What if you completed a fifteen-month construction project in twelve months? If you are a building owner, you have gained an additional three months of revenue while shrinking the amount of time an unforeseen unknown negatively impacts your project. If you are a construction manager, you have increased your profit velocity in addition to productivity savings.
Most projects fail to achieve their target completion date because they lack a strategy that allows a field management team to successfully address the inevitable unknowns and problems that surface during construction. Instead, projects are traditionally planned as a complex web of networked activities, numbering from the hundreds and often into the thousands for large projects. Within this network the longest set of activities is determined and identified as the critical path that must be managed for the project to achieve its planned schedule.
This networked set of activities is rarely strategic in terms of designing workflow. Prior to my introduction to the Last Planner System® and lean design and construction, I worked as a project scheduling consultant. On one project a client asked me to prepare a schedule that planned all work to be on the critical path. That is because the main utility of these schedules is to prove and disprove claims of responsibility for project delays rather than effectively plan workflow. My client was seeking a reason for any additional work requested by the project owner to result in additional compensation for a schedule delay.
A 20% schedule reduction is consistent with the performance of some project teams observed by colleagues and me on a range of projects. One example is the Lakewood Family Health Center project near Cleveland. The team delivered the 65,000-sf Emergency Services / Medical Office Building facility with an initial schedule of 19 months in 14 months, a 24% savings of time.
Beyond a lack of strategy, the scheduling of complex projects by identifying and linking specific activities is an impossibility. That is because construction scheduling can be accurately described as an “NP-Hard” problem, meaning that the due to the sheer number of variables that inform any complex schedule even a high-speed supercomputer is unable to calculate an accurate schedule in finite time. A relevant mathematical proof of the impossibility of accurate project scheduling is provided in the analogous Job-Shop Scheduling Problem description found at https://en.wikipedia.org/wiki/Job-shop_scheduling.
Last Planner System® (LPS®) is a registered trademark of the Lean Construction Institute (LCI). LPS was initially developed by Gregory Howell and Glenn Ballard. The current Benchmark for LPS can be found at https://p2sl.berkeley.edu/wp-content/uploads/2021/03/Ballard_Tommelein-2021-LPS-Benchmark-2020-2.pdf.
The five steps described in this article apply to the construction of a building. There is a similar five-step strategy for the design of a building. The goal of the design strategy is not speed. The principal value of using a similar strategy for design is a significant reduction of project costs while enhancing the overall benefits of the project.
Summary of the Five Steps
Step 1: Identify Project Phases and Work Streams to Determine Plan Modules. These Plan Modules should be loosely coupled, meaning that the interdependencies between each should be minimized to the greatest extend possible. This allows a complex project to be planned as multiple simpler projects, with the benefit of greater flexibility in addressing project surprises and a clearer focus on rapid completion of the modules.
Step 2: Determine Plan Increments and Release Paces for Each Plan Module. Plan Increments are defined physical locations within the building project. They introduce a measure for establishing predictable workflow, essential to achieving productivity and rapid completion times. By coordinating the scale of Plan Increments with the application of standard Release Paces project leaders have the benefit of being able to better control completion times by determining the start date for the final tasks in a construction phase, without resorting expensive tactics like overtime work and second shifts.
Step 3: Determine the Number of Operation Sets in Each Plan Module. Operation Sets are groups of tasks that can be performed at the same time within the same Plan Increment boundaries. There is a relationship between the composition of tasks within an Operation Set and the size of the Plan Increment.
Step 4: Calculate the Duration of Each Plan Module. The duration is a function of the number of Plan Increments, number of Operation Sets, and the Release Pace of the work required to complete the Plan Module. Smaller Plan Increments allow for a faster Release Pace, which allows the final Operation Set to begin sooner. Project leaders can experiment with these planning elements to optimize overall schedule duration. A faster release pace requires greater performance reliability and is a factor that needs to be part of the planning deliberations.
Step 5: Organize the Flow of Work Between Plan Modules. With the strategy for each of the Plan Modules developed, use a pull planning process to organize the sequence and relationship between the Plan Modules. Some modules may be relatively independent of other work and be able to be performed concurrent with other module. Many modules will need to only be partially complete before subsequent module can begin. The connections between Plan Modules are kept to a minimum. The benefit of this loose coupling of modules is that negative impact of design and supply chain disruptions can be better contained and that module connections can be more easily rearranged to maintain an overall project completion target.
