Takt Planning and Takt Control (TPTC) is the most widely used standard production system for what we call Takt in the construction industry. In this publication I am diving deep into the second half of the system as there is extensive content on Takt Planning.
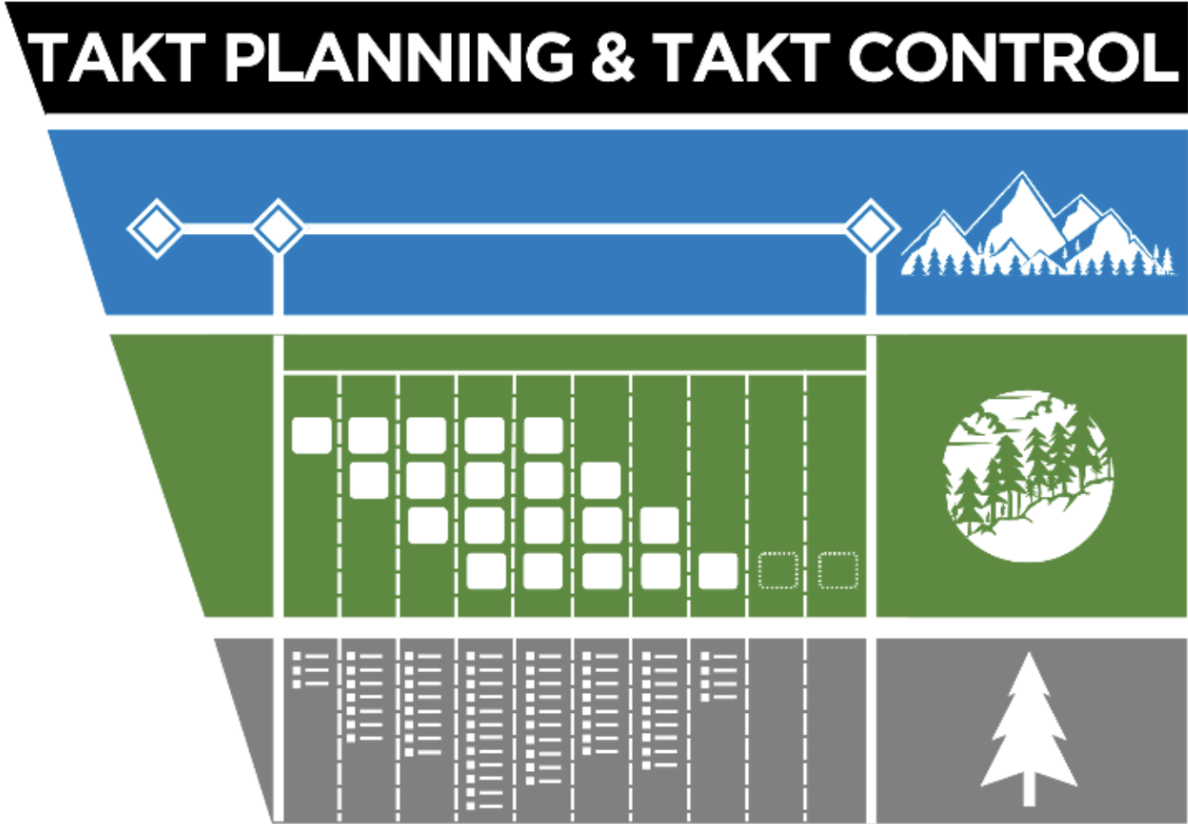
Initially there was not a production system when we were referring to “takt” but it was started as more of a method for planning the work to a constant pace. To be precise with language it was really started as common cycle time planning but called Takt Time Planning. The idea of Takt Time was technically semi highjacked as what we can perform has nothing to do with the actual definition of what takt time is. The initial professionals and academics that applied Takt to construction did reference this in their writings and research. Folks like Adam Frandson & Iris Tommelein (see their work here ) Janosch Dlouhy & Marco Binninger (see some of their work here ) or Aleksi Heinonen , Olli Seppanen (see some of their work here ). Or even the work that was done in the early 2000’s by Dr. Michael J. Horman in which he referred to as SIPS (see his final work here ) or even decades before that by Alvin Bukardt (see here ) and the list goes further and further back to 1954 (when these concepts were truly invented). But most of them up until the introduction of TPTC mainly focused on the Planning side. There was reference to production or management of the field/work, but the main focus was the planning and what did happen based on that. Most of them concluded further development and testing in the field for production was required.
