Lean Construction research has been primarily focused on deploying and implementing lean within projects. Although the organizational problem of how to spread, scale, and sustain lean has been recognized to be an important one, few researchers and practitioners have focused on this problem. In this paper, we will explore how AECON, a construction contractor with over 10,000 employees, has been approaching lean since 2021. The goal of this paper is to shed light on how this company has been able to deploy and sustain lean. We will explore the core components of AECON’s Building Smarter Program to highlight their successes, failures, and lessons learned. The goal of this case study is to share one approach to deploying and scaling up lean in a large organization so that other companies can take the findings and test it out themselves.
Since the very beginning of the field of Lean Design and Construction, the community has focused on many different aspects. In the very early days, there was a focus on developing a theoretical foundation for lean construction [1, 3, 7, 8]. Early research focused on developing lean methods such as the Last Planner System to improve percent planned complete and labor productivity [3, 7, 11, 12]. In the 2000s, there was a focus on improving lean design. This includes research on Set Based Design, Choosing by Advantages, Last Planner in Design, Target Value Delivery, and Integrated Project Delivery [2, 5, 9]. The 2010s to 2020s brought more attention to project production planning with renewed interest in operations science, factory physics, and takt [4, 6, 13].
And although organizational deployment has been understood as being as important as project deployment of lean, there rarely has been much research into this important area. There has not been a well-documented case study of an organization with over 10,000 employees deploying lean across the entire company. The goal of this research is to shed light on what a scaled deployment of lean can look like. We want to ask a few fundamental questions: 1) Can an organization with over 10,000 employees deploy lean across the entire company? 2) What would such a program look like? 3) What are some business and human results / KPIs that we can get from such a program? 4) How do we get upper management onboard and involved with such a program? 5) What kind of internal structure / management layer is needed to run and sustain such an effort? 6) Is there a positive ROI associated with such a program?
Research methodology
The research methodology that we are using for this paper is a combination of the case study method and action research (Yin 2018; March and Smith 1995). Case studies are a great way to showcase individual and unique examples. Although there is not as much data to do a statistical analysis, a case study can go deeper and provide valuable insights and inferences that can be applied to other cases (Yin 2018). Case studies give rich qualitative data, allow for theory building, and provide and roadmap for future studies and replication.
This case study is part of an action research project. In action research, the authors are participants of the study, and they actively drive the experiment. Rather than being an independent observer, the authors are working with the team throughout the project in order to test and validate new ideas (Yin 2018). With action research, there may be some biases from the researchers as well as inherent experience from the researchers which can be a barrier for replication. We will do our best to explain the organizational structure and processes that were applied in a way that the reader can understand and point out any potential biases along the way.
Since this is a new area of research where there are not many examples available, we will be presenting one case study. Our hope is that other researchers and industry practitioners will take this example as a reference point for replicating it themselves. We hope that over time we will have more case studies and examples of companywide lean deployment to develop a more comprehensive framework. For now, we will share one case study and develop a preliminary framework for how lean can be deployed within a large organization.
Organizational deployment of lean
The Organization’s Story
AECON Construction Group, Inc. began its journey to be the #1 Infrastructure Company in 1877, and has accomplished projects such as the CN Tower (Toronto, ON), Gordie Howe International Bridge spanning Detroit MI to Windsor, ON, and is currently one of the first builders to construct the world's first Small Modular Reactors for Ontario Power in Clarington, ON, on the North shore of Lake Ontario. As a publicly traded company, Aecon business model focuses on Civil, Nuclear, Industrial, Utilities, and Light-rail Transit with a revenue of over $4B, and an employee makeup approximately 2,500 salaried and 10,00 hourly staff. Over the last hundred years, there have been some notable eras that have made AECON what it is today including an entrepreneurial approach prior to 2005, five years later evolving to a “One AECON” approach to better integrate across the organization, later scaling our project portfolio by executing mega projects in 2015, then focusing on “building resiliency” in 2020, and now focusing on strengthening the company’s core to thrive for another hundred years.
In 2021, AECON’s Operational Excellence program was officially formed and wholly integrated into the AECON Strategic Plan as a requirement for all employees to live by. Early efforts were focused on improving how construction projects were executed, but quickly grew to also focus on how every employee performs their functional roles within the organization, both project-related as well as back-of-house departments to run the business. Lead by the current President and CEO Jean-Louis Servranckx, a Continuous Improvement culture was the core element of the strategic approach, and since 2022 the program has evolved into AECON’s “Building Smarter” program that utilizes Lean Construction practices as a method to enhance how AECON competes in the market and drives value for clients, stakeholders, and employees.
Aecon’s building smarter program
Three pillars make up AECON’s core organizational Strategic Plan, KF1:Outstanding Teams, KF2: Execution Excellence, KF3: Risk vs. Opportunity Balance. Although all three KFs have direct linkage, for the purpose of this paper we are only going to focus on KF2.
