendering system based on design, bid, and build does not work because the main contractor takes part in the project once the project is defined so they cannot propose better ideas to solve problems. Also, once the construction works have started, a lot of issues are out in the open and it is often too late to avoid the cost, schedule, and risk overruns, as some experts already explained in 2010 (2).
5. A lot of stakeholders only take part in the construction process temporarily
The construction industry has unique characteristics such as multiple stakeholders with different needs and opposite interests that provoke a high industry fragmentation.
Furthermore, the workforce is unstable and most of the workers even change their jobs to a different sector once they have finished their construction work.
6. It is a highly cyclical and volatile business
The activity of the sector is polycyclic. In other words, the variations in the sectoral output levels are directly affected by the variations in the economy in general.
7. It operates in a complex environment
Unlike the manufacturing industry, the CI carries out its production process outdoors in most cases. Because of this, both manpower and products are affected by meteorological factors, among others. Decision-making is difficult, and some tools are starting to be used to help technicians. In this sense, industrialization and the use of precast elements would help to improve it (3).
So how can Lean Construction help?
In that context, Lean makes sense because as Daniel Jones defines Lean consists of “creating the most value for the customer while minimizing waste of resources, time, energy, and effort. Lean thinking and practice help organizations become both innovative and competitive, which in turn allows them to become more sustainable” (4).
So, how Lean could help to fight against the problems of the current construction?
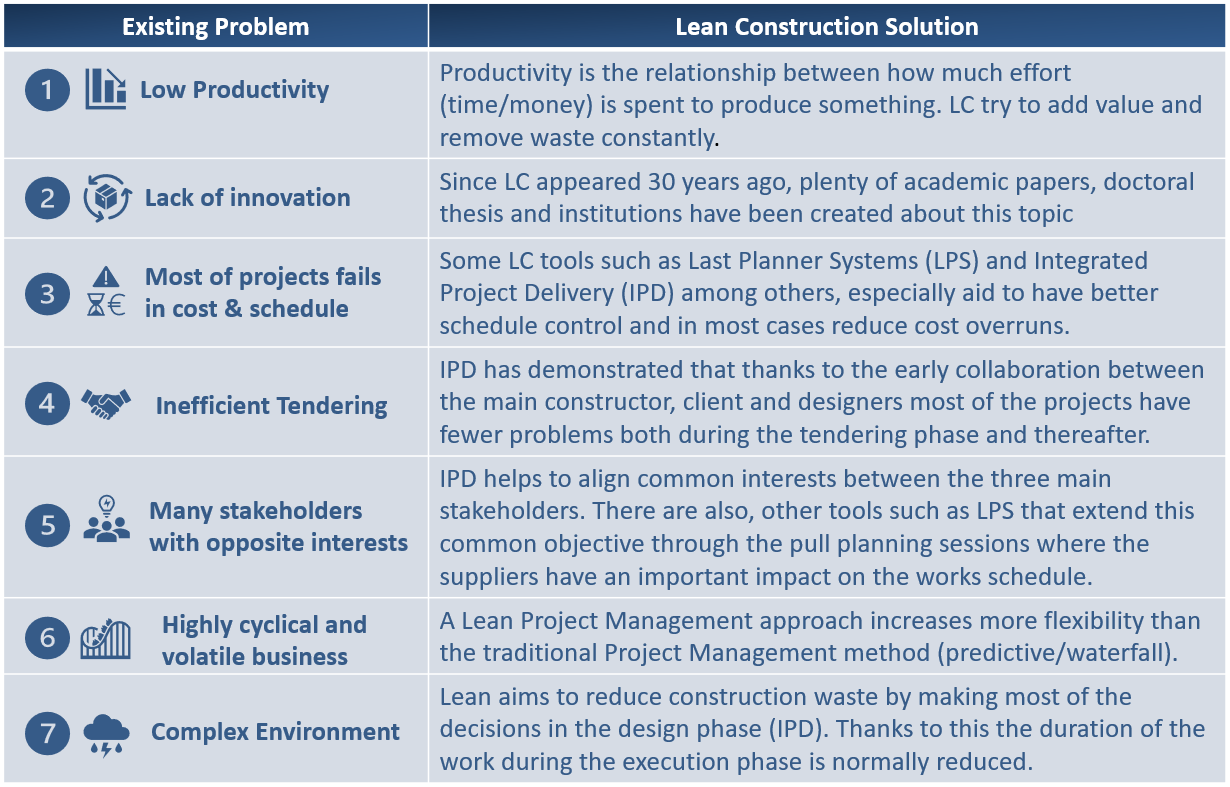
Table 1. Lean Construction solutions for the current problems of the Construction Industry.
Therefore, in order to fight against the current VUCA (volatility, uncertainty, complexity, and ambiguity) world, new methodologies like LC which could enhance productivity and react fast to the constant changes of the complex construction sector will be key.
References
1. Barbosa F, Woetzel J, Mischke J, Ribeirinho MJ, Sridhar M, Parsons M, et al. Reinventing Construction: A Route to higher productivity. McKinsey Global Institute. 2017.
2. Mossman A. Traditional construction and lean project delivery – a comparison. The Change Business Ltd. 2015;(11):2–6.
3. Bjornfot A, Stehn L. Industrialization of Construction. A Lean Modular Approach. In: 12th Annual Conference of the International Group for Lean Construction. 2004. p. 1–14.
4. Womack JP, Jones DT, Roos D. The machine that changed the world. Simon & Schuster, editor. Vol. 35, Business Horizons. 1992. 81–82 p.