Enter This influential paper titled “Technical Takt Planning and Takt Control in Construction” in which they (Binninger & Dlouhy) describe not only the detailed method of Takt Planning but had the first attempt to answer the question of “What is Takt Control” (I will be using this research paper and my experience to answer this below so please refer to this original document as the source as the original authors).
It might be easier to start with setting the record straight as there are many out there who have assumed that Takt Control is a ton of different things. Here is what Takt control is not:
- takt control is not- Preparing: Materials, upcoming work, or standard work steps
- takt control is not- Managing Delays
- takt control is not- Last Planner System or using components of Last Planner System with Takt
- takt control is not- a Checklist of Quality
- takt control is not- 5S
- takt control is not- focusing on better communication, improving meetings, or team health.
- takt control is not- Trouble Shooting, or Jidoka (seeing the abnormal and getting it back to normal)
- takt control is not- Cleaning or Organizing
- takt control is not- The focus of clearing the path for construction to flow
- takt control is not- Collaborating between people
- takt control is not- Design, DFMA, or Prefrabrication
- takt control is not- Any type of planning, re-planning, leveling, or packaging of work
- takt control is not- tracking the use of buffers
So, what is Takt Control?
Takt Control, also known in manufacturing as shopfloor management, has the goal of placing production control at the place of value creation as to limit WIP, increase Throughput, by tracking the cycle times of each step, and placing limits (control) on the resource utilization of the entire construction project.
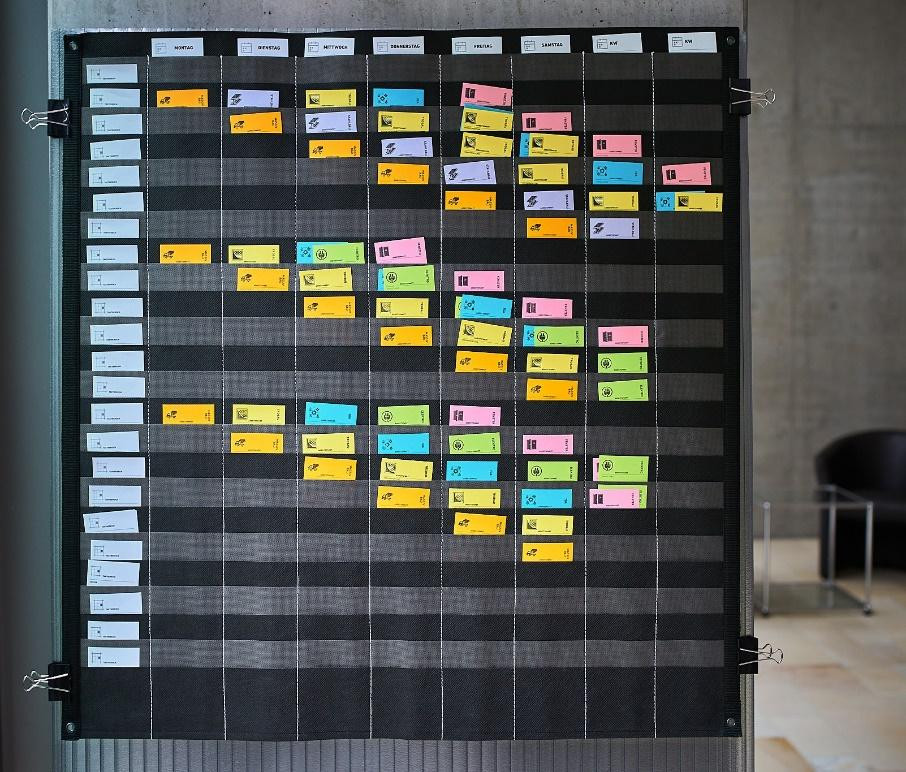
Currently there is 1 Major Control Process, and 1 Major Control Mechanism in takt control.