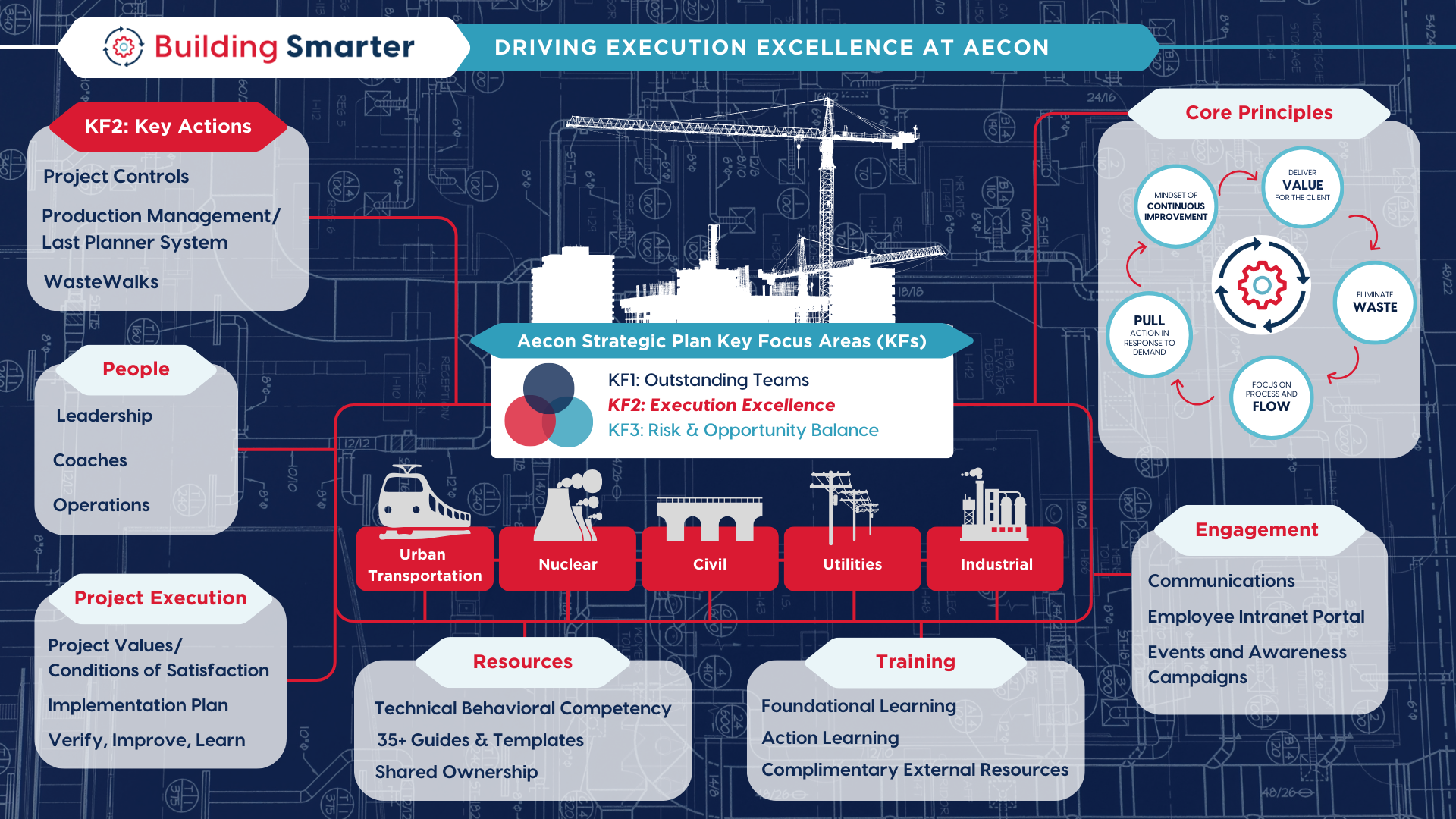
Figure 1: Aecon’s Building Smarter Program
KF2 is heavily based on Lean Construction practices, discipline to drive value through reliable and consistent project controls, and continuous performance improvement. Highlights include:
- Lean Construction – Utilize lean practices and thinking to guide production management throughout the entire project lifecycle.
- Quick, Reliable & Consistent Project Controls – Enable outstanding teams by utilizing clearly defined controls that are easily deployable, repeatable, and provide continuous project visibility to key benchmarks over the entire project lifecycle.
- Capitalize On Lessons Learned – Formally capitalize on experience and lessons learned across all projects by developing new systems or processes that drive opportunities for improvement, leverage organizational differentiators, and introduce economies of scale.
