Design and construction organisations are constantly looking for ways to improve their design processes, and the ability to deliver consistently and consistently high-quality design is vital to customer satisfaction. This blog post discusses key findings on the impact of batch size, throughput time, and reliability on the stability of the design process. The stability of the design process refers to the performance and predictability of the design workflow (Tribelsky and Sacks, 2011). It involves minimising variability, ensuring reliable throughput, and maintaining high-quality output.
Batch size plays a key role in the lean design process, as smaller batch sizes reduce throughput times, improve responsiveness, and improve resource utilisation (Hopp and Spearman, 2011). When design tasks are handled in smaller batches, teams can address problems quickly, identify errors early, and make changes more efficiently. This approach improves agility and responsiveness and contributes to the overall stability of the process. Above all, the benefits of small batch sizes are evident in the fact that mistakes are learned and recovered more quickly than by designing and delivering plans in large batches.
Throughput time, the time from the start of a design project or design task to its completion, is a critical factor affecting the stability of the design process. Long throughput times cause delays, communication difficulties, and scheduling problems ((Khan and Tzortzopoulos, 2014), while optimising the design process to reduce throughput times improves design process stability, efficiency, and resource allocation.
A key element of the reliability of the lean design process is the use of the Last Planner System™, which aims to improve the reliability of the promises associated with design tasks and is measured by the planned percentage completed (PPC) metric. The results of a study by Lappalainen et al. (2021) on the structural design of a Finnish infrastructure project indicate that design teams (teams E and F) differed from other design teams in having higher PPCs (71.2% and 71.3%) and significantly different faster design task throughput times (see Figure 1). Similarly, design teams C and D, with the lowest PPC (52.2% and 51.9%), also had the longest design task throughput times.
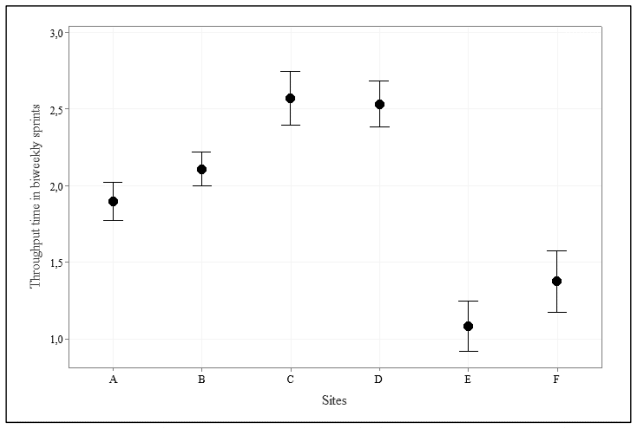
Figure 1. Analysis of variance, interval plot of TT in years 1 and 2 (Lappalainen et al., 2021).
Even though the research is limited at this stage, organisations can adopt several practical strategies to promote the stability of the design process based on the results of it and learn from similar results from many other fields.
First, adopt smaller batch sizes: Evaluate the design process and identify opportunities to reduce batch sizes. Implement agile principles (e.g., Scrum, LPS, and other parts of lean design management) and break projects into manageable tasks to improve responsiveness and minimise errors.
Second, optimise throughput time: Identify bottlenecks and streamline the design workflow to reduce throughput time. For this, there are good collaboration tools that can be used to digitize the monitoring and collaboration of tasks and related communication and make them open to the entire design team and stakeholders.
Third, focus on reliability: Standardise the measurement of the design process and implement quality control mechanisms to monitor and control the design process. Despite its iterative nature, the design process doesn’t have to be chaotic, but neither does it have to be puritanism Taylorism: involve the design team in measuring the design process and its benefits at the group and individual level.
Fourth: Promote a culture of continuous improvement: Take advantage of the quick learning from mistakes enabled by small batch sizes. Create a learning environment in the design process where your teams can collaborate, experiment, and develop the design process. At the same time, involve the customer and stakeholders in giving rapid feedback due to the small batch size.
Design process stability is crucial for design and construction organisations aiming to thrive in today’s competition. Understanding the influence of factors such as batch size, throughput time, and reliability enables the enhancement of design processes, so why not give it a try? There are many professionals and researchers who help you streamline your own process for the development of lean design processes, which you can find through international lean construction associations.
References
[1] BHopp, W.J., & Spearman, M.L. (2011). Factory Physics. Waveland Press, Long Grove, Illinois, USA, 268-271.
[2] Khan, S., & Tzortzopoulos, P. (2014). Effects of the interactions between LPS and BIM on workflow in two building design projects. In Proceedings of the 22nd Annual Conference of the International Group for Lean Construction. Oslo, Norway, June 25-27, 933-944.
[3] Lappalainen, E. , Uusitalo, P. , Seppänen, O., & Peltokorpi, A. (2021). Design Process Stability: Observations of Batch Size, Throughput Time and Reliability in Design. In Proceedings of the 29th Annual Conference of the International Group for Lean Construction. Lima, Peru, July 14-16, 605-612.
[4] Tribelsky, E., & Sacks, R. (2011). An empirical study of information flows in multidisciplinary civil engineering design teams using lean measures. Architectural Engineering and Design Management, 7(2), 85-101.