Looking back on the lean management approach
The target of lean management is a value stream. Lean management aims to reduce waste and create a value stream that includes only value. A value stream consists of value and non-value process steps, as shown in Figure 1. Non-value is called waste in lean management.

The procedure consists of the following three steps, shown in Figure 2:
- Identify non-value.
- Cut non-value.
- Add next value.
Step 1 is to identify non-value. You clarify the entire value stream and identify non-value within it. Step 2 is to cut non-value. You reduce the non-value identified in Step 1. Ideally, you would like to reduce it completely, but if that is not possible, you will aim to partially reduce it. Step 3 is to add value. You add new value to the reduced non-value part. Even if non-value is reduced, it is meaningless if it is replaced by another non-value. Value needs to be added to replace the non-value that has been removed, and the reduction of non-value is complete only when this is confirmed.
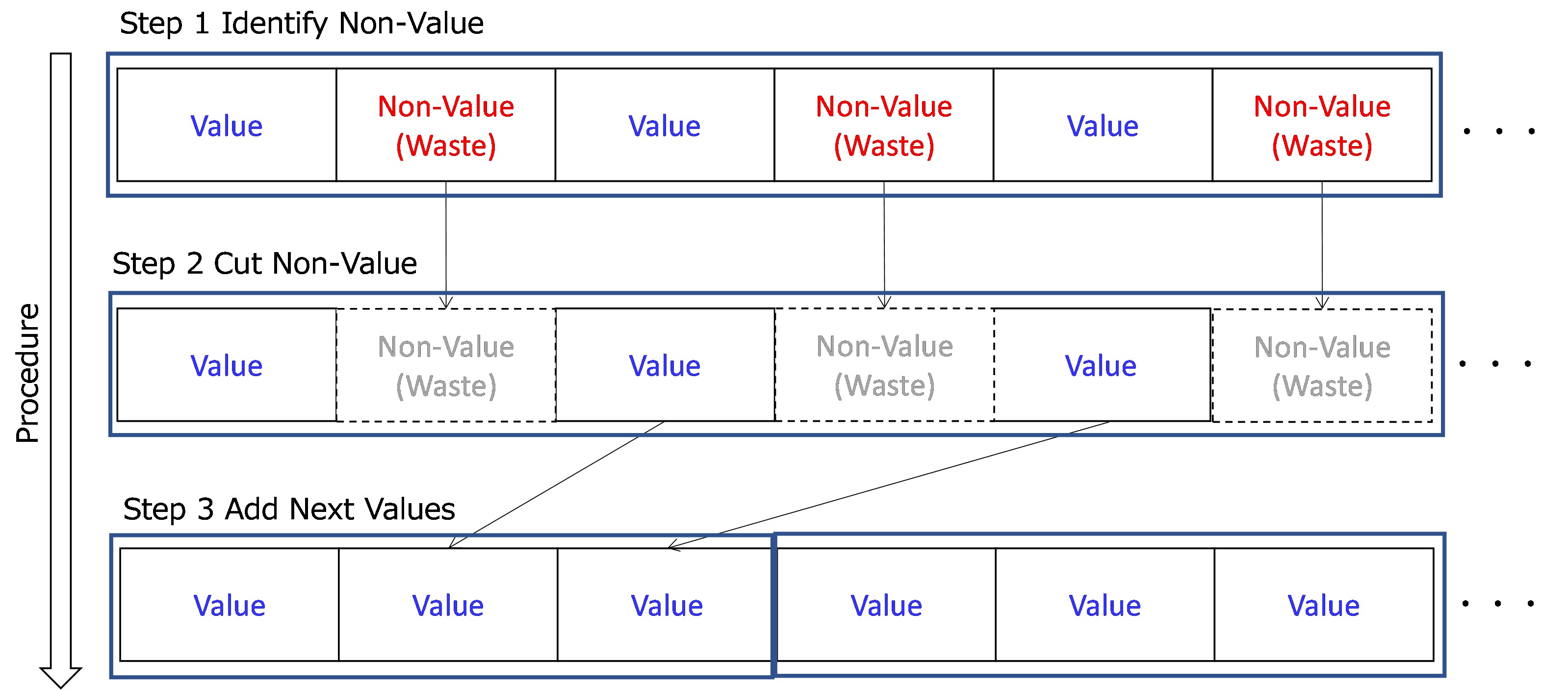
The productivity for the example shown in Figure 3 is calculated as follows. In this article, productivity refers to a process as an input and value as an output. Before waste reduction, the productivity is 3 values/6 processes. After waste reduction, roductivity = output/input = 6 values/6 processes. Comparing the two calculation results, you can see that productivity has doubled. This is the power of lean management.