Strategic Plan
Early program efforts started with a focus to enable high-performing project execution by utilizing the Last Planner System and Lean Construction practices, a general and less prescriptive approach to continuous improvement, and an enhanced focus on enabling high-performing teams. Within the second year of program implementation, it became apparent that the organization was ready for additional rigor and an increased integration of how our teams approached production management and project controls.
Project Controls – Although there are some different client requirements, level of project detail, and other considerations such as staff capacity and capability across each sector, significant work has reshaped how our project controls are implemented, managed, and tied into the Building Smarter program. As project controls are a fundamental project management component, it was essential to link program efforts to what teams were already doing on projects.
Production Management & LPS – Prior to AECON’s Building Smarter program, there were no projects that utilized LPS or other lean construction methods. Today, nearly every major project is utilizing LPS and other productivity benchmarking techniques. The goal is to implement a production planning system that produces predictable workflow and rapid learning throughout the project lifecycle and improves execution reliability.
WasteWalks – AECON utilizes what we call “WasteWalks,” otherwise known as Gemba Walks in the industry, to increase value for our teams and clients by focusing on eliminating waste through all phases of project execution and within the business. Every project and site location is required to conduct a WasteWalk once a week and report their progress and actions to reduce waste. To an organization of new lean learners, utilizing WasteWalks has had one of the greatest impacts to the program results as a mechanism to improve work for our people, foster lean thinking, and directly demonstrate value to our customers and stakeholders.
Sector Integration
Five different but complimentary industry types make up the primary project portfolio (Nuclear, Utilities, Civil, Industrial, Urban Transportations Services). From scale to complexity, to other industry-specific nuances, each sector has specific core strengths, challenges, and business needs that required minor modifications to applying AECON’s Building Smarter Program. Some examples include the complexity of managing project and production controls on a Nuclear build, logistics of building pipelines over mountain ranges with thousands of remote staff, designing and building mega projects with countless partners and thousands of people.
From the beginning, it was essential that each sector create and manage to a sector-specific plan based on a standard AECON template including multi-year goals, strategies, and tactics. Each sector plan was developed with and is continually supported by program lead to ensure alignment with the corporate plan and utilizes other sector progress to accelerate and compliment similar efforts.
Functional Departments
It is essential to align annual planning efforts with critical departments such as Human Resources to connect efforts with how the business is managed functionally. Although early efforts typically start at the workforce and recognizing that the value stream doesn’t stop at the project gate, departments within the organization heavily influence project and organizational waste, and should be part of the near-term improvement plan when capacity and benefit allow.
Human Resources – Instituting and sustaining essential learning content ensures employees have necessary understanding to perform practical application of lean methods and thinking. Beyond coordinating learning resources and training, developing an employee Job Profile for staff dedicated to Continuous Improvement was essential to identify technical and behavioral competencies for new learners, CI coordinators, managers and directors. This has been essential to developing and recruiting staff to ensure employees have the right skillsets and experience to support work and understand progression.
CI Communications – As one of the biggest lessons learned with lean program implementation, corporate-level communications provided some of the most impactful outputs to make the program what it is today and helped accelerate the majority of organizational results. From branding and visual media, to company-wide correspondence, awareness campaigns and events, to peer-to-peer sharing of lean implementation, the Building Smarter Communications Plan was the strategic and tactical action plan that identified messaging, accountability and implementation targets, to enabled project results utilizing a stakeholder focused approach.
Safety – Integration with the organizational safety department has been a significant driver to implementing our Building Smarter program and has a direct correlation to improving safety metrics by enhancing our operational production management techniques, performing and supporting continuous improvement, and providing tangible application methods to improve our safety metrics on each project and business sector.
Business Process Management Office – Tasked with managing any and all software and systems within the organization, including what is used on projects, working with this team was essential. Organizational software and process can be a barrier, or an enabler, for how employees participate and perform work to support AECON’s Building Smarter approach. An example of one challenge was enabling kiosk computers to run digital application of the Last Planner System in a way that enabled project-wide participation by all stakeholders beyond only AECON employees.
Legal – Although not initially approached as an essential component to program success, it was quickly learned how essential the legal department was with ensuing our project approach for all contract types included the considerations of lean thinking, ranging from subcontract exhibit language that included implementation requirements for methods such as LPS, 5S, Continuous Improvement, or instituting healthy project alignment with chartering and Conditions of Satisfaction.
People
Executives and Sector Leadership – Executives and sector leadership represent approximately 1% of the organization. As an initial effort by the AECON CEO, the commitment and participation by executives and business unit leadership was essential to program success. Starting with the planning, course setting, and identification of key participants, a revolution of promoters and early adopters quickly extinguished any detractors and laggards within the organization. Initial training requirements were kept at a conceptual level and specific action plans were created to fill competency gaps over time. One of the first actions by the CEO was to hire a competent and experienced program director as well as provide capital investment to enable a sustainable and results driven program.
