Ever since COVID-19 pandemic hit, many challenges began to unfold, hindering different businesses including construction projects. Safety measures involving lockdowns and minimizing physical interactions were imposed to limit the virus’ spread. People are at the heart of designing and executing construction projects, especially when implementing the Last Planner System (LPS) which calls for collaboration among all project participants. So was the pandemic really a challenge for successful LPS implementation? Salhab et al. (2021) conducted expert panel interviews with industry practitioners who were implementing LPS during the pandemic. Surprisingly, the results revealed that the pandemic was an opportunity for people to rediscover Lean concepts and embrace LPS implementation, and participants were encouraged to work on LPS software.
The study also suggested a framework for successful implementation of LPS in a virtual environment. At the base of the framework lies ensuring top and mid management buy-in for lean culture and concepts. Having management people believe in Lean secures a Lean culture that encourages all participants to believe in LPS and to collaborate towards continuous improvement. It is usually challenging to convince people to abandon their traditional practices and shift their mentality to something new. An illustrative pilot study showcasing benefits of implementing Lean and LPS can make the mentality shift process smoother. After that, management should create a cross functional team.
As the paper (Salhab et al., 2021) quotes Liker (2004), “work groups are the focal point for solving problems.” Bringing together people from different disciplines and trades serves the company in resolving issues and achieving improvements. More important are the training, training, and training! Providing teams with training on different LPS concepts and tools, communication platforms, etc., makes the process more effective. During the pandemic, a handful of online platforms that allow screen sharing became common. Training people on how to use such platforms is beneficial especially when facing technical issues. Moreover, virtual lean simulation games educate people and provide them with hands-on experience on Lean and LPS concepts. Following should be executing Value Stream Mapping (VSM) of the company’s current planning process to uncover undesirable waste and potential improvement opportunities. The teams can achieve this collaboratively using any online communication platform and a simple drawing tool.
An important step in the framework is exploring available software for online LPS implementation. Each software has specific characteristics. The company should define first what it is specifically seeking in a software. Then, to ensure that the company has a good understanding of the software features, it is recommended to have a representative from each software company presenting their features and answering to practitioners’ tailor-made requests. After this, the company can use a decision-making tool such as Choosing By Advantage (CBA) to decide on the software most suitable for their needs.
Again, a crucial step is to provide all participants who will use the software with proper training. It is not only influential to have a tool, but also to make proper use of it. Next, to complement the planning process with a control process, a dashboard of various metrics that allow evaluating performance of the project should be created and integrated with the LPS software. Having completed all this, the company can implement a pilot study on a new project or apply it to a project phase. When seeing positive results, the teams will have a stronger buy-in. The company should also standardize work through a drafted work methodology such as specifying frequency of meetings, lookahead window, daily huddles, etc., to stabilize the way of doing things for less variability and more efficiency.
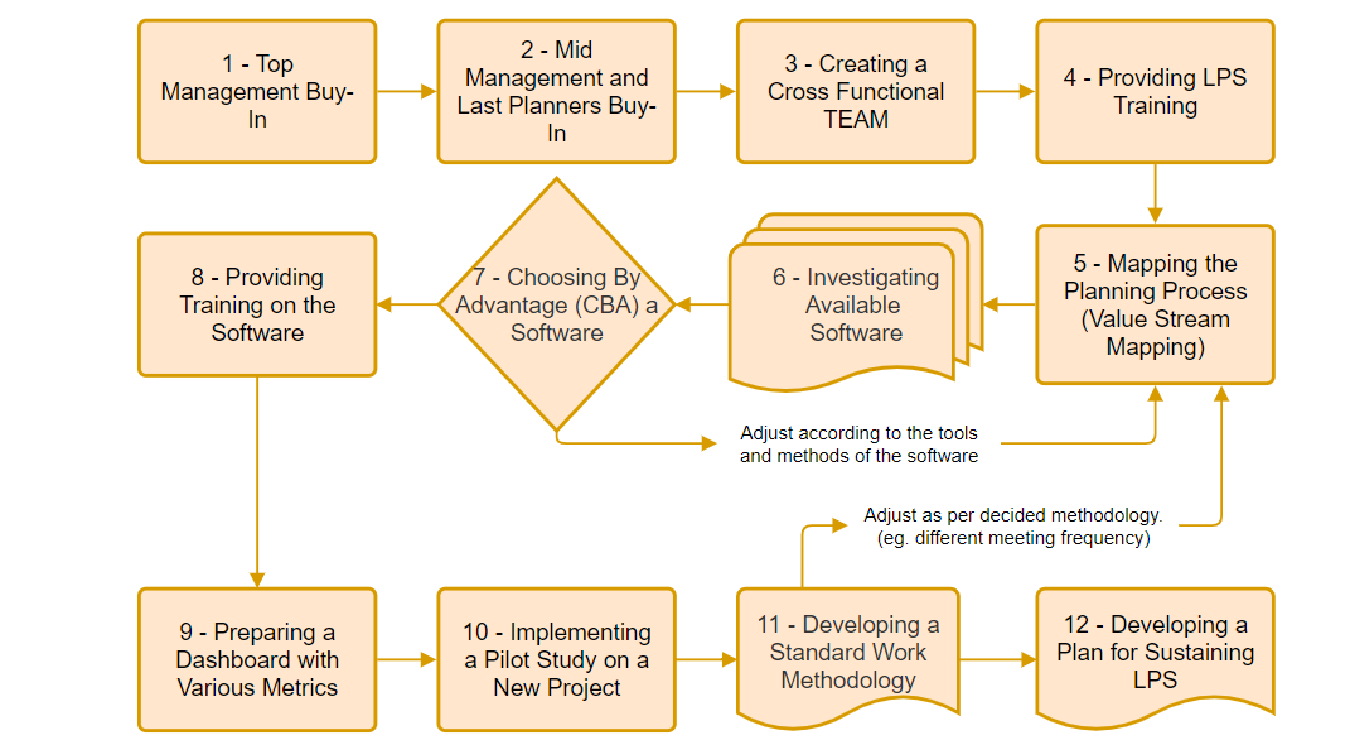
Fig. 1: The suggested framework adopted from Salhab et al. (2021)
Finally, it is critical to develop a plan to sustain LPS so that efforts are not wasted. Management can achieve this through investing in different tools, software, workshops, etc., and embedding LPS standards into their work methods. The framework is summarized in Figure 1.
References
1. Liker, J. K. (2004). “Toyota way: 14 management principles from the world's greatest manufacturer.” McGraw-Hill Education.
2. Salhab, D., Noueihed, K., Fayek, A., Hamzeh, F., and Ahuja, R. (2021). “A Framework for Implementing the Last Planner® System in a Virtual
Environment.” Proc. 29th Annual Conference of the International Group for Lean Construction (IGLC29), Alarcon, L.F. and González, V.A. (eds.), Lima, Peru, pp. 75–84, doi.org/10.24928/2021/0179, online at iglc.net.