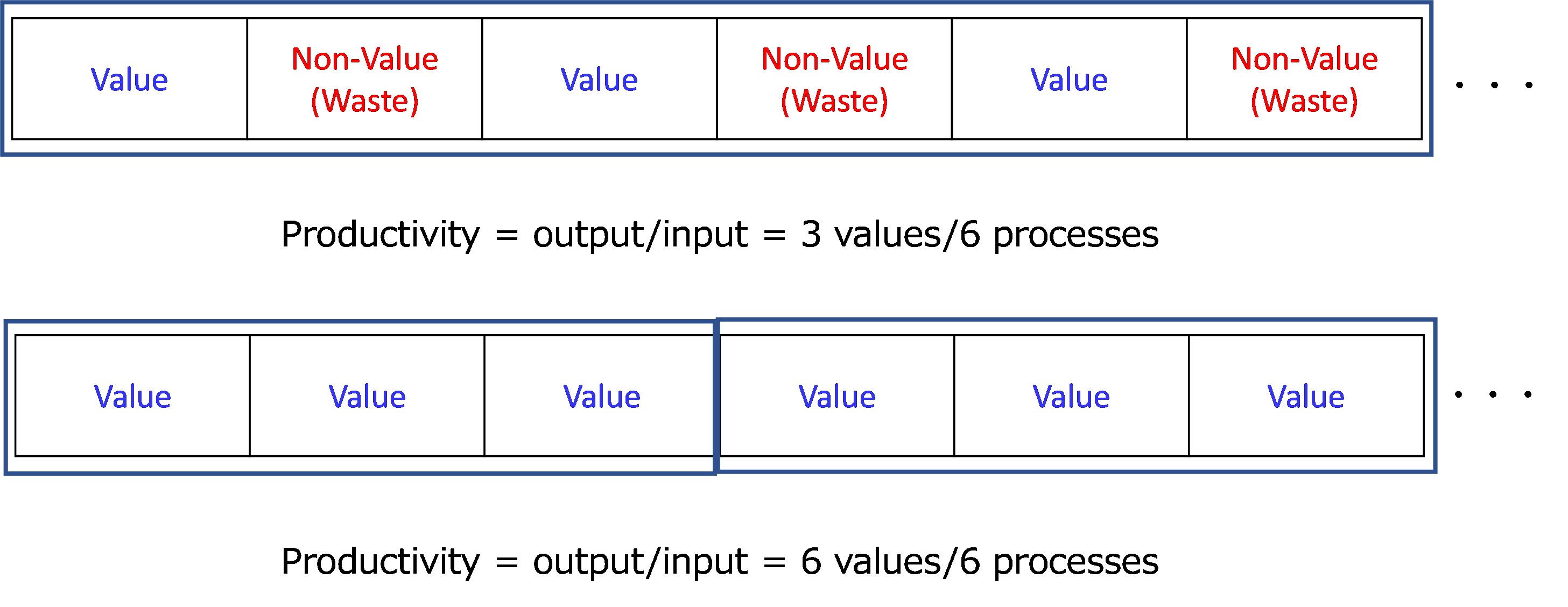
Lean management is a non-value challenge
The history of lean management has been a challenge to non-value. Lean management has divided operations into value operations and non-value operations, and it has gained an understanding of the latter. In industrial engineering, non-value operations are divided into four categories: transportation, inspection, delay, and storage. Toyota's 7 Wastes divides non-value operations into five categories:
- Waste of transportation.
- Waste of making defective products.
- Waste of waiting.
- Waste of inventory.
- Waste of overproduction.
They also showed that there are two types of waste in value operations:
- Waste of processing.
- Waste of movement.
Waste is called “Muda” in Japanese. In Japan, there is a view of non-value called “3 (San)-Mu”, which consists of three things: “Muri”, “Mura”, and “Muda”. “Muri” is something that obstructs safety and rights, and ”Mura” means variation. “Muda” is also similar to the Japanese word “Mottainai”, which was made famous by Wangari Maathai, who became the first African woman to win the Nobel Peace Prize in 2004.
Different classifications are used in each field of operations management. However, Figure 4 shows that although there are differences between them, there are also commonalities. Overall, lean management is the study and practice of non-value science.