Program Director – Initially with minimal practical application and competency across the organization, hiring an individual to not only run a program, but also with the technical and behavioral competency was an essential first step. Reporting directly to the CEO, the program director was given a high level of autonomy to work with each business unit to guide and develop sector-specific implementation plans. Additionally, the director supported strategic planning and execution, development of internal infrastructure and standard operating procedures, company-wide CI recruiting and career development, discrete project support, and helped set the tone for cultural evolution.
CI Communications Lead – While during the first 6-8 months of program efforts provided few examples of lean implementation across the organization, one of the most impactful program components steamed from hiring a dedicated CI communications manager. Early activities include the development of a CI Communications Plan, which quickly took shape into the core of all program planning. Within 3-6 months of dedicated communications support, employee perception, participation, and operational results drastically improved.
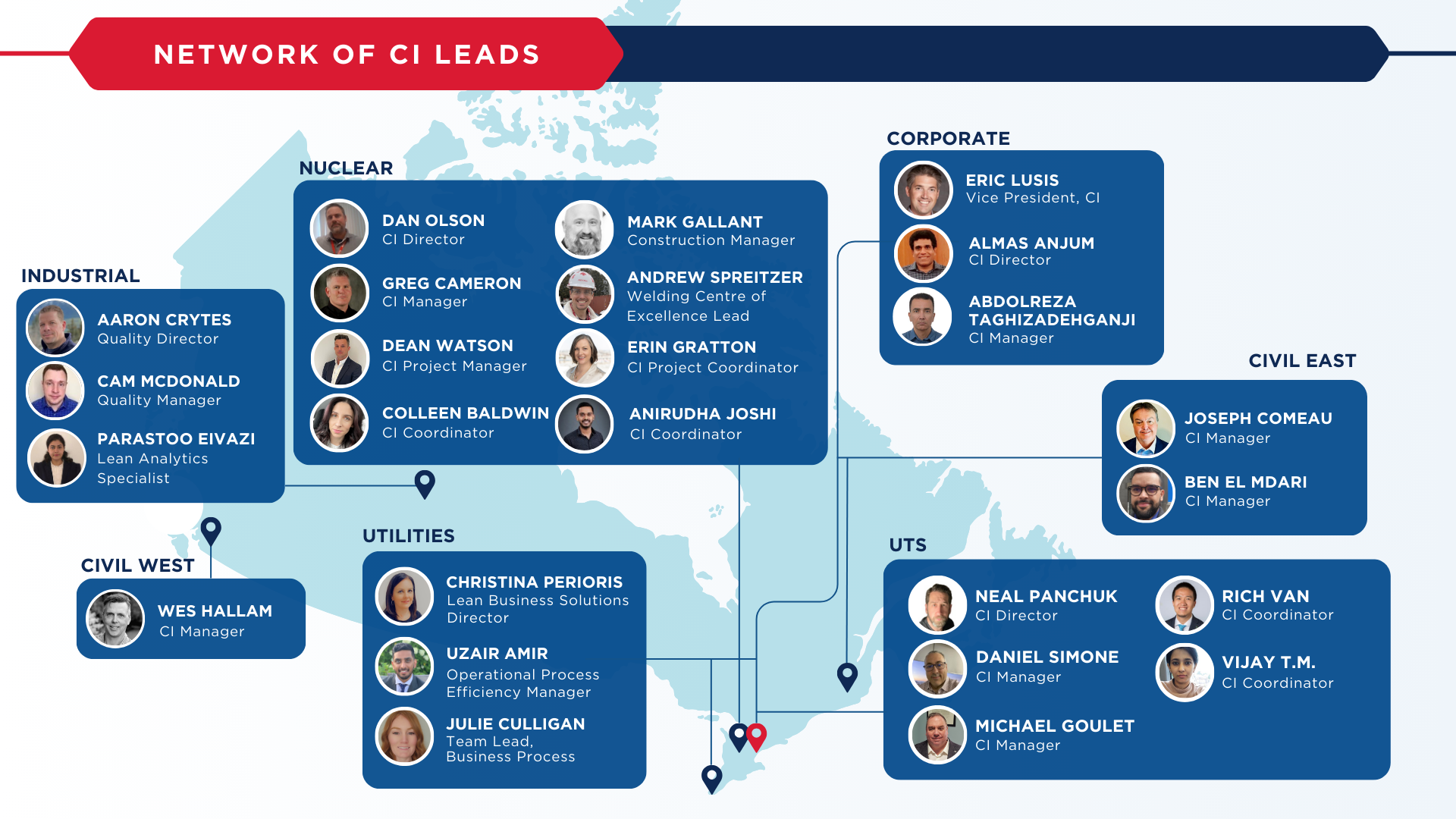
Figure 2: Continuous Improvement Leads in each Sector
Continuous Improvement Coaches – Since 2021, AECON’s full-time CI staff has grown over 700% due to the commitment by leadership and proven results from our continued investment. As lean thinking was initially new to over 90% of all employees, developing coaches in every business unit was an essential component to guide, mentor, support staff and project stakeholders while executing sector-specific efforts. Currently there are over 30 full-time equivalents across the organization and every new project has been an opportunity to expand the team of lean practitioners and grow adoption across the organization.
