Coordination issues on a construction site can spread like wildfire. This comes as no surprise to anyone. Why? There are so many moving parts (and so many parts that stop moving) in any one given day/hour/minute during the life of any job. And the moment something stops flowing, everything starts to back up and site supervision is inevitably caught up in what we call the No Flow Circle! For those of you who may not know, the No Flow Circle is the inevitable outcome that will always result when production is not balanced and the driving focus for any job relies more on schedule dates than production rates.
It looks something like this…
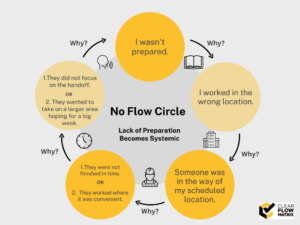
In this kind of a mindset, frustrations build and create more inefficiencies that inevitably serve to disrupt the trade partner’s planning and the lack of preparation becomes a systemic roadblock to progress. Communication breaks down as trade partners only focus on staying one step ahead of the next trade, delivery, or RFI – providing yet another excuse for why time keeps slipping away.
Breaking the No Flow Circle - Flow Is Your Foundation
Most any superintendent’s natural response to this level of discord is a knee-jerk reaction that prompts him to head straight for the middle of the circle, in a desperate attempt to deal with the excuses coming from all teams (in all directions) succinctly and simultaneously. Logically, it seems like an obvious solution – to label himself as the “go to guy” and help get things sorted more efficiently. However, he is soon overwhelmed, and the circle continues. And what’s worse? The superintendent in this scenario actually becomes the bottleneck!
In the Goal by Eliyahu Goldratt, the Theory of Constraints is exemplified by Herbie – an enthusiastic Boy Scout troop member who overpacks his backpack and slows down the rest of the hikers, thus becoming the bottleneck. As part of the solution, Herbie redistributes the contents of his pack and not only keeps up but intentionally sets the pace for the rest of the troop. So, once the problem, Herbie now becomes the solution!
Herbie becomes the Solution!
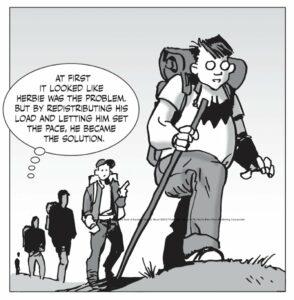
Photo Citation: The Goal: A Business Graphic Novel 2017 Goldratt, Ltd. And The North River Press Publishing Corporation
What’s the takeaway here? Only when all trade partners assume their roles and responsibilities can production be balanced through efficient trade handoffs that maintain and establish the balanced production front.
Sustaining Balance - The Production Front Is the Path
The balanced production front highlighted in a takt production matrix like the Clear Flow Matrix (shown below) focuses on balancing process flow and area handoffs with operations flow and trade production. Or, put more simply, it facilitates (and sustains) a steady flow driven by production rates versus schedule dates.
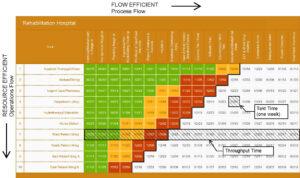
Focusing On Flow - Balance Is Key
Methods such as Pull Planning and Last Planner System (LPS) are essential to improving overall communication and collaboration – both of which are required for keeping the No Flow Circle at bay. Tasks communicated effectively during the Weekly Work Planning phase will then allow teams to agree on activities and commit to meet the pace for weekly handoffs. Within the framework of CFMx, these commitments are optimized sustainably and automatically, ensuring the project continues to flow and bottlenecks are avoided.
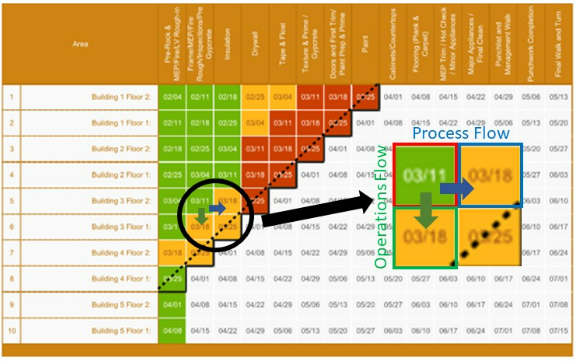
To optimize flow and keep the jobsite going, each handoff must be identified, exploited, and subordinated or they will each become a bottleneck of their own (as demonstrated above).