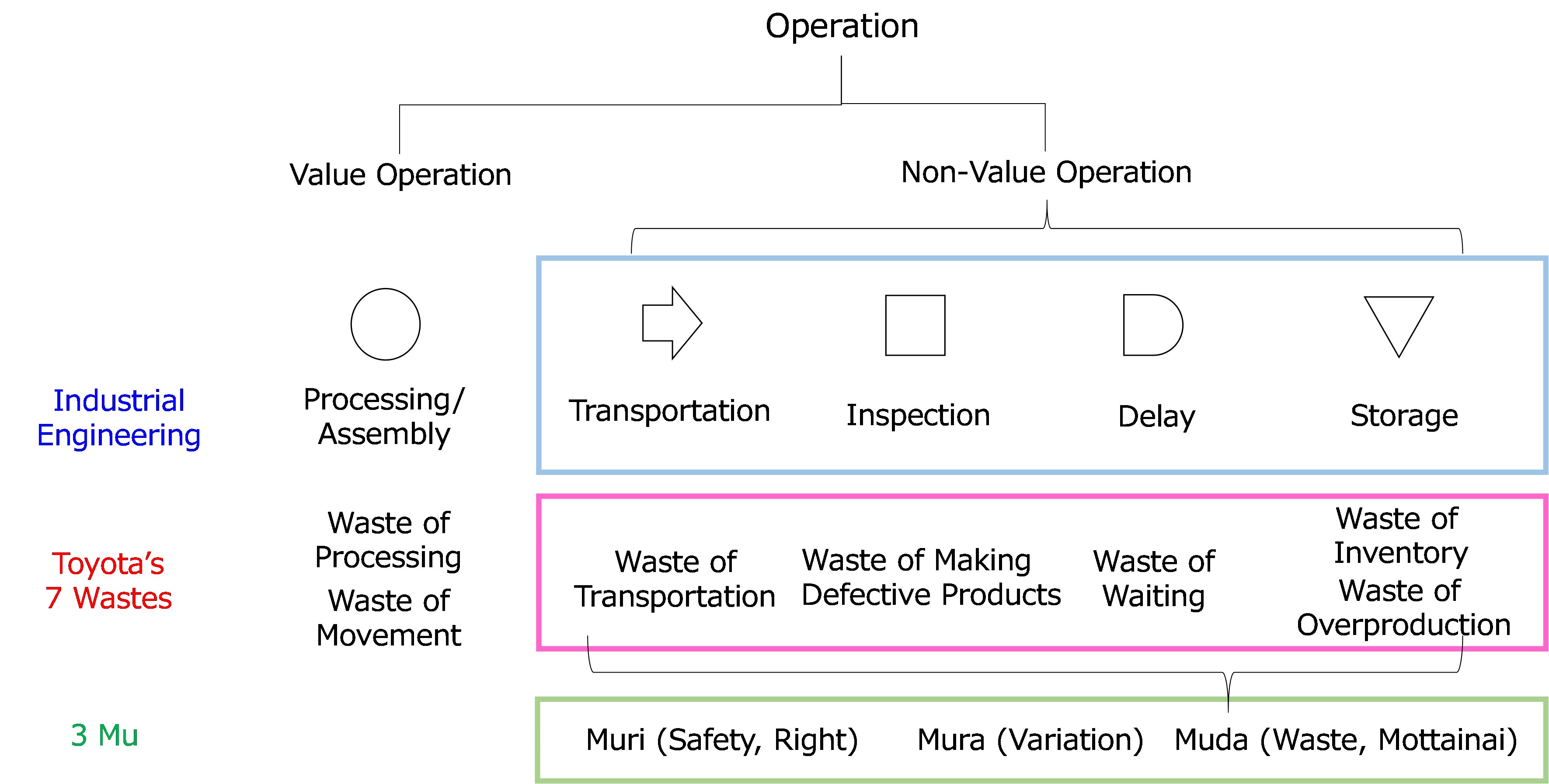
Case study: Letter
Here, we would like to compare cases involving two letter operations. The first case is a hand-made letter. It consists of six processes.
- Select a stationery.
- Select an envelope.
- Write a letter.
- Write an address.
- Put the letter in the envelope
- Waste of processing.
- Send the letter.
The second case is a digital letter (email). It consists of four processes.
- Click a button (or open email app).
- Type a letter.
- Select an address.
- Click a button (to send the letter).
Here is a quiz. How many values and non-values are there in the two cases? Anyone who has studied lean management will understand this answer immediately. The value of the first case is one, namely, “3. write a letter”. Likewise, the remaining five are non-value. The value of the second case is one, namely, “3. type a letter”. The remaining three are non-value. When you calculate productivity by using the method described above, the productivity of the first case is 1 value/6 processes = 0.16 (v/p), and the productivity of the second case is 1 value/4 processes = 0.25 (v/p). Hence, it can be expected that the non-value challenge of writing a letter will improve productivity by (0.25 - 0.16)/0.16 * 100) = 56%.
But, just a moment! What “final world” will we aim for via the non-value challenge? Will it be a world like the one in Figure 5, where you sit at your computer every day and continue to type a letter? If so, how do you feel about that world?