Operations Staff – Project leaders represent approximately 10% of the organization and have a direct influence to peers, clients, and frontline crews. As on-site leaders, they are primarily accountable to project-level KPIs, require in-depth understanding of lean methodology and program efforts to be successful, and enable project participants and stakeholders. Frontline staff represent almost 90% of AECON’s employee makeup, primarily unionized, and are typically the people who create project value.
Engagement
After clarity, focus, and discipline, engagement is not only an indicator of program success, but it should also be targeted differently for each organizational stakeholder.
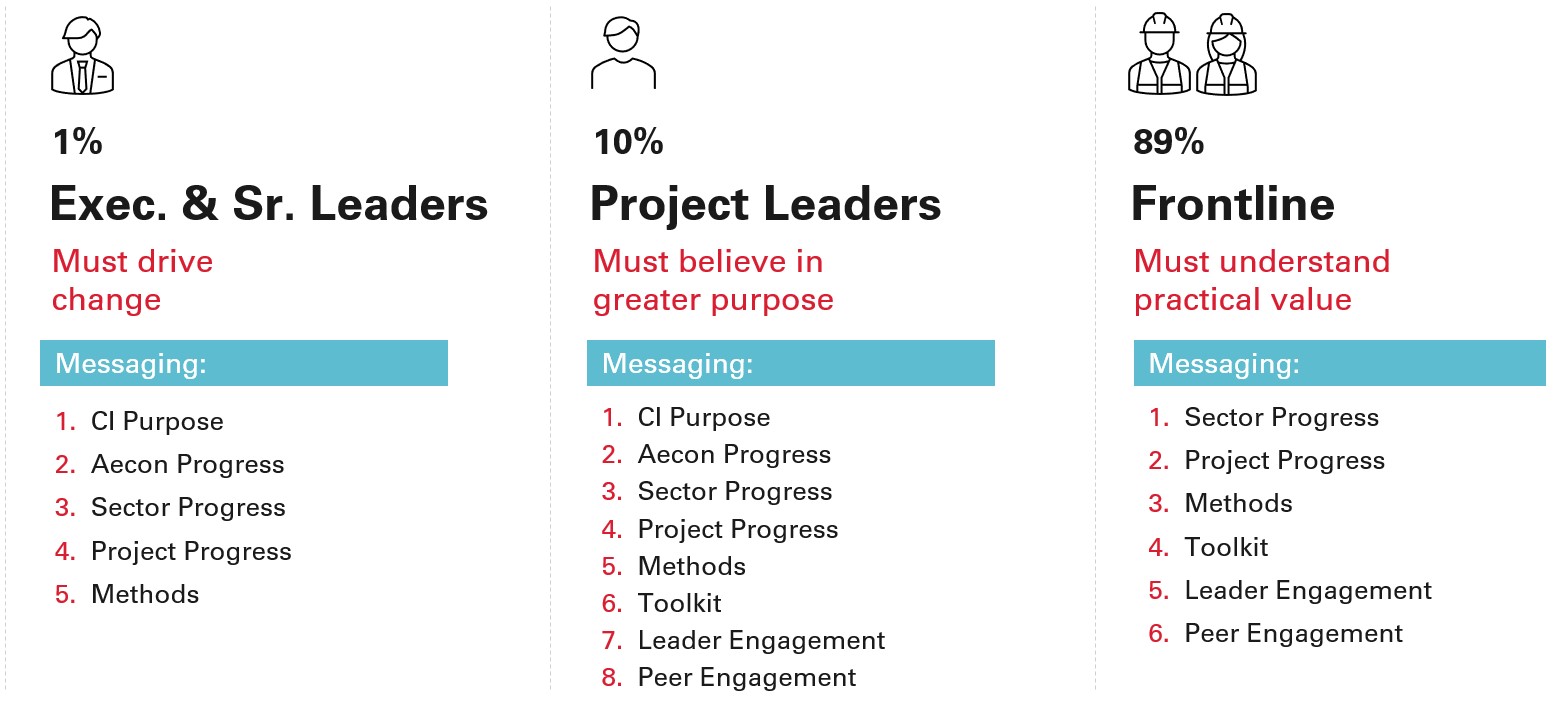
Figure 3: Stakeholder Engagement
Multiple systems were used to enable current results within Aecon including some of the following examples:
1. CI Communications Plan – After developing a six-year programmatic strategic plan, a Communications Plan geared specifically towards program efforts was one of the most impactful actions to date and was the key change management leaver.
