Bridging the Gap
As we progressed into a new project there were many challenges not generally encountered on more conventional process jobs.
The size of the project meant we would have to recruit Supervision and Craft Labour that would have no experience on a semi-conductor facility installation.
The skill sets and knowledge required to install services to the Client’s standards and in a semi-conductor environment were not widely available in the industry. We developed suitable training classes to bridge the experience gap but the main thing we needed was time and time was not available due to the aggressive nature of the schedule.
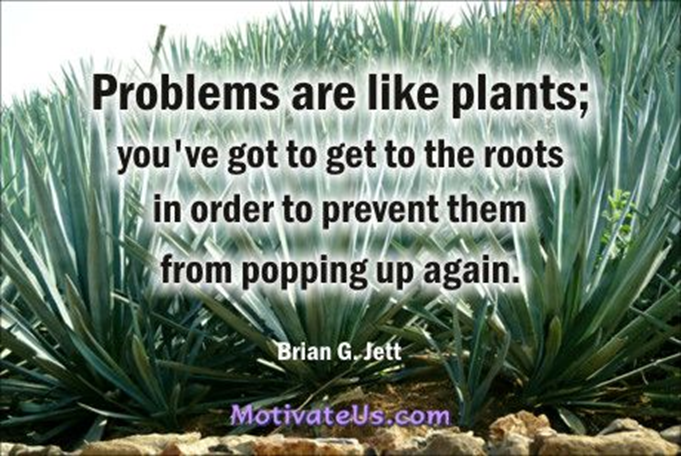
Getting to the Root Cause
The Project Management team set-up various discussion/meeting forums to plan our approach to meet the QAQC goals for the project.
The QAQC team met regularly with the Construction team Supervision to get aligned on the Client’s specifications and standards. The level of inexperience was a constant challenge during this period. The net effect of our inexperience could be measured through the lists of punch items generated for each line. At this point in the project, we were averaging 11 punch items per line.
This was a huge drain on resources and as a further consequence, overall productivity. A conservative estimate rounded the cost of each punch item at €100. This resulted in the cost of not getting it right the first time for each line was €1100.00. At that point in the project, we were walking approx. 200 lines per week meaning, we were losing €220,000 per week to punch items.
The first quarter of the first year of the project saw a ramp never before experienced on our Client’s previous projects. To meet the challenge, we went into task force mode. At this point the first signs of improvement in the overall quality were visible. Given that the project was at such a crucial stage the small improvements we were making were important indicators that the experience we were gaining was beginning to influence the overall quality of our installations.
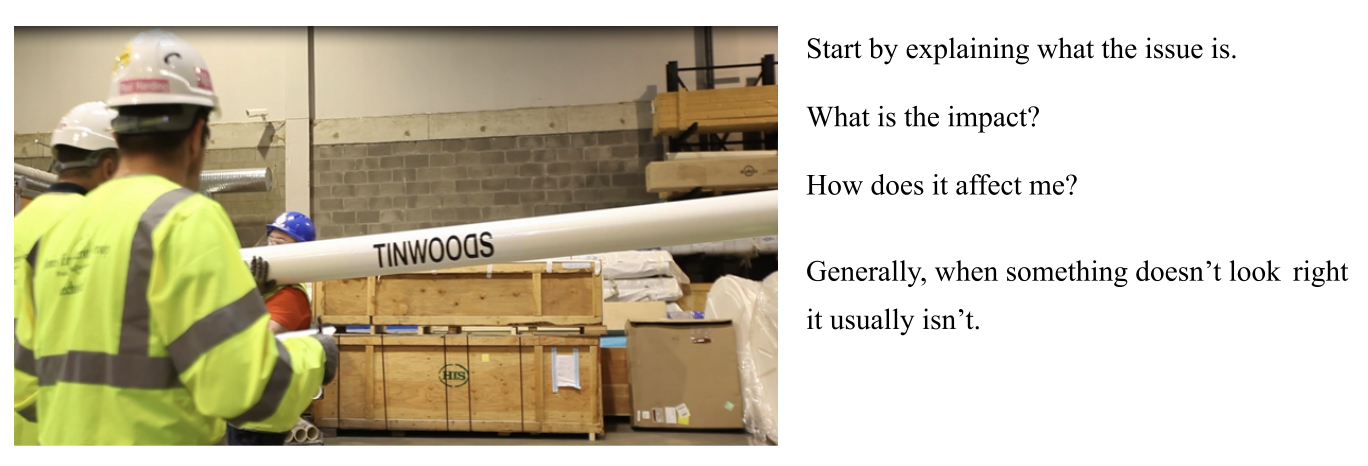
Continuous Improvement
The next objective was to build on these improvements, and this proved a difficult nut to crack. The improvements made were based on experience gained but to make further improvements we needed to find ways to focus more on the quality of our end product, (IE line handover).