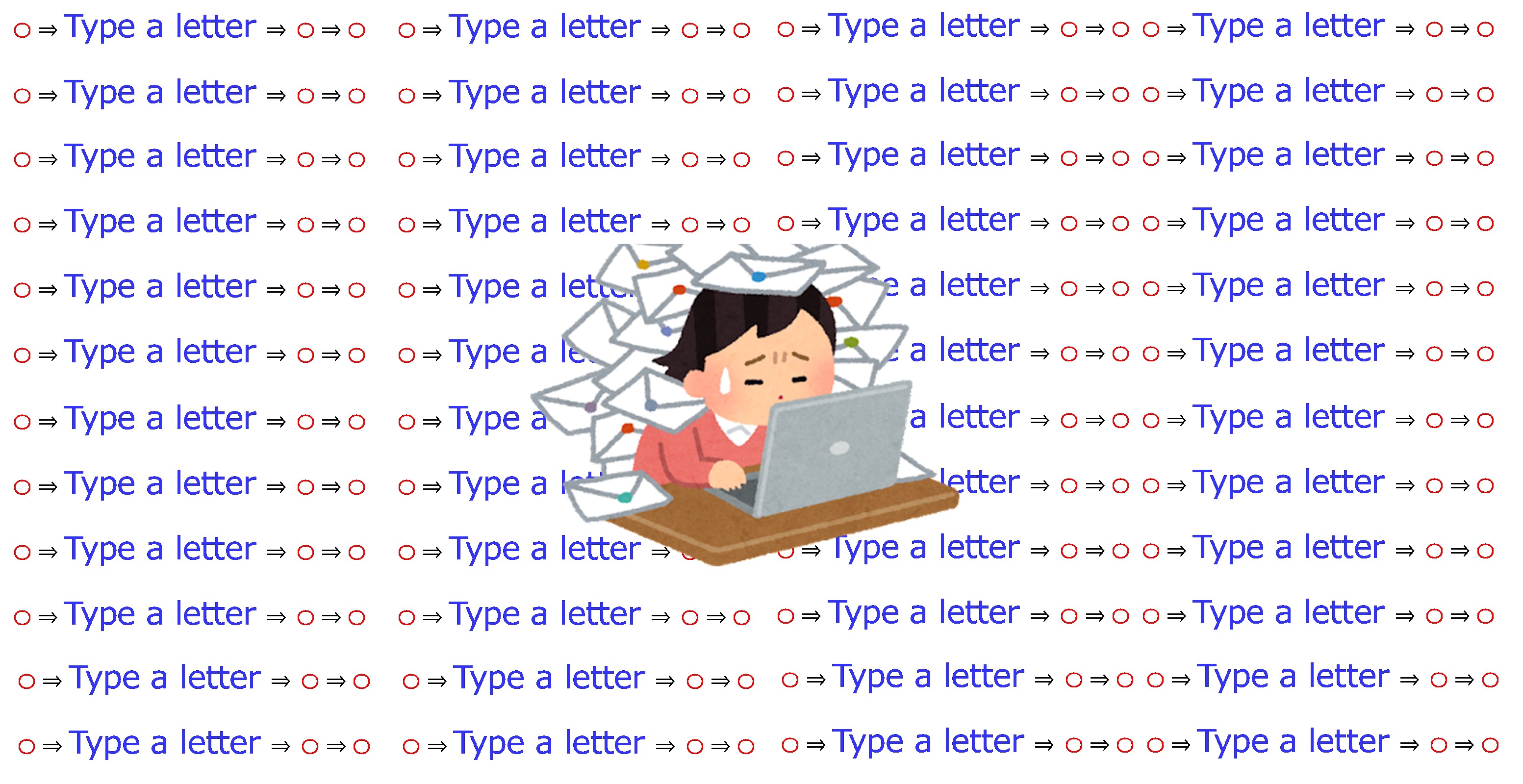
Rethinking non-value
Non-value challenges create a world of mass value operations. There are two risks in this world. The first is a lack of attention to value operations. A situation may arise in which you easily write a letter that should politely convey your feelings to a significant other. The second is the appearance of new non-value operations. As work becomes more efficient, people have probably found themselves looking at their smartphones in their free time. As a result of these two risks, there is a concern that the quality of operations will decrease.
You are now in an era where we must reconsider non-value. Is non-value really non-value? If the purpose of writing a letter is to convey your feelings to someone, is the process of selecting a stationery, selecting an envelope, and submitting the letter to the post office non-value? In the process, it is valuable to take your time and have fun while composing and sending the letter as well as while thinking about your significant other.
Non-value is a concept that views processes only from the perspective of efficiencies, such as time and cost. Just as there are various aspects to people, you need to realize that there are various aspects to processes. You must not overlook the important perspectives within the process. Machines do not currently have emotions, whereas people always have emotions. Work is centered around people, not machines. Therefore, you should think about whether process changes are worthwhile for the people in a workplace. Lean management is about understanding people.