2. Intranet – Providing an attractive and easy to use visual interface for employees to connect to resources, learn, and share with community, is one of the easiest ways to foster adoption, stimulate engagement and provide transparent program visibility to vision, actions, and results. The Building Smarter intranet SharePoint is the one place an employee can find what’s needed to fast-launch their career and approach to performing work both in the field and office.
3. Events – Annual event examples include: Quality Week to focus our people on building right the first time, Operational Excellence Team Summit to share best practices and lessons learned, Project Controls Summit to deliberately focus on cost and schedule management. Each event is tailored to a specific audience, supports the organizational strategy and roadmap, provides an opportunity for functional leaders to participate and develop, and solidifies a common language and approach to work across the organization. One of the most impactful events is the WasteWalk Challenge to practice CI.
4. WasteWalk Challenge – Although waste reduction is practiced throughout the year, the company-wide WasteWalk Challenge is when each sector and employee has two weeks to identify waste in the work around them. Beyond tracking observations, waste type, value, and status, sectors are greatly evaluated by quantity of participating projects or yards, unique facilitators, and new facilitators. A real-time company-wide dashboard is posted to the intranet for all to see improvements.
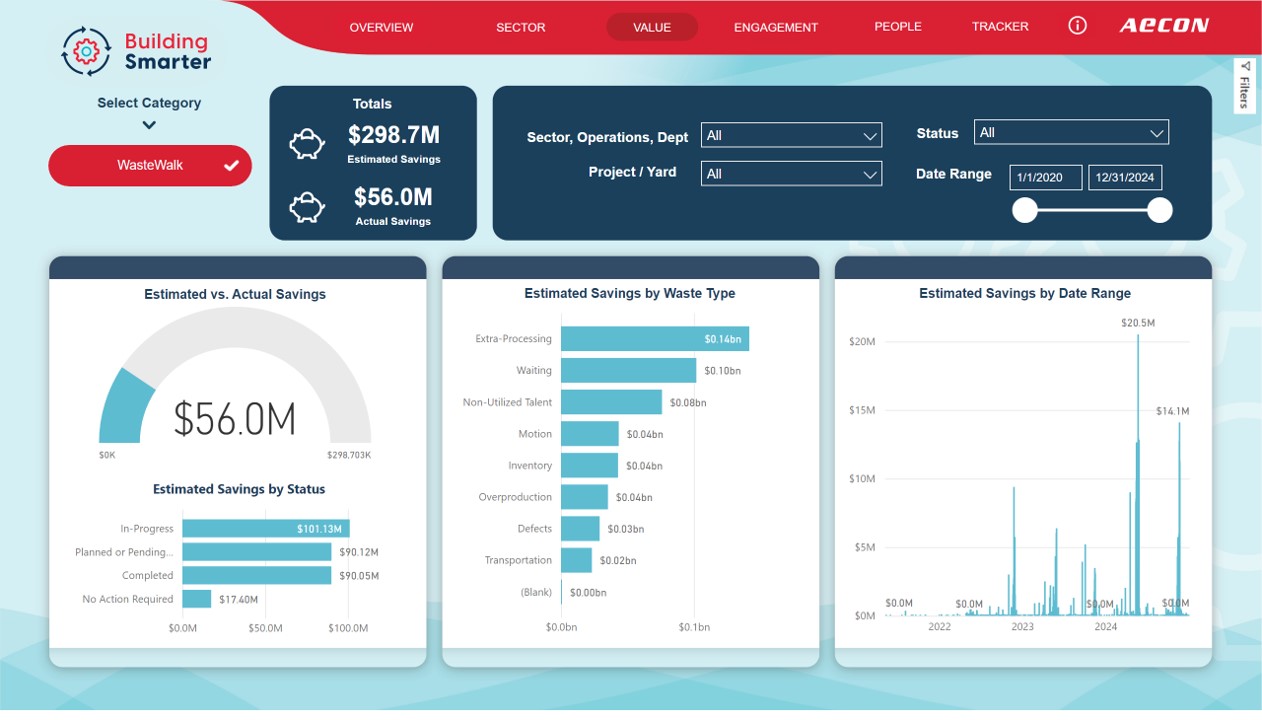
Figure 4: Wastewalks Dashboard
Learning Materials and Resources
For any program, it is essential to have developmental targets, standardized materials used with training and implementation, and an organizational structure that fosters shared ownership to both align on what is needed and share with the workload. At an organizational level, some critical elements should be considered to drive results, including:
Technical/Behavioral Competency – For any role, particularly a new career path for lean practitioners, without defined expectations and written roles and responsibilities, its pretty hard to expect accountability and drive results. Early efforts included ensuring we had clear role definition, purpose, and expectations to support internal development, recruitment, and program expansion.
