If you work in the AEC industry, the concept of lean is likely nothing new. However, putting a strategic plan behind your firm’s lean journey—which we call our “Lean Operating Strategy”—might be something you’re still working through. So, let’s discuss the strategy, tactics, and tools of developing a Lean Operating Strategy (aka “LOS”).
SSOE, an architecture and engineering firm with more than 1,200 employees, had dabbled in lean for many years. And with a large industrial client base, it more than made sense to apply lean concepts to our design projects. What we didn’t necessarily see coming is how lean would positively affect all of our projects and even our corporate operations.
The real game changer was an added focus on lean as part of our overall strategic plan in 2020. With a new CEO at the helm, we set forth to become a firm that doesn’t just provide excellent value to clients, but one that engages our partners in the holistic advancement of our industry. With a revised corporate mission statement in place—"to deliver unparalleled client value that advances the AEC industry”—we set out to define our LOS.
Tactics led by strategy (not the other way around!)
Recognizing that defining our LOS as the foundational element of our strategic plan was key! Since this was a crucial part of the framework to advance our mission, we knew it was necessary to break down this thought-shifting initiative into practical, achievable steps.
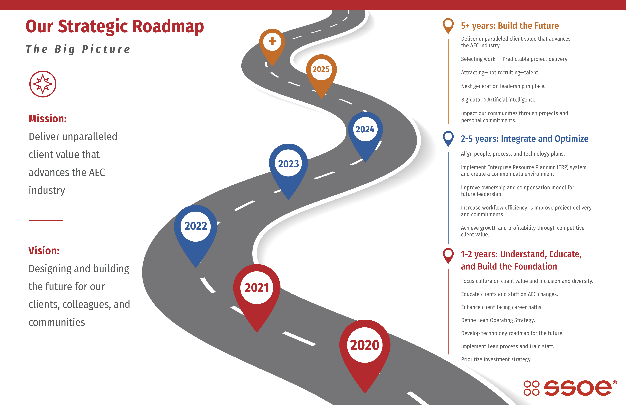
Enter our “Strategic Roadmap.” This 10,000-foot, visually mapped view helped break down what we needed to accomplish in the first two years, in years two through five, and into the future to achieve success and gain leadership (and later, employee) buy-in. At the same time, our CEO also set an ambitious and transformational goal for a 50% increase in production efficiency in just five short years to further drive lean thinking corporate-wide. This goal was included in performance metrics and measured by improvement in the ratio of profit to headcount (FTE).
Encouraging a lean mindset
We knew the path from concept to widespread adoption was not going to be an easy one. Our progress at first was slow, siloed, and inconsistent. We did not have an overall strategy driving the implementation and ended up with focus on specific tools without the understanding of what the tools would help achieve. With our 50% efficiency improvement goal in place and roadmap defined, we began tackling the looming challenge of having many employees with a minimal understanding of lean and very few lean practitioners in house. We decided this would have to be a cultural shift focused on mindset.
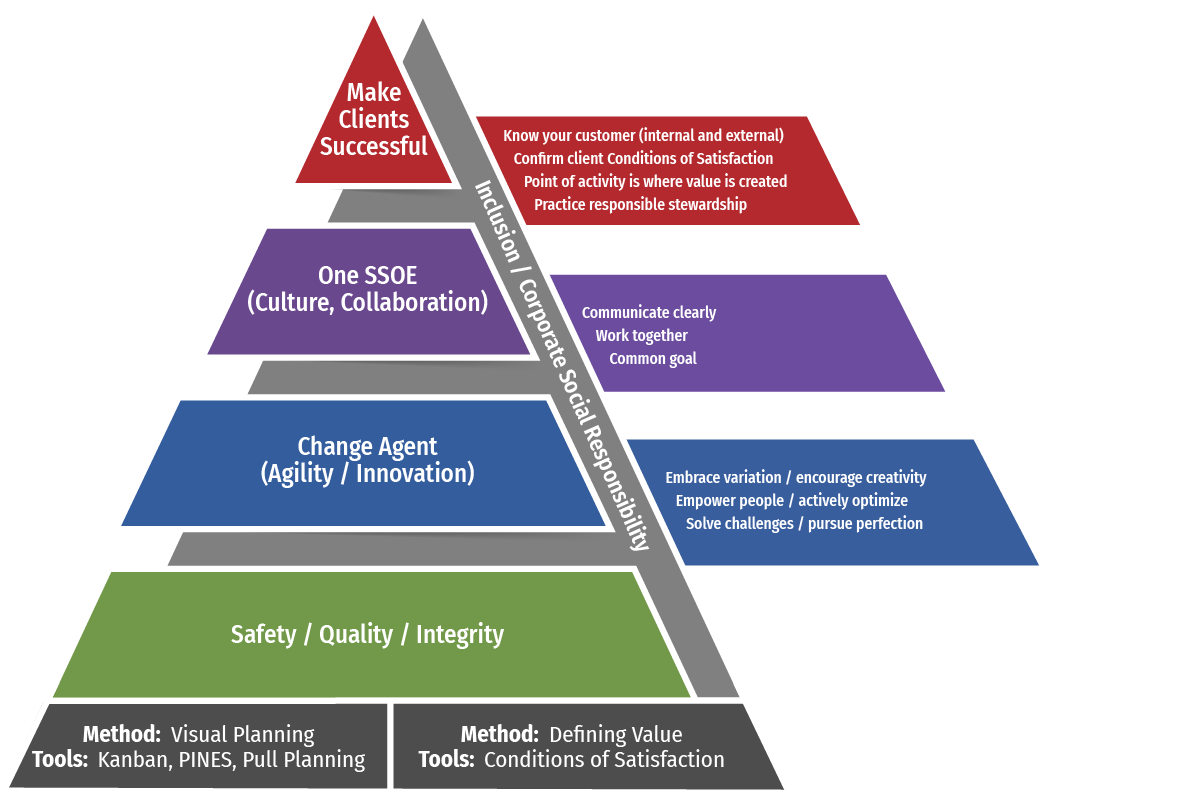
Other challenges included taking abstract concepts and making them practical, teaching a framework for thinking rather than a set of processes, a reliance on metrics that measure and reward resource efficiency, and most of our technical talent being too tied up in project work to participate in lengthy training. In the spirit of lean and to ensure everyone in the firm—from an electrical engineer in Oregon to a model manager in Mexico to a corporate accounting coordinator in Ohio—was hearing the same message, the leadership team rolled out what we defined as our Lean Principles to the entire company at once rather than by project or division. As we had implemented monthly virtual Town Halls during the pandemic, we were able to use one of the Town Halls to present the strategy as well as to answer questions from employees.
