I have been reading and responding to a recent spate of posts on LC Blog and other sites in which professional construction schedulers extol the virtues of P6 and MS Project schedules, and assert that the Last Planner System® is a fake process that does not accomplish anything useful, and perhaps even misleads. A common thread is that Lean is derived from the Toyota Production System which was developed for and only applies to a linear, factory-based process, and not construction projects. They conflate improperly implemented Last Planner practices with the totality of Lean Construction, when in fact the LPS® is just one of 40+ Lean Tools.
The following is a response to the assertion that we have nothing to learn from Lean in the Auto Industry.
I certainly understand skepticism about whether “Lean” can actually be applied to the AEC industry, where production happens on projects rather than in factories. Of course, construction uses all sorts of components that are manufactured in factories, so their argument really stems from limited site assembly applications, but their arguments rarely make any such distinction.
When you have not seen Lean done well, nor seen the significant results that can be achieved, the efficacy of Lean Construction can be hard to believe. Many people at Ford did not believe that Toyota and Honda could complete product development, defined as concept development to first produced vehicle off the assembly line, in half the time (3 years) required by Ford (6.5 years). The “Big Three” American manufacturers were losing market share and going in the red while Japanese companies were taking market share and making great profits. Japanese vehicles provided better value for the dollar, with better quality and the ability to incorporate and offer new features and technology years sooner than their competition. Many at Ford literally could not believe it. I heard them say, “They must start measuring product development later than we do!” Or, “It’s not possible. We have been developing vehicles for more than 60 years and we know how long it takes!” These remarks exemplified the truism that our perceptions of reality are influenced by our underlying mental models that function as lenses in our view of reality. We look but cannot see.
Today’s construction industry is still organized the way US auto industries were in the 1980s: they had separate engineering organizations (Design, Engine, Chassis, Body, Manufacturing, Assembly Ops., etc.), each in its own building, with its own senior leadership tasked to reduce the cost of their services, with separate budgets, production schedules, staffing resources and incentive structures. Each with strict hierarchical management and “professional” leadership. Each vehicle “program” (a particular model of car or truck with a successive annual product life cycle of about 6 years) was driven by a dictatorial, but essentially powerless, “Program Manager” with a team of schedulers and budget managers, but no control over the project workers. Program (Project) management was yet another professional specialty in yet another building.
We in construction are in even worse shape. At least all those departments at Ford were part of Ford. We contract with completely different, very siloed companies that try desperate to defend razor-thin margins. We involve them as little and as late as possible thinking this will lower costs. We plan and budget based on data derived from how projects have always been done and not how they should be done to be more efficient. And we get the same old late and over-budget results.
Ford's Program Managers had very little power over resources working on their vehicle programs and were locked in power struggles with the engineering group's leaderships who loosely guarded their resources. Assembly Operations, therefore, were not engaged until vehicles were pretty much fully designed and their expertise in assembly innovation was lost to the design process, often causing rework and delay. People who know construction should easily recognize similarities to traditional Design – Bid – Build construction management. Toyota and others completely rethought not only the whole design process, but the whole organization structure, its leadership and the design of every operation in every process. Ford could not catch up using continuous improvement (PDCA) alone. They had to completely re-invent the way they developed products. They went from hierarchy to dedicated collaborative teams, from discipline focus to product focus, from activity focus to production system design based on TQM/Lean principles, like flow and pull.
In traditional construction every function is siloed, with separate contracts, and separate functions supposedly controlled by a PM Planner somewhere remote in time and location from where actual work takes place. All of this is organized by outdated concepts about construction and business management. It‘s time to reinvent.
Here’s an example of how this reinvention works in construction: in California, Sutter Health began to rigorously apply Lean Construction to its health facility projects, big and small. It pioneered a completely different contracting process (IPD or LFOA) that created shared risks and incentives, involved suppliers and constructors as early as the concept development/feasibility phase. They began to rethink every aspect by approaching each project as a unique production system that could be described, measured, managed, and improved. They changed how they led and put resources into dedicated, cross-functional teams in co-located facilities. Nothing about this was simply "low-hanging fruit".
They did this because before Lean, not a single Sutter project came in on time or budget despite having a P6 planner working hard. After their Lean transformation, not a single project came in late or over budget, as reported by their project leadership. Profits and savings were shared, the team members were proud and happy, and many industry-leading practices, such as TAKT planning, were proven highly effective when done correctly.
We can't transform the industry through piecemeal tweaks. Real Lean is about bold reinvention.
Lean Does Not Apply To The Construction Industry?
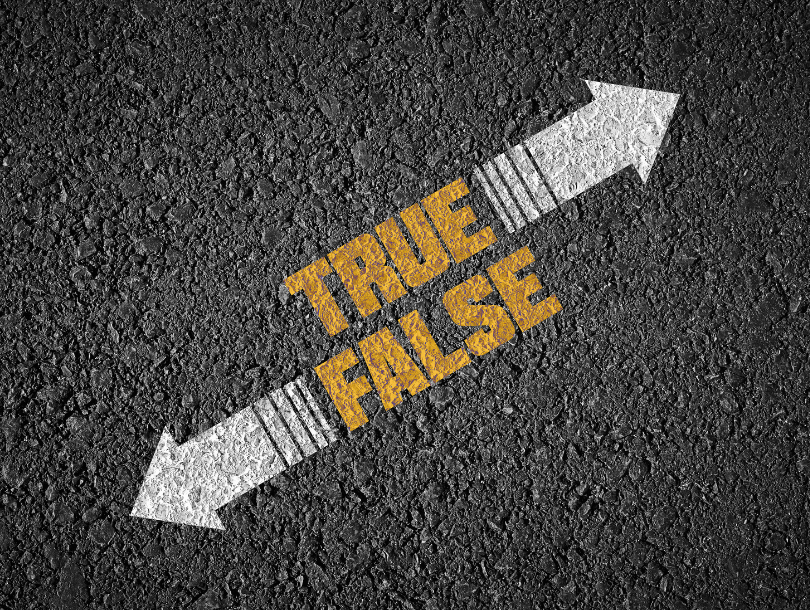