The terms “Plan Modules” and beginning in Step 2 “Plan Increments” used for these elements are adapted from the work of Gene Kim and Steven J. Spear in Wiring the Winning Organization, IT Revolution, 2023. The “Theory of Performance” described by the book helped greatly to codify successful planning practices used by different project teams I observed beginning in 2012.
Step 5: Organize the Flow of Work Between Plan Modules. With the strategy for each of the Plan Modules developed, use a pull planning process to organize the sequence and relationship between the Plan Modules. Some modules may be relatively independent of other work and be able to be performed concurrent with other module. Many modules will need to only be partially complete before subsequent module can begin. The connections between Plan Modules are kept to a minimum. The benefit of this loose coupling of modules is that negative impact of design and supply chain disruptions can be better contained and that module connections can be more easily rearranged to maintain an overall project completion target.
The planning strategy steps summarized above are described in more detail in balance of this article.
Step 1: Identify Project Phases and Work Streams to Determine Plan Modules
Project Phases are sets of similar types of work. Typical examples in construction include Site Preparation, Substructure, Structure, Envelope, Systems Rough-In, Interior Finishes, Site Finishes, Commissioning. Based on the size and complexity of a project some of those typical Phases may be combined, such as combining the Structure and Envelope, or divided, such as splitting Systems Rough-In into Vertical Shaft Rough-In, Overhead Main Rough-In, and Branch Rough-In.
Work streams are sets of sequential tasks that advance each Phase, or sometimes a portion of Phase. As an example of the latter, there may be separate Systems Rough-in Work Streams for a building’s basement, ground floor, upper floors, and mechanical penthouse. Because the intensity and sequence of tasks in each of these four areas is different, each forms a different work stream.
Each Work Stream forms a Plan Module for the purpose of developing the strategy for constructing the building. Before determining the time relationships between the Plan Modules, it is necessary to plan the type and sequence of work in each module.
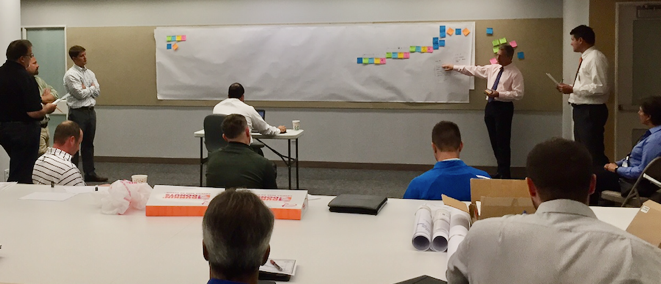
Image 1 – A project team working through steps 1 through 5 during a milestone planning session. The session was supported by the participation of major trade contractors, the construction manager, the architect, consulting engineers, and the project owner.
Step 2: Determine Plan Increments and Release Paces for Each Plan Module
A Plan Increment is a physical part of the building project in which a task is completed before the people performing that task move to the next Plan Increment. A structural steel sequence is a common type of Plan Increment. Because a steel sequence is a function of the building’s structural design opportunities to adjust the size of the sequence can be limited.
There is a large degree of flexibility in determining the size of Plan Increments for building interior work. Plan Increment size if defined by the amount of time pace setting tasks require to complete the work in each increment. An example of a pace setting task for interior finishes work is the installation of drywall. Plan Increments should require no longer than five days for a pace setting task to be completed and can be as small as one day. The number of days required to complete work in a Plan Increment is the Release Pace for that Plan Module.
Determining the size of a Plan Increment is an important element of a project team’s strategy. A one-day Release Pace for a Plan Increment allows the completion of a typical interior finishes set of tasks for a 200,000-sf area 16% faster than a Plan Increment with a Release Pace of five days. The shift is more dramatic for a smaller area of 100,000-sf, with the one-day Release Pace being 25% faster than a five-day Release Pace. Smaller Plan Increments with faster Release Paces also increase the likelihood that two sets of crews can work on different floors concurrently.
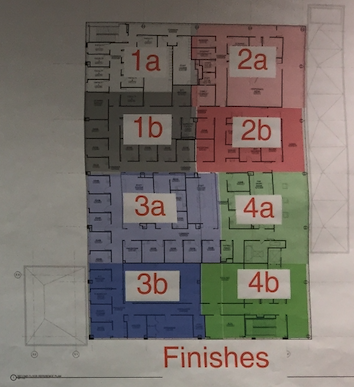
Image 2 - This project identified eight Plan Increments on each floor. The Plan Increments were paired so that it was clear where activities that required a large space would be working.