Guides/Templates/Learning Materials – Guided by the initial six-year program implementation plan, guides and templates for anything used were developed to support gradual adoption. Making new methods easy for employees to access and utilize reduces barrier for adoption and ensures work standards and current onboarding is utilized.
Training and Development
One of AECON’s “secret sauce” program element which is heavily utilized by our project teams, including our non-AECON stakeholders on Joint Ventures, is our employee development resource catalogue. We have found that teams will need training and support in three specific areas: leadership development, training in lean methods and tools, and continuous improvement and retrospective techniques.
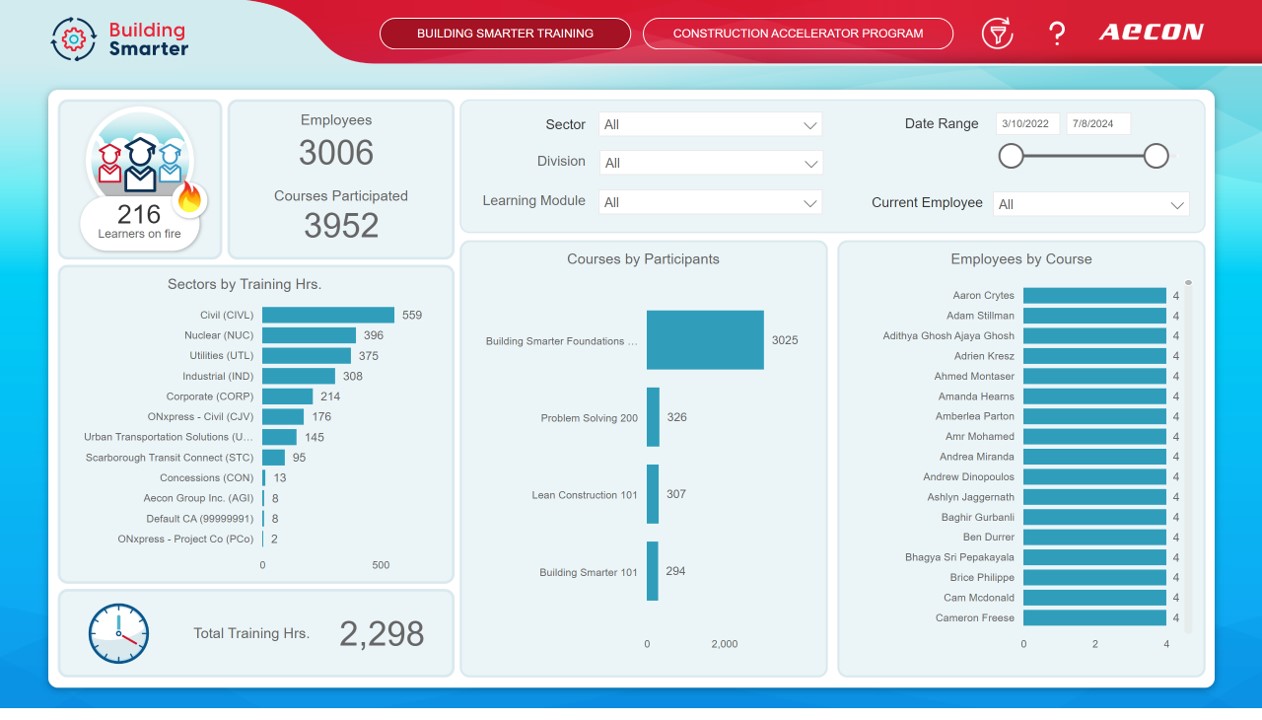
Figure 5: Training Dashboard
Foundational Training – Our employee onboarding begins with developing a common language, starting with the lowest level of common foundational understanding to set the stage for accelerated adoption and practical use. Beyond every employee experiencing the same common level of understanding and basic lean methods, the approach to training is primarily based on accountability level, implementation needs, personal development, and organizational competency requirements.
- Building Smarter 100 – High-level, Five Principles
- Building Smarter 101 – Mid-level, Five Principles, lean methods introduction
- Problem Solving 200 – Mid-level, continuous improvement, problem solving
- Lean Construction 101 – Mid-level, Lean project methods introduction
Complimentary External Training – We also utilize external enterprise-wide learning mechanisms such as Construction Accelerator from the Realignment Group and the Shingo Institute. Other key industry-leading resources such as the Lean Construction Institute, the Lean Construction Blog, and annually hundreds of essential books provided free to our people have had a dramatic impact on how people work on our projects and within the organization. To date, over 3,000 employees have participated 3,948 courses, aggregating thousands of training hours.