Evolutionary change and the power of agreement
We utilized various tactics to level the understanding of lean across disciplines and office locations. This included having leadership at various levels of the firm participate in Study Action Teams over several weeks using This is Lean: Resolving the Efficiency Paradox by Niklas Modig and Pär Åhlström, a book that challenges what many organizations believe to be “true efficiency” and what we ultimately used to develop the key components of our LOS. The effort centered on how we could evolve past being a firm that completes lean projects into a lean company with the potential to help advance the AEC industry. Our Study Action Teams followed the framework developed by Lean Project consulting to help teams understand new information and put it to use quickly. We divided our leadership team into two groups with each led by a facilitator. Each group then completed a specific reading assignment with a guided discussion asking two questions: What is the author’s key message for this section? How might this message apply to our work?
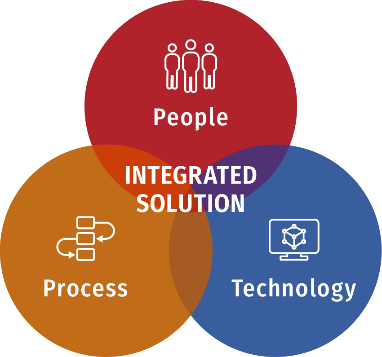
Other important tactics included the integration of our LOS with our technology strategy, which started by bringing together prepared people, lean processes, and new technology. We also took the large discussion of flow efficiency versus resource efficiency and turned it into tactical implications–specific actions in our strategic plan with owners and implementation dates. The result was increased collaboration, less sequential processes, and better use of BIM that resulted in an increase in our metric of profit / FTE—taking what could have been another initiative and creating a solution to a burning platform and impending disruption. Deep discussion ensured everyone was aligned on the journey, and our updated mission served as our North Star.
Leveled understanding
We’re currently in our third year of the plan as outlined in our Strategic Roadmap. The progress to our 50% efficiency improvement goal has been consistent with our initial plans (even during unusual circumstances like a once-in-a-hundred-years global pandemic). We’ve achieved the desired incremental increase in profit / FTE over the past three years to put us on track to meeting the 50% improvement goal. We now have our own in-house Lean Community of Practice (CoP) that provides professional development training and maintains our connection to the greater lean community. The CoP meets monthly in Teams as our members are dispersed through our various locations. We currently are using this agenda for our meetings: Agenda with prep details:
1. Something you've learned from your external Lean work (LCB, LCI, Curt, other) - please bring a relevant takeaway the rest of the group may benefit from.
2. A problem or challenge that you are experiencing regarding lean. Your colleagues will be ready to jump in with questions and potential ideas to help!
3. Celebrations/Successes - what's something great that happened in your work world regarding lean? Share the joy! Share the enthusiasm!
4. Share a Small Win that has been submitted from your group/team/department. Pick one that will likely be relevant and helpful for the others to hear and take back to their group/team/department.
Our focus on our lean principles has been a big part of enhancing the culture and mindset, helping us to advance the AEC industry from within. We’re striving to begin every project by defining value in our clients’ eyes through establishing Conditions of Satisfaction. While many of our industrial manufacturing clients use lean processes as part of their manufacturing strategy, very few are as familiar with applying these principles to design and construction. We work together to gather alignment as to desired outcomes and have found that the clear definition of these factors empowers the entire project team to work together to make decisions that drive toward a shared vision of value.
As with any significant effort within a large group, we have had challenges with consistent implementation. Resistance to change has been difficult to overcome, especially in a traditional industry. However, our shift from a focus on the use of specific tools to an understanding of a continuous improvement mindset allowed for needed variation between clients and business operations. We also were able to target a specific group of projects within an emerging market sector and under the umbrella of defining value and visual planning, have applied various lean practices to improve our results on these large, complex projects. This has led to positive acceptance of these practices and increased demand from other projects as they witness better work practices guiding the teams. We will continue to work under the continuous improvement mindset as we strive to better serve our clients while advancing the AEC industry.