Major Control Process #1: Short-cycled shift meetings
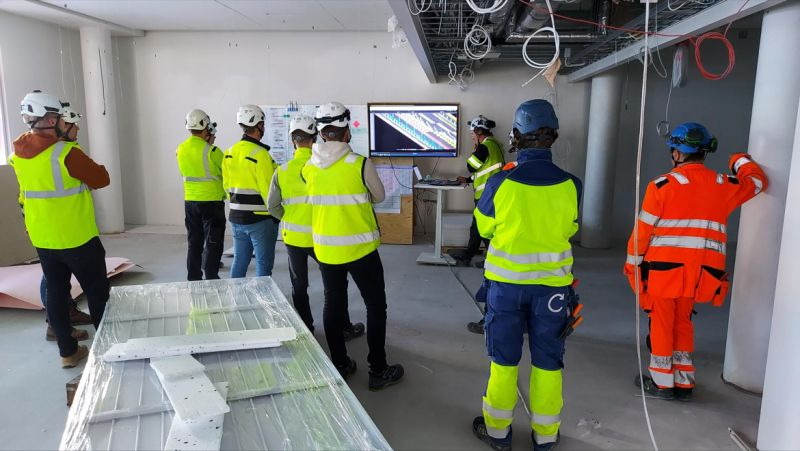
Short-cycled shift meetings are at the core of “takt control”. The construction manager (PM, Site Supervisor, Superintendent, etc.) leads this meeting, and all persons responsible for execution should take part. This does change the typical construction management system on its head and creates a team goal instead of how fast change each independent crew or task go.
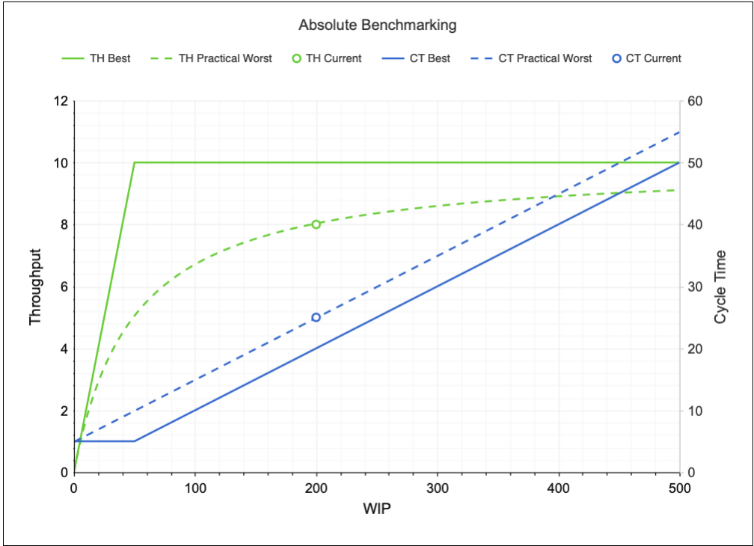
This is the check in and/or check out for the shift and should serve to control how much WIP at any given time the construction project is experiencing. If too much work is released into production, then our takt control process is not working, it must limit WIP as to increase throughput. That can be tracked overtime.
Major Control Mechanism #1: Takt Control Boards
Another adaptation from manufacturing is the use of shopfloor boards (Takt Control Boards).