RESULTS
WasteWalk Observations have led to the identification of over $300MM worth of estimated and $52MM of actual net cost savings/added value on over 300 projects and yards. 2024 saw the highest employee engagement in WasteWalks since introducing them as a Building Smarter best practice in 2022 with FY24 results including:
- $190 million worth of estimated value from waste reduction efforts identified
- Over $25 million worth of actualized savings from waste reduction efforts
- 1,674 employee observations of Waste, 544 of which were performed by new first-time facilitators
Thanks to our vast and growing data of nearly 3,000 unique Wastewalk observations, AECON can say that Extra-Processing is our most common type of waste amounting to 29%, followed by Waiting at 21% and Inventory at 12%, with the remainder of waste totaling 38%. The total observations have been created by almost 1,000 unique Facilitators, on hundreds of projects. Training & Development (as of November 2024):
- Total to date, 3000+ employees have completed at least one Building Smarter core training session
- Total to date, 5,000+ courses participated
- In FY 2024, 880+ AECONers participated in over 724 Building Smarter Training Hours
Conclusions
AECON has made significant strides in deploying and sustaining lean practices through its comprehensive initiative known as Building Smarter which has enhanced our project execution capabilities, leading to better schedule performance, increased productivity, and more efficient operations. This program is designed to enhance the company's focus on driving value for our clients and stakeholders while also ensuring our employees are the best at what they do.
The company has experienced both successes and challenges in its lean journey. The successes include improved project execution capabilities, enhanced safety performance, and the development of thousands of employees. Lessons learned from AECON's experience include the importance of leadership commitment, the need for clear communication and collaboration across departments, and the value of continuous learning and adaptation. AECON’s Building Smarter program has a long road ahead as we continue to work towards developing thousands of employees with still little to no experience, continue to make lean thinking part of daily work, and as we do our part to proliferate Lean Construction across the industry we serve.
We hope that this case study provides inspiration and a roadmap for other large scale construction organizations to build and develop their own scaled up implementation of Lean Construction.
References
1. Alarcon, L. (Ed.). (1997). Lean Construction. Taylor & Francis. https://doi.org/10.1201/9781482287356
2. Arroyo, P., Ballard, G., & Tommelein, I. D. (2009). Making design decisions using choosing by advantages. Proceedings of the 17th Annual Conference of the International Group for Lean Construction (IGLC-17), Taipei, Taiwan, 501-510. https://iglc.net/papers/Details/663
3. Ballard, G. and Howell, G. (1997) Shielding production: an essential step in production control, Technical Report No. 97-1, Construction Engineering and Management Program, Department of Civil and Environmental Engineering, University of California, Berkeley. 15p.
4. Dlouhy, J., Binninger, M., Oprach, S., & Haghsheno, S. (2016). Three-level method of takt planning and takt control – A new approach for designing production systems in construction. In Proc. 24th Ann. Conf. Int. Group for Lean Constr. (pp. 13-22). iglc.net/Papers/Details/1350
5. Do, D., Chen, C., Ballard, G., & Tommelein, I. D. (2014). Target Value Design as a Method for Controlling Project Cost Overruns. Lean Construction Journal, 171-179. https://iglc.net/Papers/Details/1065
6. Frandson, A., Berghede, K., & Tommelein, I. D. (2013). Takt time planning for construction of exterior cladding. In Proc. 21. https://iglc.net/Papers/Details/902
7. Howell, G., Laufer, A., & Ballard, G. (1993). Interaction between subcycles: One key to improved methods. Journal of Construction Engineering and Management, 119(4), 714–728. doi.org/10.1061/(ASCE)0733-9364(1993)119:4(714)
8. Koskela, L. Application of the New Production Philosophy to Construction. Technical Report no. 72. Center for Integrated Facilities Engineering. Stanford University, 1992.
9. Matthews, O., & Howell, G. A. (2005). Integrated project delivery an example of relational contracting. Lean Construction Journal, 2(1), 46-61. https://leanconstruction.org/wp-content/uploads/2022/08/LCJ_05_003.pdf
10. March, S. T., & Smith, G. F. (1995). Design and natural science research on information technology. Decision Support Systems, 15(4), 251–266. doi.org/10.1016/0167-9236(94)00041-2
11. Tommelein, I. D., & Ballard, G. (1997). Coordinating specialists. University of California, Berkeley. p2sl.berkeley.edu/wp-content/uploads/2016/03/Tommelein_Ballard-1997-Coordinating-Specialists-CoordSpecTR97-8.pdf
12. Tommelein, I. D., Riley, D., & Howell, G. A. (1999). Parade game: Impact of work flow variability on trade performance. Journal of Construction Engineering and Management, 125(5), 304–310. doi.org/10.1061/(ASCE)0733-9364(1999)125:5(304)
13. Tommelein, I. D, & Lerche, J. (2023). Comparison of takt planning methods used on projects of different types. In Proc. 31st Ann. Conf. Int. Group for Lean Constr. (pp. 1605-1616). doi.org/10.24928/2023/0255
14. Yin, R. K. (2018). Case study research and applications (Vol. 6). Thousand Oaks, California: Sage.