We need to let go of our antiquated thought patterns and, in some respects, take a leap of faith into the unknown. Artificial intelligence can maximize effective communication and networking of people, information and machines and optimize processes and projects. Lean provides the basis for futuristic technologies and fosters optimization. Lean is also key to achieving standards and stability – and stability is the basis for general digitalization. Only stable and recurring processes can be digitized.
Digitized processes provide the foundation for the main AI topics, such as:
- Machine Learning (ML): uses math and statistics to learn from data; improves with experience.
- Deep Learning (DL): uses artificial neural networks to solve complex tasks.
In the context of takt planning as a common scheduling method in lean construction, the potential of these two emerging technologies can be leveraged as follows:
- With ML, takt plans can be generated autonomously based on previously collected empirical data. However, humans are still needed in the loop for validation.
- With DL, takt plans for projects are created entirely autonomously with no humans in the loop.
Lean principles are increasingly supported by applying larger, more complex datasets, which is why the future of lean and big data is connected. The ability to evaluate data correctly, to derive measures, and to improve processes will be decisive for the future competitiveness of companies in the construction and real estate sector. Therefore, companies aiming to sustainably position themselves in the market require data management, e.g., in the form of a data warehouse – a construction information database for optimized, efficient and quality-assured project handling and improved management processes.
With the growing complexity of projects, data warehousing is becoming increasingly crucial. Taken together, sustainability requirements, increasing cost pressure and the need for shorter project cycles all but simplify the construction process, despite all the technologies already available. As a consequence, engineers and technicians are challenged to master increasingly complex challenges. Therefore, artificial intelligence in connection with the associated future-oriented technologies is the solution of choice when it comes to managing projects across the planning framework.
Holistic process systems that are able to sustain and improve synchrony in implementation in a structured way have the potential of taking lean to the next level and possibly being even more disruptive. Visualizations and processing of project-related data streams as well as smart connections between dependencies and influences lead to autonomously created project or production plans. Through artificial intelligence and real-time data, a project can constantly learn and potentially develop into a platform that does everything autonomously. We may not know for sure, but we need to position ourselves today to be able to change for the future.
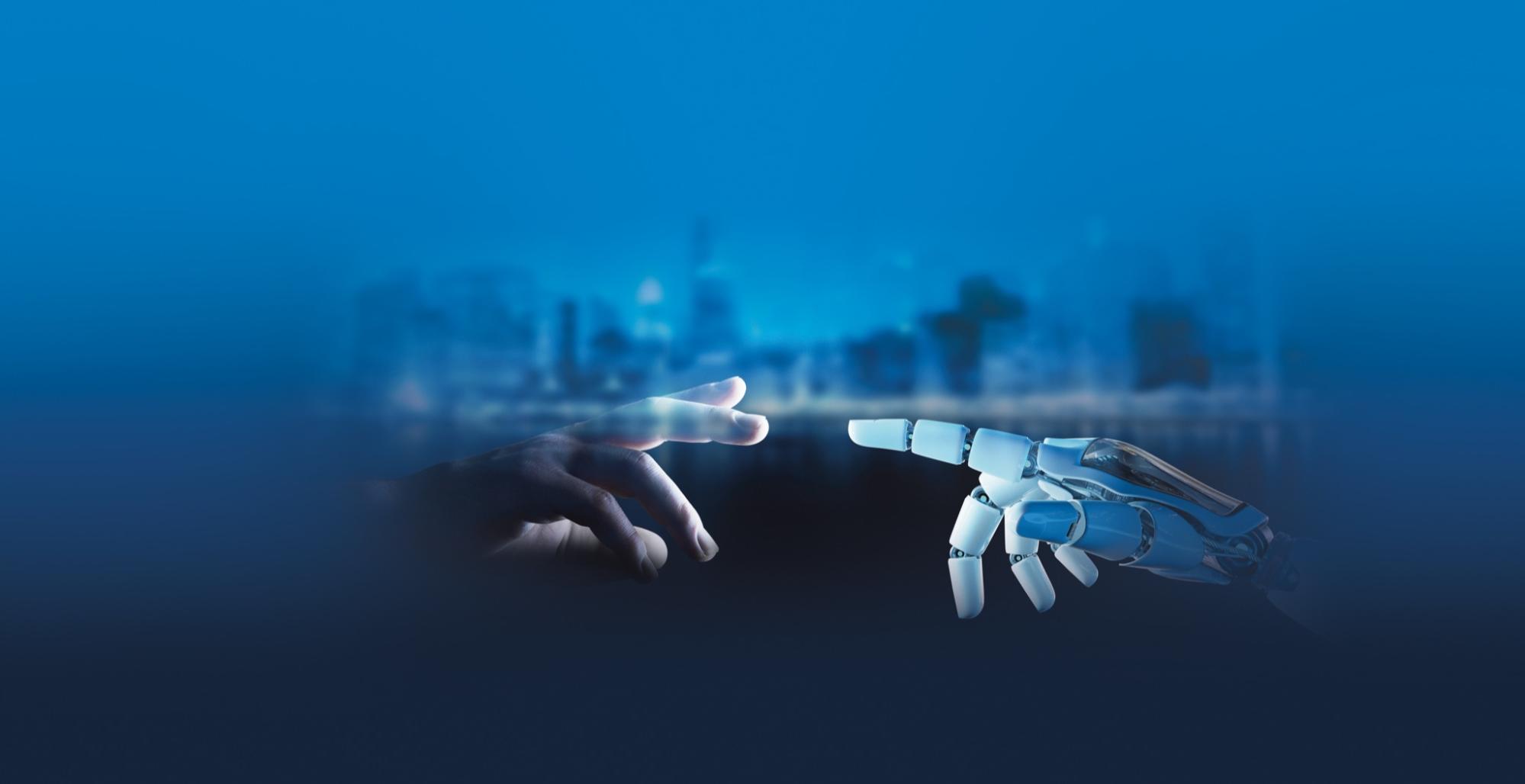
Lean management in construction is in itself based on a very simple idea: implement processes with maximum value and without waste. However, implementing this simple idea in the construction and real estate sector is a very complex endeavor. This is where data comes into play. Without data, lean practices or operational excellence efforts are mostly based on estimates and projections. A common way of looking at lean advocacy is to think of construction as production, and, in extension, to think of a construction project as a temporary production system. However, if we want to draw this comparison, we must understand that construction is one of the most complex production systems. In this logic, lean construction requires big data.
If we succeed in embedding lean culture in the corporate DNA, not only incremental improvements but also radical innovations will emerge. Lean constantly challenges the status quo, as efficiency and effectiveness are simultaneously increased. Artificial intelligence can make a significant contribution to this. But only thanks to lean is it possible to strike a balance between people, data, and technology.