Shingo and SMET - Handoffs Get Optimized
As a means of maintaining a balanced flow, Shingo developed Single Motion Exchange of Dies (SMED) to avoid the tendency to use overproduction as a means of hiding bottlenecks that resulted from inefficient handoffs. Based on this concept, Single Motion Exchange of Trades (SMET) was developed as a tool for project teams (and especially trade partners) to identify and focus on the handoff process.
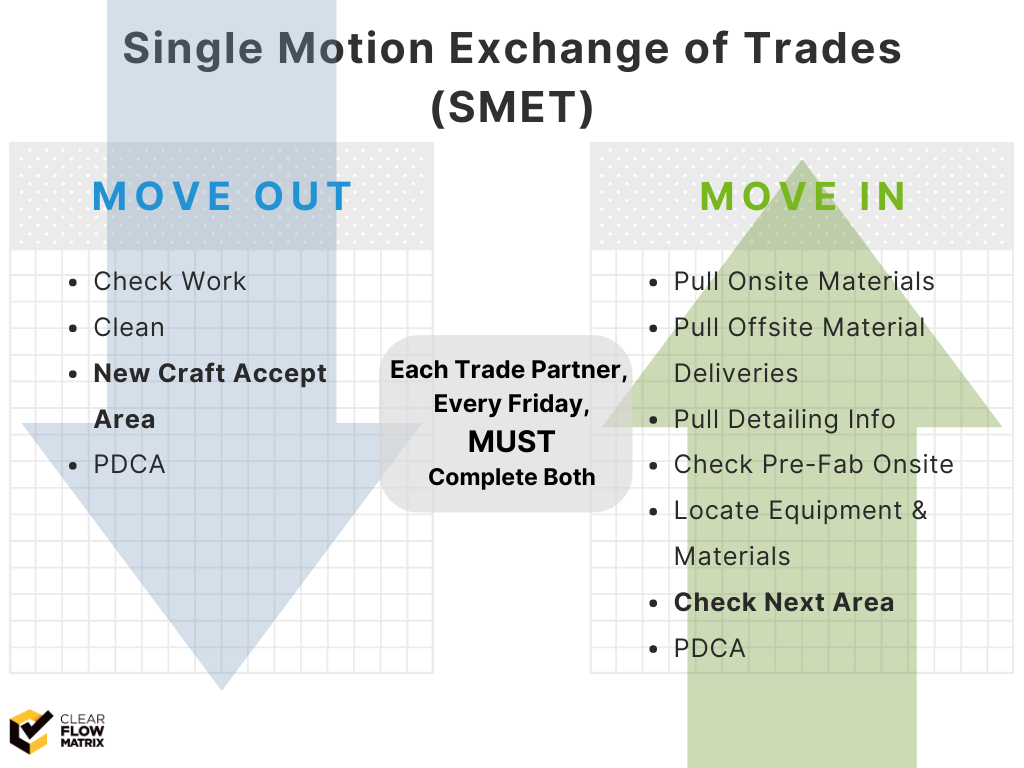
Using SMET, the handoffs are identified early along the balanced production front and confusion is minimized. Materials can be more easily obtained, and equipment is scheduled to ensure nothing is held up by looking for or ordering materials at the last minute.
And all of this facilitates a level of efficiency that maximizes flow, ensures accountability and simplifies communication, keeping the No Flow Circle exactly where it needs to be – in the past!
So, why isn’t this the dominant experience at jobsites everywhere? Or, in other words, why are we still bottlenecking our flow?
Human Tendency - Direct Work’s Greatest Adversary
In a word (or two): Human tendency. Since the 1980’s we have depended on subcontractors to focus on cost efficiency and used CPM methods to manage specific deadlines we think will maintain project schedules. Both methods completely ignore project flow. The level of disruption has become systemic to the point that trade partners defend their approach and do not trust balanced flow or balanced production. And this is a real problem because of what it has done to our direct work ratios!