There is a trade-off in shifting from five-day to one-day Release Paces. The shorter Release Paces require greater precision in daily execution. That is why one-day Release Paces are more easily attained in building types such as dormitories and multi-family apartment compared to building types with a variety of room types and sizes. For this reason, two-day and three-day Release Paces are common.
Even the five-day Release Paces represent a significant time savings compared to typical methods of project scheduling. The above comparisons between a one-day and five-day Release Paces are presented to demonstrate that the strategy a project team selects allows them to manage the amount of time a project requires to be completed.
Some people will recognize the above as describing a form of Takt Planning. Takt is a German word for beat, or rhythm. The terms Plan Increment and Release Pace are used to define the essential concepts for designing a linear work stream, Release Pace being the beat that tasks follow. Note in some cases tasks may need to be in play in more than one Plan Increment at the same time. This is feasible so long as the tasks advance to the next Plan Increment at the same pace as the other tasks preceding and following them.
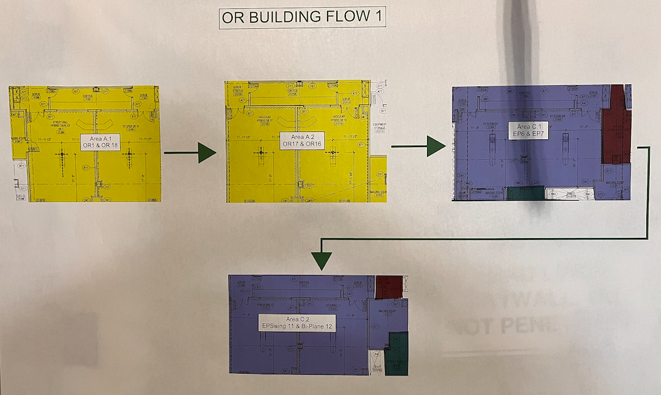
Image 3 - When determining Plan Increments the optimal flow should consider the movement of people and materials on the project.
Step 3: Determine the Number of Operation Sets in Each Plan Module
Operation Sets are groups of tasks that can be completed at the same time within the same Plan Increment area. A Plan Module for interior finishes work may begin with Operation Sets that begin with Drywall Installation, then Taping and end with Final Cleaning. The size of the Plan Increment will impact the number of Operation Sets. For example, taping in a one-day Plan Increment may be four Operation Sets, with a set for each of three coats of taping and sanding. In a five-day Plan Increment, Taping is a single Operation Set.
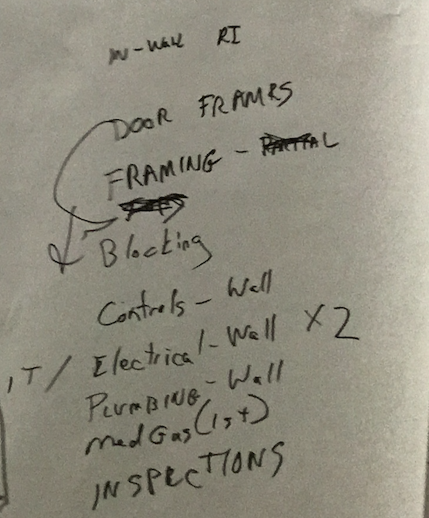
Image 4 - An experienced team can informally identify the Operation Sets for a Plan Module, in this case for an in-wall rough-in module. Note that electrical rough-in was determined to require two Operation Sets.
The number of Operation Sets for an interior finishes Plan Module can range from twenty-three with one-day Plan Increments to fifteen for five-day Plan Increments. Some tasks allow for negotiation between trades and project leaders to determine optimal Operation Set design given schedule targets and production efficiencies. Determining Operation Sets is another opportunity for project teams to select a strategy that allows them to manage the overall duration of the project.
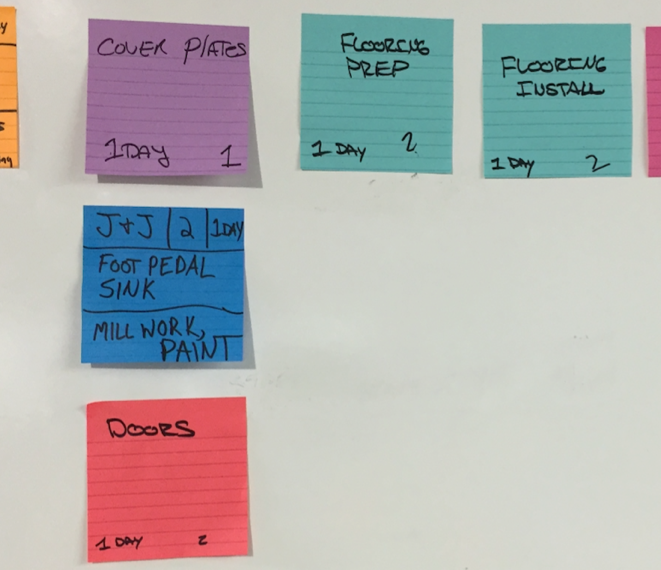
Image 5 - The purple, blue, and red sticky notes represent individual tasks by different specialists that can happen concurrently within the same Plan Increment. Together they comprise an Operation Set.