At this stage in the project there was no doubt the basic quality had improved but the amount of detail and nuances contained in the specification meant any further improvement would be hard to achieve.
We looked at the profile of the punch items we were generating, and the biggest single issue was labels. At the early stages of the project labels accounted for over 60% of all punch items generated and as we entered the second quarter, they still accounted for over 60%.
To tackle this issue, we developed a more comprehensive label training plan. It involved awareness classes and practical training in the field. Two complete installations were labelled, and we reviewed these with the Client’s QAR to confirm alignment. These were then used as a template for follow-on installations.
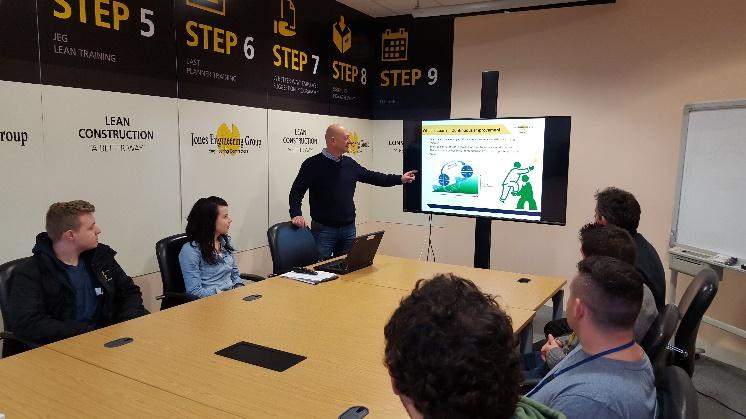
This strategy over a period had a significant effect on the number of label issues being generated. The percentage dropped from an average of 62% to 38% of the overall as we transitioned through the next phase of the project.
Right-First Time
As the project went on significant progress was made on improving construction efficiency. All the key indicators were showing clear improvement in our performance. In relation to quality, we continued to make progress with the general protocols; however, we still struggled to get to our goal of zero punch list items for each line transmitted.
As we started into the last quarter of the first year our punch list rate was remaining at 5.5 items per line average. We struggled at this point to make any further improvement even though we did have performance highlights, but we generally struggled to maintain these.
The issue with the number of punch items being generated was raised at a development session with our Project Teams and a team was tasked with reviewing performance to date and developing a strategy to improve that performance.
The team was made up of people from BIM, Move-in Crew, Installation Crew and QC. The BIM and Move-in team members brought fresh eyes to problems which challenged the approach we had been taking to the issue. A strategy to promote a “right-first-time” approach and generate the data from the new initiative was implemented.
The Construction Managers and the Site Supervision were tasked with achieving a reduction in the number of punch items generated by driving a “right-first-time” approach to the issues that were accounting for the bulk of the punch items, (e.g. loose brackets, label issues, plumb, level, square etc).
Within two weeks we reduced the punch item rate from 5.5 to 2.2 items per line. In the next two-week period, the punch item rate was reduced to 0.9 items per line.
The punch item rate continued to decrease to an average of 0.4 snags per line and this rate was maintained until the end of the project. In this period, we’ve had several outstanding achievements from individual crews completing a number of super complex installations punch item free.
Setting and maintaining this standard has been achieved by the site level Supervision, a motivated Craft Labour Force working in conjunction with our company’s QCR’s. We now have developed a culture where we deliver services/systems and installations punch item free as standard.
In the second year of this project, we have inspected and transmitted 3059 lines. The Client QAR has inspected approximately 80% of these lines and has picked up 7 minor issues.
Today we still are aiming for zero punch lists, and we believe with the right approach this is achievable on all our projects.