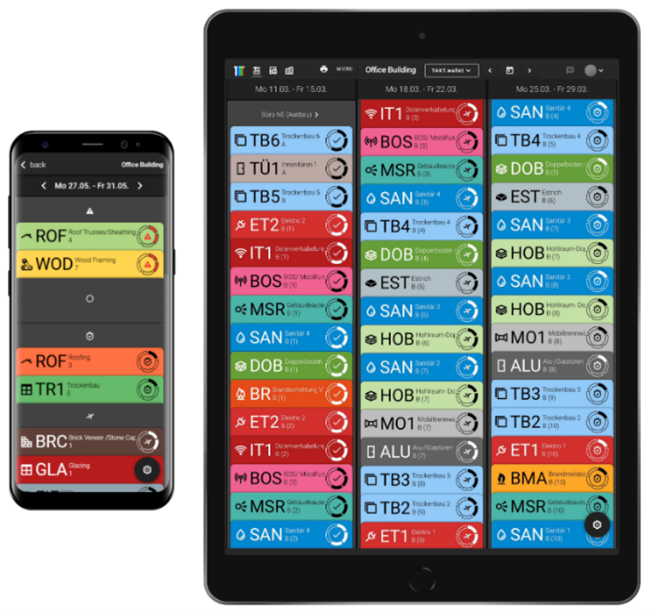
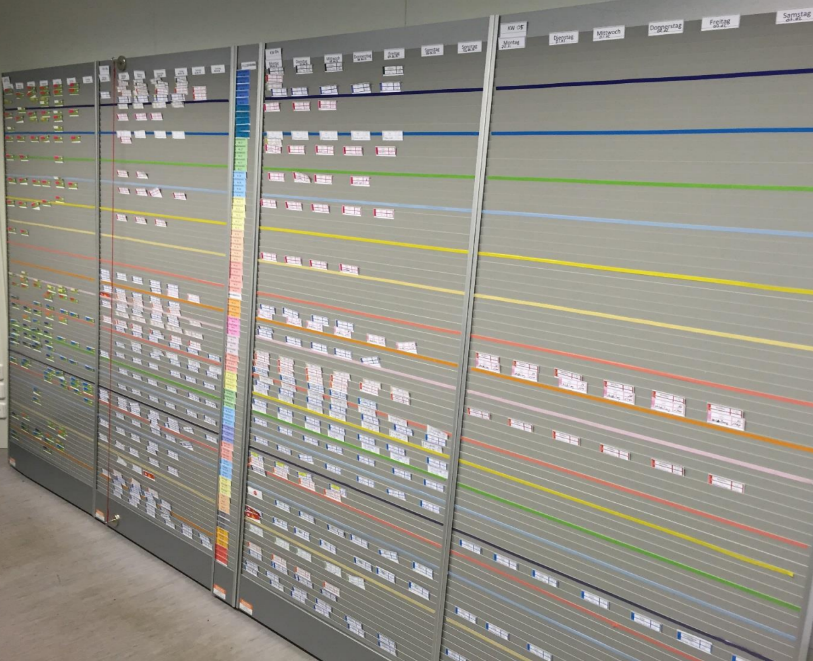
The board ( digital or physical) is used as the Control mechanism when it comes to what others call production control. Much like other control processes this is the tool that helps us to release or constrain (control) the amount of work the construction project has at any point in time. If you have done a good job in the Planning portion of TPTC then the work should be leveled and constant across the work sequence (Train, or production line). As such the flow of production should ideally be cyclical, constant and continuous.
As part of this mechanism, data from the work package has historically been collected to help other processes and to try and understand what is happening in the field.
- Number of workers per trade (Per Shift)
- How many Pieces of Equipment
- Rate of compliance with the Required Production (Cycle Time of Task)
- Defects in quality
- Safety figures, number of accidents, violations of safety rules
- Number of disruptions to work
And so on
Control vs Controls.
A great paper dives into this and is key if we are to understand and take away from the above how using takt control (production control) could eliminate a ton of non-value add extra processing we are doing every day in construction. The title is “Contrasting Project Production Control With Project Controls” and if found on the Project Production Institute. I have been an active reader of their content since 2019 and love their fundamental concepts (check them out here ).
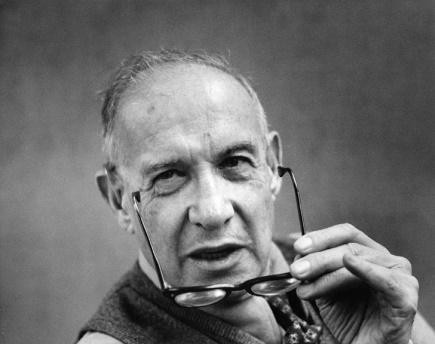
“While the main function of Project Controls is to satisfy project accounting and reporting requirements, Project Production Control focuses on how work is… executed” ( H. Jame Choo ) goes on to say in different presentation about Kanban and the misconceptions of this widely used term. He describes that Kanban is really (as it was created by Toyota) a limit set on the movement of material… in other words it was a control mechanism on how much inventory was allowed into production. Watch the full video of James Choo diving into this as I feel it is one of his best (and that is saying something).
