If you are involved in the delivery of capital projects, there is a good chance that you may have heard, or even used, expressions such as, “We have a resource-loaded schedule,” “We are behind schedule, so let’s add more resources,” or “We need to increase our capacity.”
Knowingly or unknowingly, the use of such expressions—as well as many others—may have developed specific mindsets across the global engineering and construction industry. For instance, a resource-loaded schedule is typically framed as a schedule that has workforce quantities added to some or all its activities. Because workforce refers to labor (either knowledge or craft), this has created a situation where resources and labor are often used interchangeably. Furthermore, those that intend to increase their execution capacity typically look to add more engineers, craft labor or equipment, so terms like capacity and labor also end up being used interchangeably. If we add equipment and materials to the picture, we get a conventional view of resources (labor, equipment and materials). So, nothing new there.
However, as the global engineering and construction industry transitions from conventional project management to a new era where better project performance is achieved by looking at projects as production systems, a more robust perspective for what resources, capacity and other terms are must be introduced and further explored, including how they are related to each other.
Resources - A resource is a stock or supply of money, materials, staff and/or other assets that can be drawn upon by a person or organization to function effectively. An operation will require the use of one or more resources to perform the transformation. These resources include raw materials, sub assemblies, components, labor, machines, information, intelligence, energy and fuel, among others. (Source: PPI Glossary, 2024)
The technical basis this article uses to examine these terms and their relationship is project production management, which is the application of operations science to projects. In essence, this perspective separates the elements of resources that are used to perform the work from the elements of resources that the work is done to (FIG. 1).
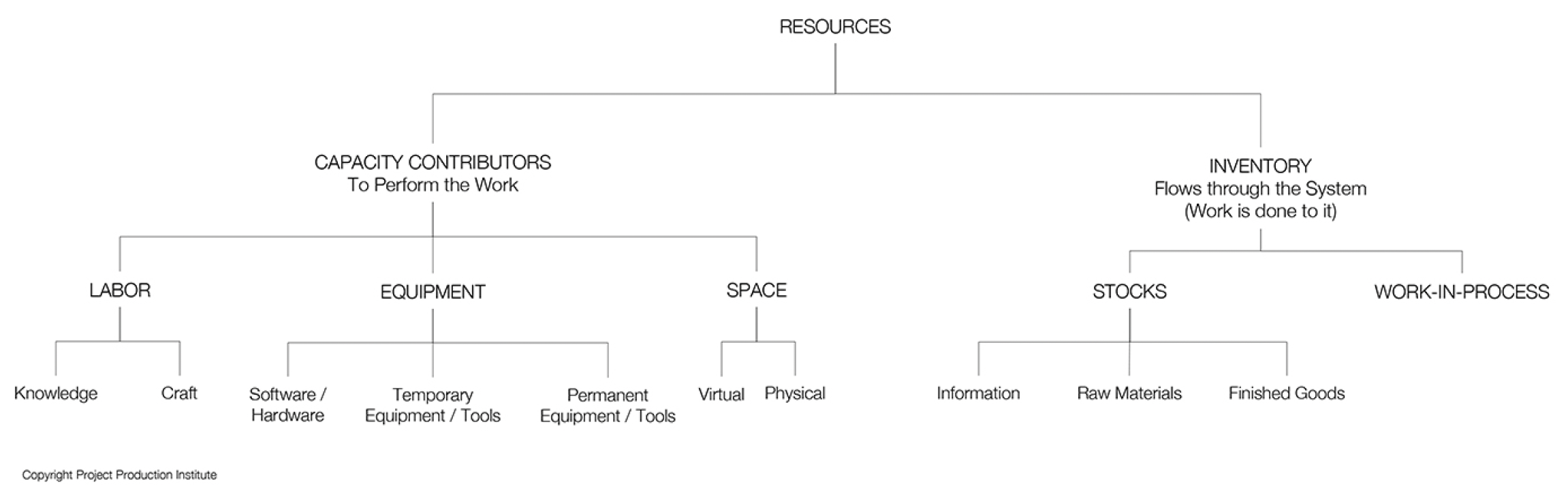
The elements of resources that perform the work are known as capacity contributors. As transformation occurs in any project production system, there are three capacity contributors: labor, equipment and space. Labor includes not only craft labor focusing on operations such as fabrication, assembly, installation and commissioning, but it also refers to knowledge workers, such as engineers, across multiple disciplines. In production processes such as engineering, equipment refers to computer-based tools and software, while in physical production processes, it refers to temporary equipment used for installation work, permanent or temporary equipment used in fabrication and assembly processes, and hand tools.
Why is space a capacity contributor? The reason is simply because you may have access to the other two capacity contributors (all the labor and equipment you need to perform the work or even in excess of what you need), but if you do not have access to the space or are unable to get the required labor and equipment in the space you have, you will be unable to produce the desired throughput. Basically, access to the right amount of space contributes to the capacity of a given operation or an entire production system. Capacity here refers to a rate, one that represents the maximum throughput of a given operation or production system and is expressed in units over time. Based on this, capacity and resources should not be used interchangeably, as they have different meanings altogether.
Capacity - The maximum average rate at which the items, units, tasks and/or products can flow through a process or system. Capacity is the upper limit of throughput. Having installed capacity above average demand allows the stock inventory and backorder time buffers to remain small. If the process had infinite capacity, there would be neither stock nor backorders, as the process could satisfy demand instantly (Source: PPI Glossary, 2024)
In contrast with capacity contributors, inventory moves through the production system, so work is done to it. When people hear or use the term inventory, it is typically in the context of stocks of raw materials (such as parts and components), finished goods (e.g., sub-assemblies, permanent plant equipment) and information (such as drawings, 3D models and engineering packages).
Inventory and stocks are commonly used interchangeably, like capacity and resources. However, inventory is not just stocks. Inventory includes another important component in production systems known as work-in-process (WIP), which refers to work that is either being processed by one or multiple operations, or work that is waiting to be processed between operations across specific boundaries in a production system. Together, stocks and WIP form inventory—thus, inventory = stocks + WIP. One should be cautious here as work-in-process is not the same as work-in-progress, even though they use the same acronym. While work-in-process is measured in number of units (e.g., number of piles, number of footings, number of pipe spools, number of drawings), work-in-progress is a measurement used in earned value management, typically expressed as a dollar amount or a percentage.
Next time you look at your project resources, keep in mind that they comprise much more than just knowledge, craft labor, equipment and materials. The more you look at how to effectively design and control your project production systems, the more you must account for capacity contributors and inventory—the production view of resources.