At an early stage of planning, it is not important to finalize the sequence of Operation Sets. All that is necessary is to have a reasonable estimate of the number of Operation Sets for each Plan Module.
One caveat to keep in mind. Some Plan Modules will not lend themselves to Operation Sets that can be evenly distributed across like Plan Increments. These are usually specialized areas such as mechanical penthouses or food preparation spaces in which it is necessary to vary Plan Increments and Release Paces. Normally these modules require less time to construct than concurrent modules, so a less regular flow of work can be managed to not impact the overall project duration.
Step 4: Calculate the Duration of Each Plan Module
With the number of Plan Increments and Operation Sets determined for all the Plan Modules it is possible to calculate the amount of time required to complete each module.
(Release Pace in Days x Number of Operation Sets) + (Release Pace in Days x Number of Plan Increments) - Release Pace in Days = Duration of Plan Module in Days
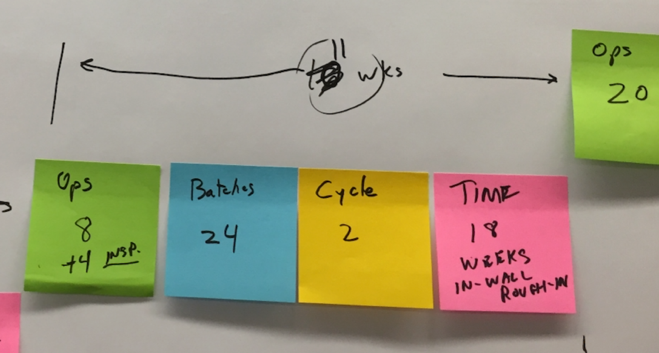
Image 6 - In this early version of the approach Plan Increments were called "Batches" and Release Paces were identified by the pace number of days in a week. The duration in this example is 18 weeks, with the following module starting after week 11.
By controlling for the Release Pace, Number of Operation Sets, and Number of Plan Increments a project team has a large degree of influence over the duration of a project. For Initial Project and Milestone Planning purposes it is reasonable to round the number of days up to determine a weekly duration for the Plan Module.
Step 5: Organize the Flow of Work Between Plan Modules
The primary advantage of organizing the project with Plan Modules is that the modules can be sequenced and arranged with a limited number of predecessor connections, or expressed differently, loosely coupled. Loose connections between Plan Modules have the advantage of allowing project teams to adjust their plan and strategy more easily as unanticipated events that impact one part of the project unfold. In contrast, most traditional project schedules are tightly coupled throughout, and a change anywhere in the project tends to ripple through the network of task connections to appear to impact many future tasks.
Use a pull process to organize the modules. In addition to sequencing the modules the team should identify release points in predecessor modules and connect modules at those release points. For example, if a Systems Rough-In Plan Module has as a final Operation Set In-Wall Inspection, then it is likely that only a certain number of Plan Increments need to be completed before an Interior Finishes Plan Module for the same spaces is able to start.
Once all the Plan Modules have been organized and loosely coupled using a pull process it is possible to calculate the estimated duration of the project.
Using the Strategic Plan During the Project
About two months before the beginning of each Plan Module the project team should replan the work in the module using a pull process. Using the earlier plan for the module as a reference they determine Plan Increments, Release Paces, and Tasks. Using a pull process, they determine which tasks can be part of the same Operation Set and the sequence of the Operation Sets. The objective of the planning session is to complete the Plan Module in less than or equal to the time determined during the initial project planning. Because at this stage greater trade expertise is available identifying ways to reduce the initial planned duration is often observed.