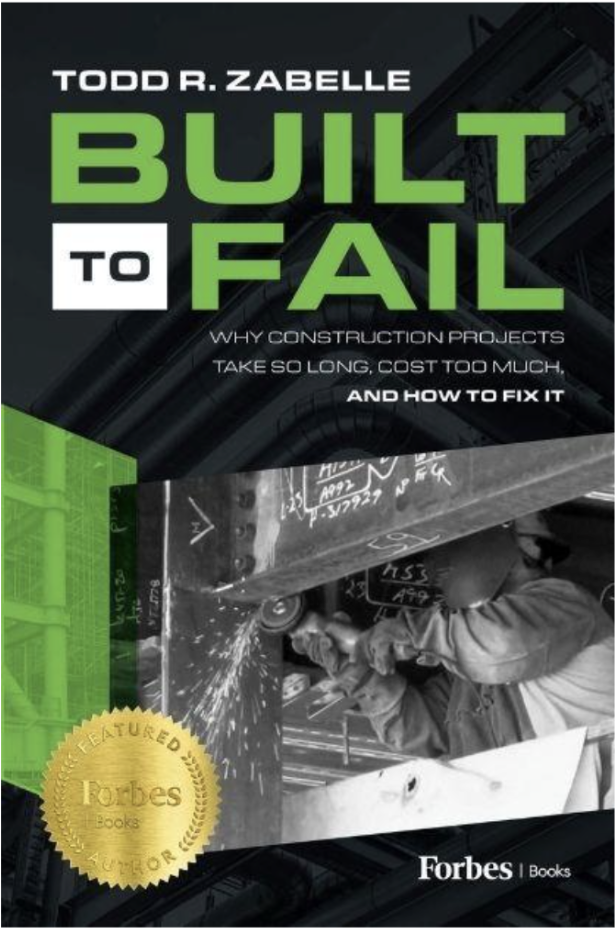
Another very noteworthy reference from the production control side of things
is Built to Fail a great book by Todd R. Zabelle that is one of the best
books this decade and summarizes a lot of the concepts from PPI and the
Project Production Control (PPC) community. I reserved a copy the moment you
could pre-order and started sharing and posting about it across social media
and the folks I interact with at work.
Quoting Todd out of his book:
“Production control is any action, process, mechanism, system, or
combination that organizes and enables control of production, or work
execution. Production control uses physical, software, and human
decision-making for the control-to-control production routings/sequence of
work, use of capacity, and the amount of inventory, including WIP".
By physical we mean actual devices that control what happens, much like the plate that forms the size of the entrance to a baggage scanning machine at the airport, or the number of cranes on a construction site. Control means actual allocation of capacity, management of minimum and maximum levels of WIP and management of variability. It is important to understand the various control protocols, schedule (known as push), pull, and constant work in process, or CONWIP, including how each works.
Push systems use predetermined schedule dates to release work into the production system. Though most widely used in construction, push, or working to a predetermined schedule, is not effective means of control due to the impact of variability.
Pull System was developed by Toyota, the pull control protocol is based on the downstream operation sending a notice-or, in the case of Toyota, a kanban card—to the upstream operation to produce.
CONWIP control protocol sends a signal to the beginning or near beginning of a production process and, in so doing, controls the WIP between the operation that initiated the signal and to the operation where the signal was sent.
Lean experts go on about push versus pull, but as Mark Spearman says, "Push, pull, what's the point. The objective is to control the WIP."
Takt Control is a type of Production Control

Takt Control then is the work execution adherence to the takt time through the lens of production control. It can serve us as a method to leave the hyper focus/investment of time and money in command and control, project controls, forecasting and scheduling systems behind us. Moving towards a more production management-based approach. From focusing on dates to focusing on rates.
Again, Quoting Built to Fail:
“The most effective project production control solutions combine standard work and CONWIP, enabling synchronization of work through the production system. This results in effective control of WIP and use of capacity that, as you now know, reduces duration, cost, use of cash, and risk while improving quality.”
The Standard Work is the other side that is scalable if you focus on what the work is. This is the idea of there are a myriad of things that one task must go through, and some conflate the make ready process (from Last Planner) with field execution processes like production control. If you have planned the Standard:
- Work Steps
- QA/QC Process
- Safety Measures
- Logistics
- Design & Engineering
- Bill (or Quantities) of Materials
- Handover
Then this next part starts to make sense. You conclude there is unit of work that can be our standard base unit of steps or tasks in our production process.