After decades struggling with the No Flow Circle, the percentage of direct work on construction sites has decreased from 50% in the 1970’s, to less than 40% currently. And it goes without saying (but we’ll say it anyways) that direct work is quite literally what gets the job done.
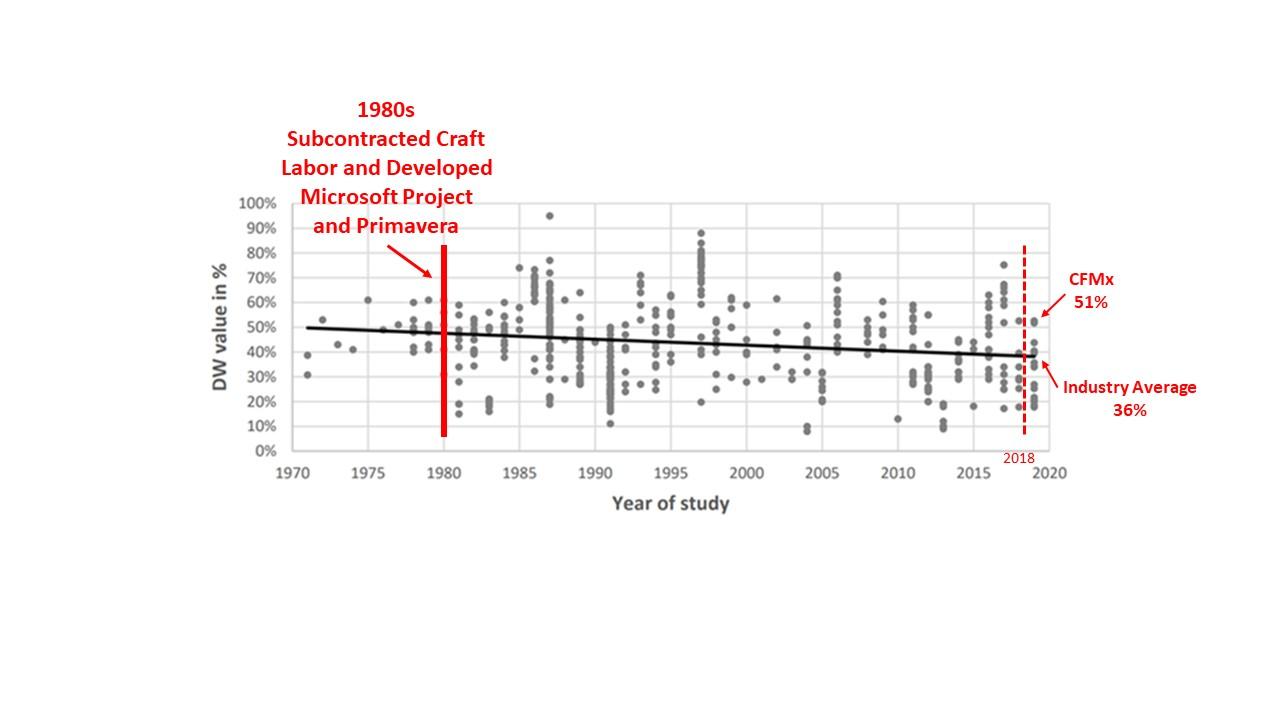
The Solution Is Clear And Balance Is the Answer
Using the Clear Flow Matrix (CFMx), trade partners are able to focus on both flows (process and operations), enabling them to balance process handoffs and allow for the pace of production to return. There is clear direction to their preparation efforts and sustainable flow is the logical result. Focus can then be directed to ensuring work is completed at the right place and at the right time, resulting in smaller handoffs, smaller crews, and reduced variation. This then restores the 50% direct work average by returning to the methods used when trade foremen and job superintendents successfully managed with production rates versus schedule dates. And, of course, the No Flow Circle is simply no more.
Keep Your Jobsite Clear!