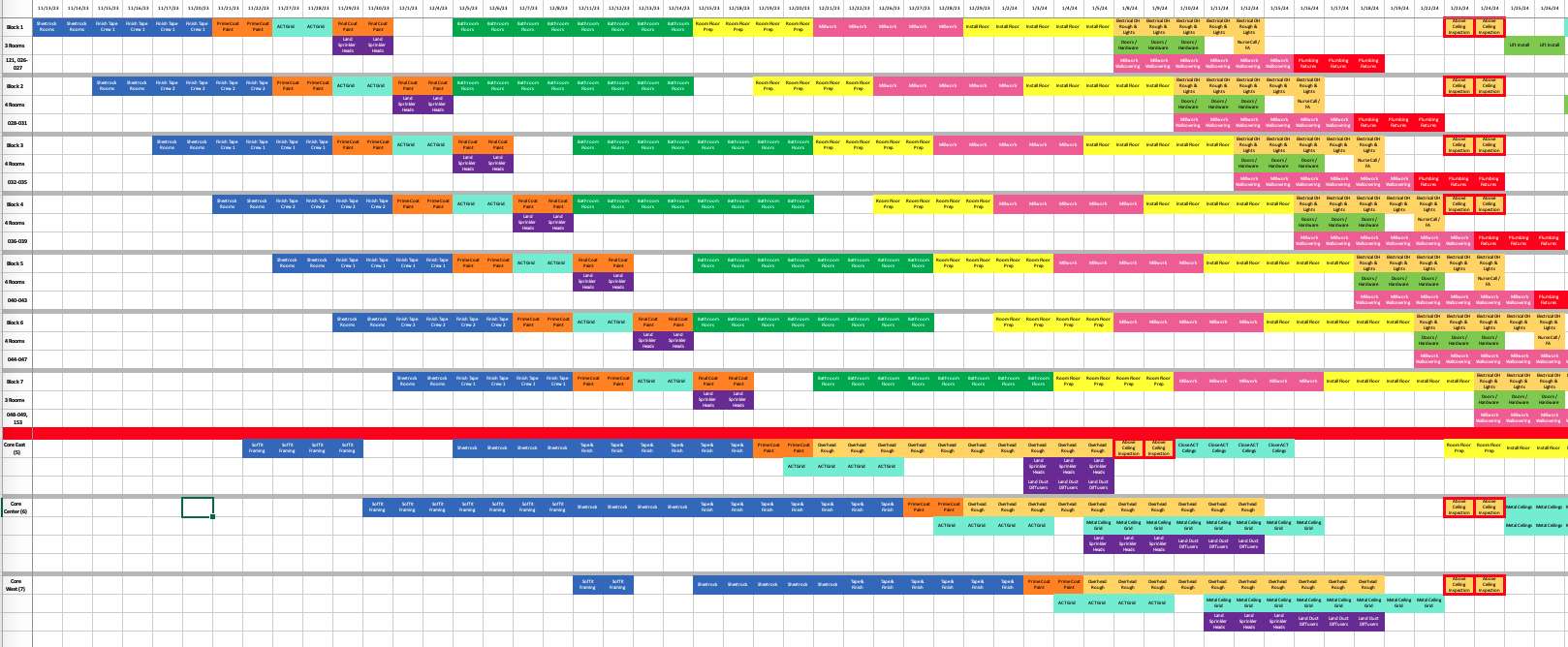
Image 7 - This illustrates the flow of work following a pull planning session for the two finishes modules of a project, the modules separated by a red line. The upper module shows seven Plan Increments of four patient rooms each and the lower module shows three Plan Increments for sections of the floor core services area. Each color represents a trade, some of which have multiple sequential Operation Sets with a two-day Release Pace.
Unplanned events may disrupt a portion of the project, beginning with work in one of the Plan Modules. The response to such events should be to assess how the disruption impacts other modules. Because modules are loosely coupled a shift in how they are organized is one approach to maintaining the overall project duration. Because Plan Increments within a module are well defined another response to some types of disruption, such as a late design change or the late delivery of specialized materials unique to certain Plan Increments, the impacted Plan Increments can be organized as a standalone Plan Module, and loosely coupled to the rest of the project.
Conclusion
The objective of this article is to demonstrate how by taking a strategic approach to planning work project leaders can achieve significant time savings compared to traditionally planned projects. I chose 20% as a benchmark because that is a level of performance that I and colleagues have observed readily achievable. As described in a footnote, one team using a forerunner of this process completed a nineteen-month project in fourteen months, a 24% reduction in time.
As project teams become more skilled with this approach, they should seek to increase time savings on each subsequent project, achieving 30%, 40%, and greater levels as their capabilities grow.