This concept is known as a Work Package, and is the at the heart of Production Control. So too it is at the heart of TPTC as well. Applying a bit of the underlying concepts of AWP which is the standardization of the concept of the work package; we can start to use that as a jumping point to get into Project Production Control.
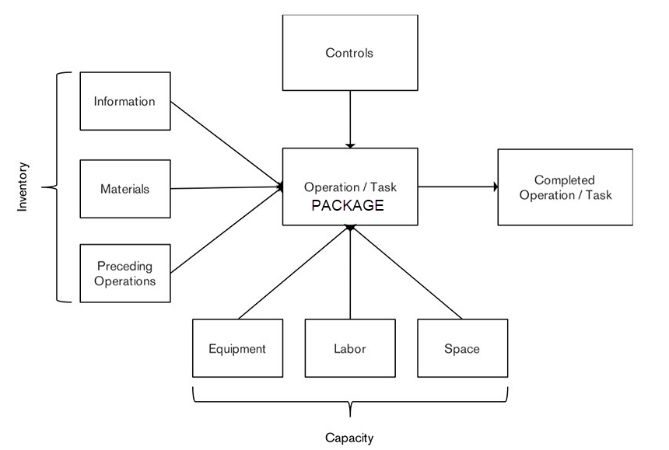
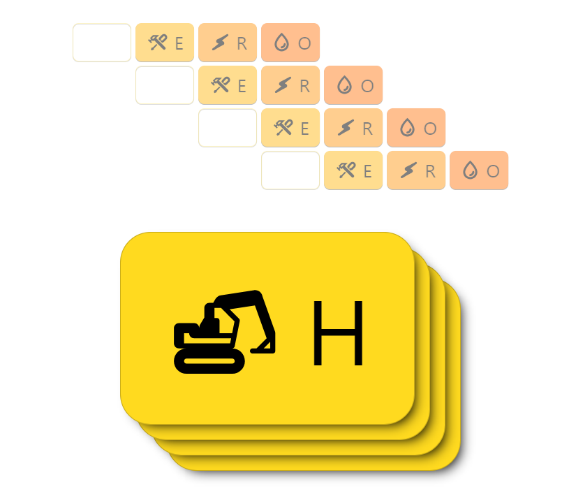
“Work packages are the scalable standard for construction processes.”
“All data is structured around it, and all workflows are designed inside the work package.” Takting.com
With the standard work component covered by the Work Package, CONWIP becomes much easier to scale and can affect the true triggered control with upstream work, inventory, and processes to the actual production on the jobsite. This is not usually the focus of folks attempting to try out “takt” as they usually searching for a better way to schedule their work. I have a great example of a Mega Data Center project that did not have a CONWIP protocol in place and their delivery of prefabricated assemblies. Before they knew it (a matter of 2-3 weeks) they had the whole projects inventory of specialized prefabricated assemblies on the project with no where to store them but in the way of the current WIP. After meeting with them and the supplier to look at this; they harmonized these two. However, they did not fix the underlying problem as all they did was try to align the forecast better to what the field was doing now (which could change). What they are still (even to this day) missing is a CONWIP control mechanism/protocol. So the concept of Pull or CONWIP would be the actual fix for this team that would control based on production the release of prefabricated assemblies to the field.
