The unique power of Lean lies in its ability to maximize quality and resource productivity by minimizing throughput time and Work-In-Process [1]. A key element of this strategy is the implementation of one-piece flow, which has transformative potential for the construction industry by altering processes and, more importantly, people’s behavior [2].
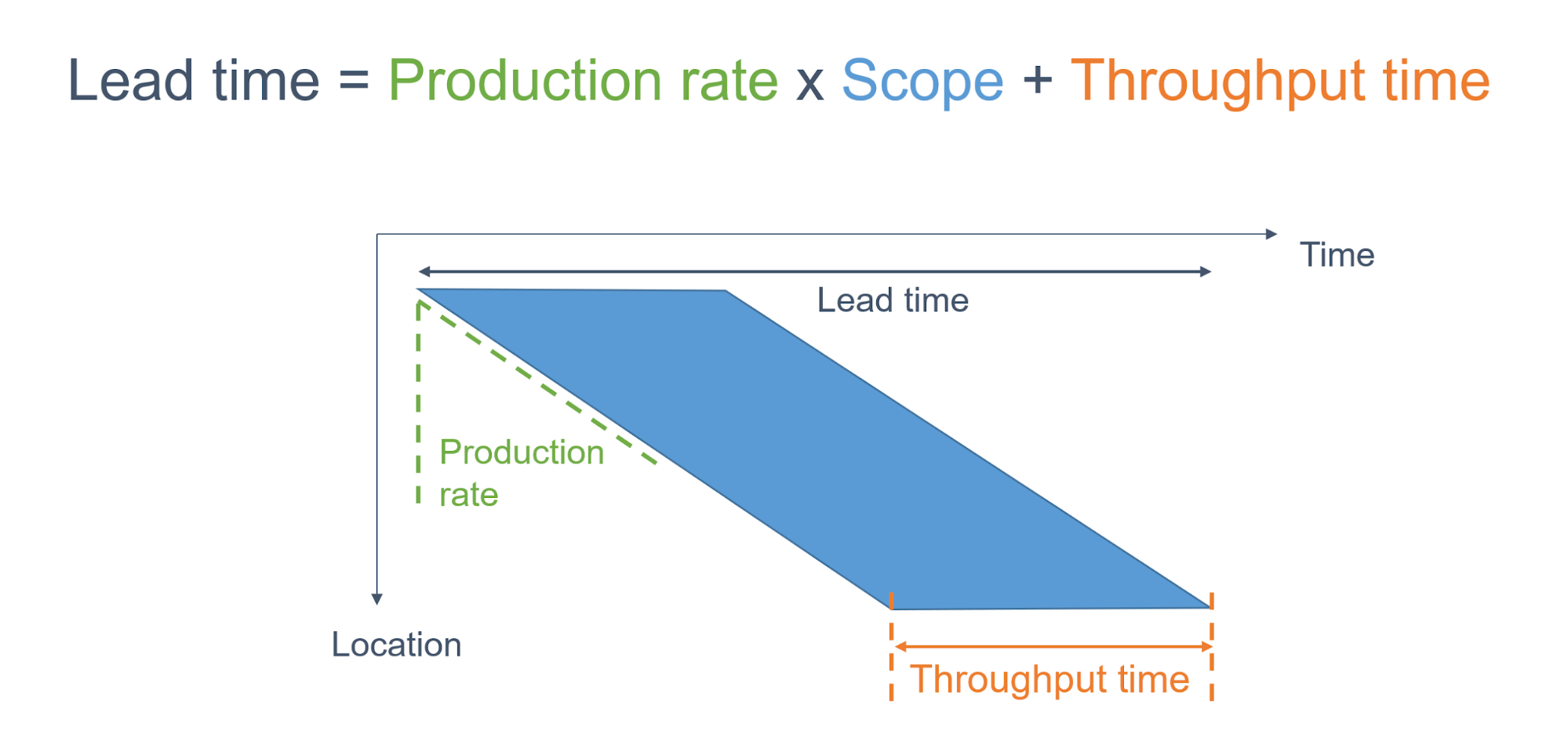
The application of these principles has significantly transformed the construction industry, particularly in Finland, where takt production has made considerable advancements in recent years. This shift was catalyzed by the successful implementation of one-piece flow in the cruise ship cabin refurbishment industry. By reducing takt time to a mere 15 minutes and segregating logistics from value-adding work, productivity of the work crew doubled on the first attempt. Further productivity improvements were made using daily KPIs, deviation root cause analysis, and smaller kaizen sprints between projects, resulting in a fourfold productivity increase over seven projects [3].
Following this, Finland's construction industry has witnessed a growing adoption of takt production. In 2021, almost all finalists for the construction site of the year award had employed takt production. Notably, the Haahtela’s 352-room hotel project operated on a 4-hour takt-time. The award-winning Helsinki Airport Terminal 2 project, an IPD megaproject, utilized a 1-day takt, resulting in a four-month lead time reduction, all while staying under budget - an exceptional achievement for a public megaproject. This was driven by the project owner, Finavia's demand for takt planning [4].
However, while implementing one-piece flow and reducing batch sizes and takt-time, it's crucial to understand its impact on the people involved. Two key areas to consider are:
- Resource Balancing: Effective planning is crucial for resource balancing. Preventing trades from altering their schedules based on other site’s needs or available work area is critical for continuous improvement. Challenges can be addressed with robust planning and resource management strategies.
- Urgency Over Buffers: Most Finnish schedulers have used line-of-balance scheduling methods, often incorporating two-week buffers between activities. While this could stabilize the production system from a factory physics perspective, the value of urgency over buffers has been demonstrated in takt production cases. Smaller WIP buffers lead to improved collaboration and situational awareness among team members.
In response to queries about the reliability of one-day takt schedules, I often say, it certainly isn’t totally reliable, but it can be closely achieved through the adoption of the Last Planner System® weekly re-planning practices. Consistently aiming at a target in a standardized way increases the likelihood of success, much like repeatedly aiming a gun at a target and adjusting the sight between shooting rounds. This mindset shift is a stark contrast to the common practice of large blind buffers in contract interfaces. It's akin to the red or blue pill dilemma in the Matrix movie – do you want to identify deviations and improve the system or remain in comfortable ignorance?
The aim should be short and clear: design a production system that fosters situational awareness for everyone involved, and train people to improve it daily.
References
1. Modig, N., Ahlström, P. (2013). This is Lean: Resolving the Efficiency Paradox. Rheologica Publishing.
2. Womack, J. P., Jones, D. T. (1996). Lean Thinking: Banish Waste and Create Wealth in Your Corporation. Simon & Schuster.
3. Heinonen, A. & Seppänen, O. 2016, 'Takt Time Planning: Lessons for Construction Industry from a Cruise Ship Cabin Refurbishment Case Study' In: 24th Annual Conference of the International Group for Lean Construction. Boston, Massachusetts, USA, 20-22 Jul 2016. https://iglc.net/Papers/Details/1338
4. https://www.rakennuslehti.fi/2021/12/tahtituotanto-ja-hiiliajattelu-tekivat-lapimurron-rakentamisessa-vuonna-2020/