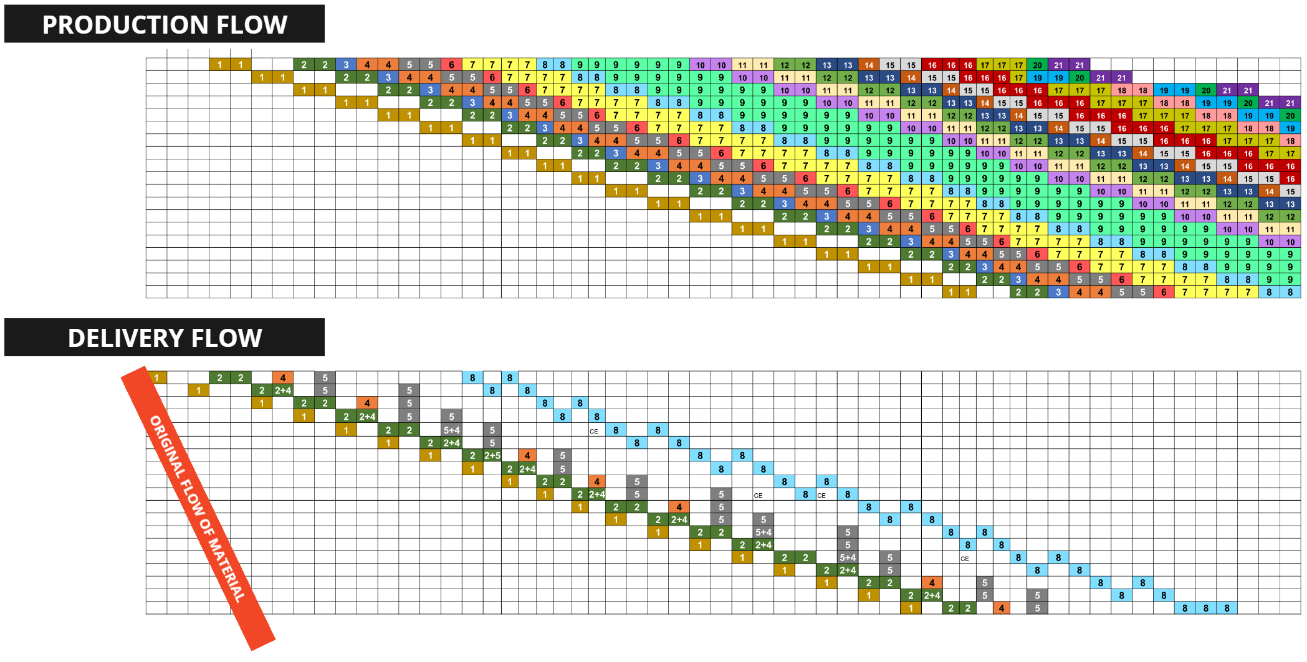
Steering Buzz Word & Visual Misconceptions
Whenever I hear Takt Control I usually hear the term Steering thrown around. Steering is much like saying return to green. If red means anything abnormal, like overproduction and underproduction or any sort of variation from standard. Also known as the made-up word by Toyota to describe this “JIDOKA”.
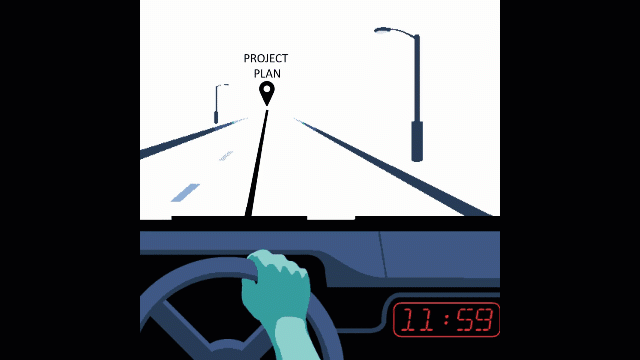
Steering is the effort to attempt to get back on track in micro adjustments. A metaphor I think of for steering is like when you are driving a car, you are constantly making small micro left and right adjustments as you drive. The lanes might even represent the takt time. So, while steering could be considered a connected process, it is not a control per say. Rather it is considered a practice where our efforts would adjust one way or another to help us get back to normal (RTG).
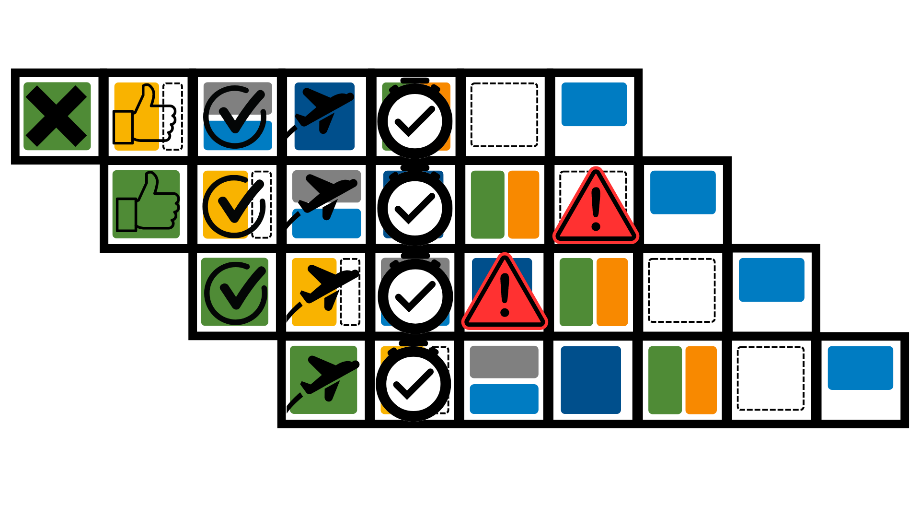
Some have also started to conflate the attempt of visual management combined with Takt Control and miss the understanding of the concept all together. As part of the traditional method of Preparing (Make Work Ready Planning)the work, and seeing where we might have Roadblocks (constraints) in the future is a process we can start to think that is the process. Since we might even use these types of processes in conjunction with the Takt Control Board but is a secondary feature it can become hard to remember the reason for Takt Control is the control of WIP.
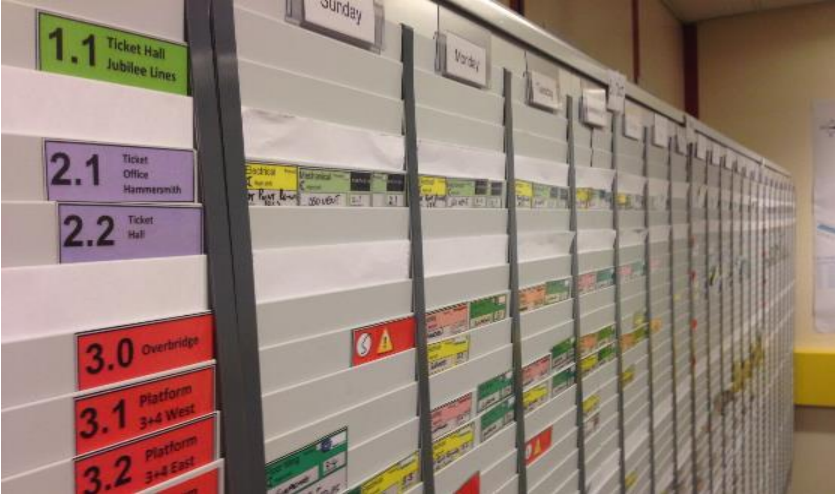
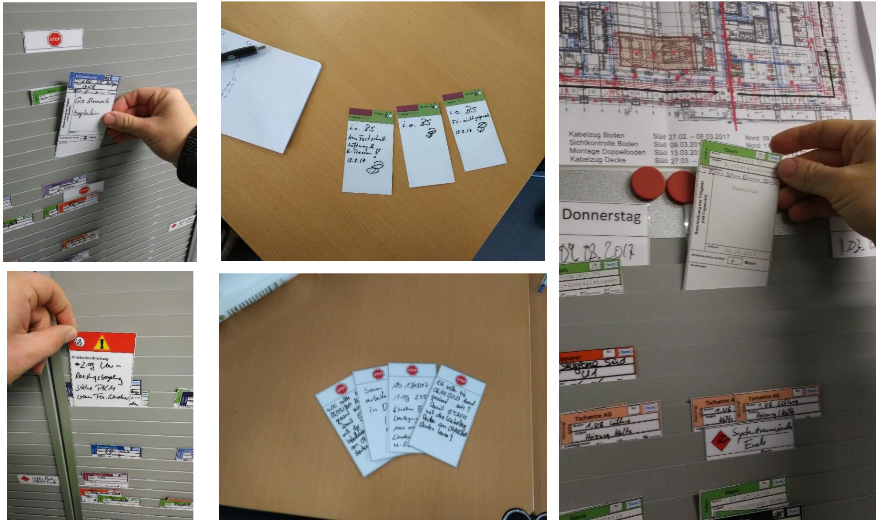
In closing Takt Control is a method of Production Control. TPTC is the attempt of some to achieve the production planning through to Production Control. One might call TPTC -> Production Planning and Production Control.